The potential of cheap herbaceous biomass to enhance the environmental performance of coal fired power plants was the focus of study for Yash Joshi of the Process and Energy department at the Mechanical, Maritime and Materials Engineering faculty (3mE).
Energy firm E.ON Benelux, the coal plant owner at Maasvlakte, funded the research. “We are very pleased with the practical applicability of this research,” said Henk Bak, Corporate Development Manager at E.ON, before Joshi’s PhD defence on November 19. And it was timely, as the following week 64 professors in an open letter called for all Dutch coal plants to be shut down to tackle climate change in the context of the forthcoming Paris climate conference.
Electricity producing coal fired power plants can pollute less by co-firing renewable carbon neutral biomass fuels. Existing power stations do not have to be substantially modified. Currently used pellets from wood and forestry industries cost up to six times as much coal on an energy basis. They have been co-fired in fractions of 10% or more but they have not been used by industry without subsidies. Joshi searched for renewably sourced, cheaper fuel options not reliant on subsidies to ramp this up to 20% biomass content on an energy basis.
He studied verge and landscape grasses and bagasse, a by-product of the cane sugar cane industry. These cheap alternatives, with existing centralised collection, put no demand on agricultural land used for food crops. “But you have to know your fuel and prepare it for optimal combustion with pulverised coal,” he said.
First, mechanical de-watering reduces moisture content and leaches minerals, reducing the amount of ash and improving its quality. Thermal drying further removes water before torrefaction. Also known as roasting or mild pyrolysis, it occurs between 230-300ºC, improving the properties of the fuel and maximizing the energy yield. About 30% of the mass is lost but the energy content remains around 90%. The torrefacted biomass is less prone to reabsorb moisture and be attacked biologically and can be pelletized and stored.
Joshi proposes integrating the heat and mass flows of all pre-treatment steps. He found the greatest net system efficiency with lower torrefaction temperatures, which have the least mass loss of the fuel. Drying has the greatest heat demand and should make use of a low grade waste heat source.
To better test the scaling up of the technology and gain operational experience he carried out experiments with a bench scale drying and torrefaction test rig. He also used it to study the effect of possible air infiltration in the torrefaction process. Sometimes this can contribute to more uniform heating of the biomass bed. But he also identified thresholds beyond which safety can be compromised by an oxidative thermal runaway. In layman’s terms, an explosion.
Yash Vasant Joshi
Thesis: Torrefaction of herbaceous biomass – A study of product, process and technology
Phd Supervisor: Dr. B.J. Boersma (Mechanical, Maritime and Materials Engineering, Process and En-ergy Department)
Defence date: November 19, 2015
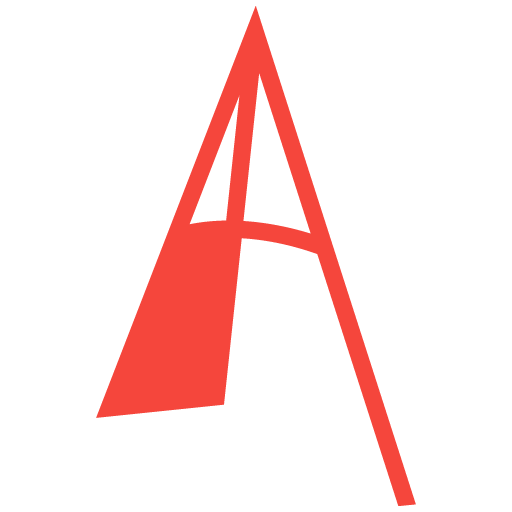
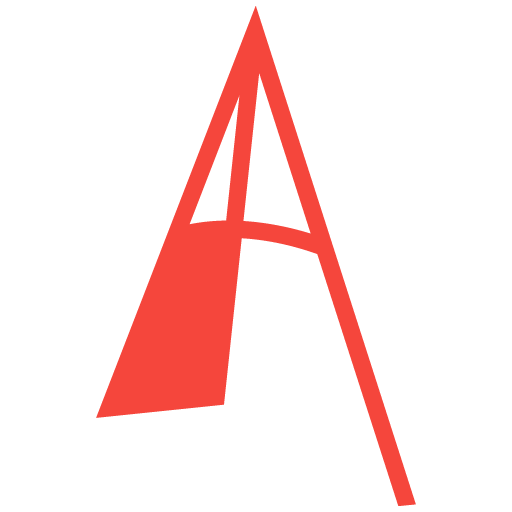
Comments are closed.