Of het nu om cake, vuistdik pantserstaal of een vliegtuigpaneel gaat, een waterstraal snijdt er moeiteloos doorheen. Door de wispelturigheid van de waterjet bestaat er nog koudwatervrees bij de industrie.
Onterecht, meent dr.ir. André Hoogstrate, die een praktisch model voor deze scheidingsmethode uitwerkte.
De laserstraal is het toonbeeld van hightech snijgereedschap. Bij het grote publiek is de intense lichtbundel vooral bekend uit films waarin excentrieke snoodaards James Bond in tweeën willen zagen. In de bewerkingingsindustrie is lasersnijden echter bijna usance, vertelt dr.ir. André Hoogstrate.
,,De laser is zo ingeburgerd dat er tot op de cent mee geconcurreerd moet worden. Het is een mooie techniek, waarmee je afhankelijk van het materiaal een snijsnelheid tot ruim vijftien meter per minuut kunt halen.” In combinatie met een computergestuurde snijtafel kunnen zeer complexe werkstukken worden vervaardigd. Toch kent ook de laser zijn beperkingen, zegt Hoogstrate, die maandag promoveerde bij de afdeling productietechniek en organisatie van Werktuigbouwkunde.
,,Omdat het te snijden materiaal tot smelttemperatuur wordt verhit, verandert de microstructuur rond de snede. Hierdoor wijzigt ook de hardheid van het materiaal en dat is niet altijd acceptabel.”
Aan lasersnijden kleven wel meer nadelen. Door de enorme hitte verdampt er altijd wat materiaal en ontstaan soms giftige gassen. En materialen die het vertikken te smelten, zoals keramiek, vallen met een laser nauwelijks fatsoenlijk te klieven.
Nu wil het geval dat met water, zo ongeveer de tegenpool van de loeihete laserstraal, snijden ook prima gaat. Vallende waterdruppels kunnen een rots tenslotte volledig uithollen, al duurt dat wel heel lang. Maar dat kan sneller. Aan het begin van de twintigste eeuw gebruikten Russische mijnwerkers al hogedruk waterstraalapparatuur voor steenkoolwinning. En eind jaren zestig ontdekte de Amerikaanse onderzoeker Robert Franz dat een dunne waterstraal zelfs door allerlei materialen kan snijden, mits de snelheid van de straal hoog genoeg is. Een beetje industriële waterjet schiet tegenwoordig met 700 meter per seconde uit zijn snijkop, ruim twee keer de geluidssnelheid.
Hoogstrate: ,,Waterstraalsnijden is nu redelijk ingevoerd, vooral voor het snijden van zaken als taart en schuim. In de jaren tachtig werd ontdekt dat je met een waterjet ook metalen en andere harde materialen kunt snijden, door deeltjes als granaatzand in de straal te injecteren. De waterstraal fungeert dan als drager voor de deeltjes, die het eigenlijke snijwerk doen. Het gemak waarmee je dan door allerlei soorten materialen kunt snijden, is bijna onvoorstelbaar.”
Rariteit
Dat maakt waterstraalsnijden tot één van de meest flexibele scheidingstechnologieën. Boterzachte cake, panelen met kevlar-wapening of zelfs explosieve stoffen vormen geen beletsel voor het naalddunne straaltje. Hoewel er vierduizend bar druk achter de straal zit, voert het water namelijk ook veel warmte af. Daardoor wordt het snijmateriaal nauwelijks heter dan zestig graden Celsius. Maar terwijl puur waterstraalsnijden al vrij gebruikelijk is, wil de abrasieve variant met toegevoegd poeder maar niet doorbreken.
,,Tot voor kort was abrasief stralen een rariteit. Op beurzen vond men zo’n apparaat machtig interessant, maar serieuze industriële toepassingen waren er nauwelijks. De methode bleek namelijk erg onvoorspelbaar. De ene dag haalde je een snijsnelheid van 100 millimeter per seconde, de andere dag veel minder”, aldus Hoogstrate. ,,Ook de beheersing van de poedertoevoer en de druk levert veel problemen op, en zo is er een groot aantal zaken waarmee je rekening moet houden. En als je een ander materiaal wilt snijden, moet je al die procesparameters weer opnieuw instellen.”
Een kwestie van trial-and-error kortom, en dat maakt het abrasieve waterjet niet erg aantrekkelijk voor de industrie. Daar moest dus nodig wat aan gebeuren vond Hoogstrate. Hij besloot een praktisch model op te stellen, waarmee voor elk materiaal snel de benodigde instellingen zijn te vinden.
In feite staat het model geheel in dienst van de industriële werkvoorbereiding, geeft de onderzoeker toe.
,,Dat was mijn bedoeling ook, want ik wil hiermee de toepassing van deze technologie stimuleren. Daarom gaat het model ook uit van makkelijk meetbare parameters, zoals de snijenergie, de intensiteit van de waterstraal, de diepte van de snede, of de gewenste optische kwaliteit van het snijvlak.”
Een van de problemen waar hij tegenaan liep, was het bepalen van de snijenergie van de waterbundel. ,,Je kunt er natuurlijk geen drukmeter onder zetten, want daar snijdt-ie meteen doorheen. Uiteindelijk ontdekte ik dat de smeltenergie die je nodig zou hebben om het materiaal van de snede weg te branden, erg goed overeenkomt met de benodigde snijenergie van de straal. Raar eigenlijk, je zou eerder een verband verwachten met een mechanische materiaaleigenschap zoals de elasticiteitsmodulus.”
Dat is een fysische puzzel waar Hoogstrate niet helemaal uit is gekomen. ,,Maar ach”, relativeert hij, ,,Als je echt gedetailleerd naar de interactie van de poederdeeltjes en het snijmateriaal gaat kijken, snap je soms überhaupt niet dat het werkt. Het voordeel van praktijkgericht onderzoek is dat je dan even naar je machine kunt lopen om je ervan te vergewissen dat-ie wel degelijk snijdt.”
Pantserplaat
Verder was zijn onderzoek redelijk hands on. Hoogstrate reviseerde de snijtafel van zijn waterstraalmachine, ontwierp een nieuwe spuitkop, en liet een ton fijn granaatzand aanrukken om exotische materialen als Arall, Glare en pantserplaat aan stukken te snijden.
,,Je moet ongeveer driehonderd gram poeder per minuut aan de waterstraal toevoegen. Dat lijkt misschien veel, maar de straal bevat maar één procent poedermateriaal.”
Het verbruikte poeder wordt meestal niet teruggewonnen, weet hij. ,,Dat kost energie omdat er veel vocht inzit. Bovendien verandert de grootte en kwaliteit van de poederdeeltjes tijdens het snijproces. In de spuitkop worden korreltjes over een afstand vanvijftig millimeter enorm versneld, van stilstand tot ruim driehonderd meter per seconde. En door onderlinge botsingen worden de korreltjes dan tot een factor drie kleiner. Je kunt het poeder dus niet al te vaak hergebruiken.”
Nu hij dit onderzoek heeft afgerond, wil hij verder met nieuwe toepassingen en hogere drukken. ,,Tot achtduizend bar”, geeft hij aan. ,,Dat zijn we nu aan het uitwerken, en als we dat eenmaal voor elkaar hebben kunnen we misschien laminaten als Hylite snijden zonder poeder toe te voegen. Verder willen we een soortgelijke straaltechniek inzetten voor microbewerkingen, bijvoorbeeld bij zonnecelfabricage. Het etsproces daarvan gebeurt nu chemisch, maar met een soort egale poederdouche zou je hetzelfde moeten kunnen bereiken.”
Zijn opstelling in de Centrale werkplaats is nu weg. Maar binnen en buiten TU-kringen kreeg men al snel lucht van de speciale eigenschappen van Hoogstrate’s snijmachine. In de avonduren heeft hij naast zijn onderzoek dan ook flink wat specialistisch snijwerk verricht voor onder meer materiaalkundigen en onderzoekers van Lucht- en Ruimtevaarttechniek. ,,Sommige materialen zijn haast niet op andere manier te bewerken. Als je dicht, vezelversterkt materiaal onder een zaag- of freesmachine legt trek je de vezels eruit en gaat het delamineren. Dat vind ik nog wel het leukste van dit onderzoek. Het is misschien niet wereldschokkend, maar voor een kleine groep mensen heeft het toch veel betekend. Dat is toch mooi?”
Of het nu om cake, vuistdik pantserstaal of een vliegtuigpaneel gaat, een waterstraal snijdt er moeiteloos doorheen. Door de wispelturigheid van de waterjet bestaat er nog koudwatervrees bij de industrie. Onterecht, meent dr.ir. André Hoogstrate, die een praktisch model voor deze scheidingsmethode uitwerkte.
De laserstraal is het toonbeeld van hightech snijgereedschap. Bij het grote publiek is de intense lichtbundel vooral bekend uit films waarin excentrieke snoodaards James Bond in tweeën willen zagen. In de bewerkingingsindustrie is lasersnijden echter bijna usance, vertelt dr.ir. André Hoogstrate.
,,De laser is zo ingeburgerd dat er tot op de cent mee geconcurreerd moet worden. Het is een mooie techniek, waarmee je afhankelijk van het materiaal een snijsnelheid tot ruim vijftien meter per minuut kunt halen.” In combinatie met een computergestuurde snijtafel kunnen zeer complexe werkstukken worden vervaardigd. Toch kent ook de laser zijn beperkingen, zegt Hoogstrate, die maandag promoveerde bij de afdeling productietechniek en organisatie van Werktuigbouwkunde.
,,Omdat het te snijden materiaal tot smelttemperatuur wordt verhit, verandert de microstructuur rond de snede. Hierdoor wijzigt ook de hardheid van het materiaal en dat is niet altijd acceptabel.”
Aan lasersnijden kleven wel meer nadelen. Door de enorme hitte verdampt er altijd wat materiaal en ontstaan soms giftige gassen. En materialen die het vertikken te smelten, zoals keramiek, vallen met een laser nauwelijks fatsoenlijk te klieven.
Nu wil het geval dat met water, zo ongeveer de tegenpool van de loeihete laserstraal, snijden ook prima gaat. Vallende waterdruppels kunnen een rots tenslotte volledig uithollen, al duurt dat wel heel lang. Maar dat kan sneller. Aan het begin van de twintigste eeuw gebruikten Russische mijnwerkers al hogedruk waterstraalapparatuur voor steenkoolwinning. En eind jaren zestig ontdekte de Amerikaanse onderzoeker Robert Franz dat een dunne waterstraal zelfs door allerlei materialen kan snijden, mits de snelheid van de straal hoog genoeg is. Een beetje industriële waterjet schiet tegenwoordig met 700 meter per seconde uit zijn snijkop, ruim twee keer de geluidssnelheid.
Hoogstrate: ,,Waterstraalsnijden is nu redelijk ingevoerd, vooral voor het snijden van zaken als taart en schuim. In de jaren tachtig werd ontdekt dat je met een waterjet ook metalen en andere harde materialen kunt snijden, door deeltjes als granaatzand in de straal te injecteren. De waterstraal fungeert dan als drager voor de deeltjes, die het eigenlijke snijwerk doen. Het gemak waarmee je dan door allerlei soorten materialen kunt snijden, is bijna onvoorstelbaar.”
Rariteit
Dat maakt waterstraalsnijden tot één van de meest flexibele scheidingstechnologieën. Boterzachte cake, panelen met kevlar-wapening of zelfs explosieve stoffen vormen geen beletsel voor het naalddunne straaltje. Hoewel er vierduizend bar druk achter de straal zit, voert het water namelijk ook veel warmte af. Daardoor wordt het snijmateriaal nauwelijks heter dan zestig graden Celsius. Maar terwijl puur waterstraalsnijden al vrij gebruikelijk is, wil de abrasieve variant met toegevoegd poeder maar niet doorbreken.
,,Tot voor kort was abrasief stralen een rariteit. Op beurzen vond men zo’n apparaat machtig interessant, maar serieuze industriële toepassingen waren er nauwelijks. De methode bleek namelijk erg onvoorspelbaar. De ene dag haalde je een snijsnelheid van 100 millimeter per seconde, de andere dag veel minder”, aldus Hoogstrate. ,,Ook de beheersing van de poedertoevoer en de druk levert veel problemen op, en zo is er een groot aantal zaken waarmee je rekening moet houden. En als je een ander materiaal wilt snijden, moet je al die procesparameters weer opnieuw instellen.”
Een kwestie van trial-and-error kortom, en dat maakt het abrasieve waterjet niet erg aantrekkelijk voor de industrie. Daar moest dus nodig wat aan gebeuren vond Hoogstrate. Hij besloot een praktisch model op te stellen, waarmee voor elk materiaal snel de benodigde instellingen zijn te vinden.
In feite staat het model geheel in dienst van de industriële werkvoorbereiding, geeft de onderzoeker toe.
,,Dat was mijn bedoeling ook, want ik wil hiermee de toepassing van deze technologie stimuleren. Daarom gaat het model ook uit van makkelijk meetbare parameters, zoals de snijenergie, de intensiteit van de waterstraal, de diepte van de snede, of de gewenste optische kwaliteit van het snijvlak.”
Een van de problemen waar hij tegenaan liep, was het bepalen van de snijenergie van de waterbundel. ,,Je kunt er natuurlijk geen drukmeter onder zetten, want daar snijdt-ie meteen doorheen. Uiteindelijk ontdekte ik dat de smeltenergie die je nodig zou hebben om het materiaal van de snede weg te branden, erg goed overeenkomt met de benodigde snijenergie van de straal. Raar eigenlijk, je zou eerder een verband verwachten met een mechanische materiaaleigenschap zoals de elasticiteitsmodulus.”
Dat is een fysische puzzel waar Hoogstrate niet helemaal uit is gekomen. ,,Maar ach”, relativeert hij, ,,Als je echt gedetailleerd naar de interactie van de poederdeeltjes en het snijmateriaal gaat kijken, snap je soms überhaupt niet dat het werkt. Het voordeel van praktijkgericht onderzoek is dat je dan even naar je machine kunt lopen om je ervan te vergewissen dat-ie wel degelijk snijdt.”
Pantserplaat
Verder was zijn onderzoek redelijk hands on. Hoogstrate reviseerde de snijtafel van zijn waterstraalmachine, ontwierp een nieuwe spuitkop, en liet een ton fijn granaatzand aanrukken om exotische materialen als Arall, Glare en pantserplaat aan stukken te snijden.
,,Je moet ongeveer driehonderd gram poeder per minuut aan de waterstraal toevoegen. Dat lijkt misschien veel, maar de straal bevat maar één procent poedermateriaal.”
Het verbruikte poeder wordt meestal niet teruggewonnen, weet hij. ,,Dat kost energie omdat er veel vocht inzit. Bovendien verandert de grootte en kwaliteit van de poederdeeltjes tijdens het snijproces. In de spuitkop worden korreltjes over een afstand vanvijftig millimeter enorm versneld, van stilstand tot ruim driehonderd meter per seconde. En door onderlinge botsingen worden de korreltjes dan tot een factor drie kleiner. Je kunt het poeder dus niet al te vaak hergebruiken.”
Nu hij dit onderzoek heeft afgerond, wil hij verder met nieuwe toepassingen en hogere drukken. ,,Tot achtduizend bar”, geeft hij aan. ,,Dat zijn we nu aan het uitwerken, en als we dat eenmaal voor elkaar hebben kunnen we misschien laminaten als Hylite snijden zonder poeder toe te voegen. Verder willen we een soortgelijke straaltechniek inzetten voor microbewerkingen, bijvoorbeeld bij zonnecelfabricage. Het etsproces daarvan gebeurt nu chemisch, maar met een soort egale poederdouche zou je hetzelfde moeten kunnen bereiken.”
Zijn opstelling in de Centrale werkplaats is nu weg. Maar binnen en buiten TU-kringen kreeg men al snel lucht van de speciale eigenschappen van Hoogstrate’s snijmachine. In de avonduren heeft hij naast zijn onderzoek dan ook flink wat specialistisch snijwerk verricht voor onder meer materiaalkundigen en onderzoekers van Lucht- en Ruimtevaarttechniek. ,,Sommige materialen zijn haast niet op andere manier te bewerken. Als je dicht, vezelversterkt materiaal onder een zaag- of freesmachine legt trek je de vezels eruit en gaat het delamineren. Dat vind ik nog wel het leukste van dit onderzoek. Het is misschien niet wereldschokkend, maar voor een kleine groep mensen heeft het toch veel betekend. Dat is toch mooi?”
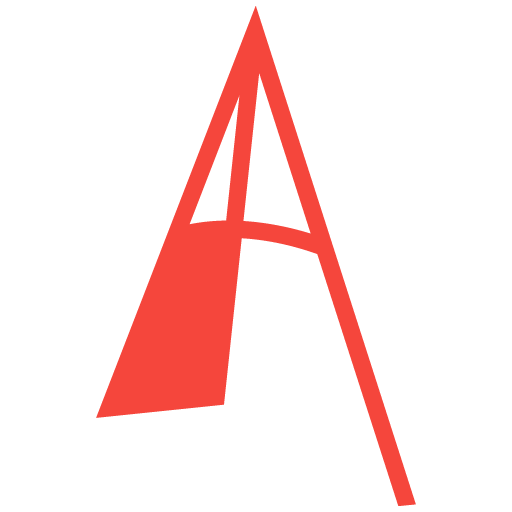
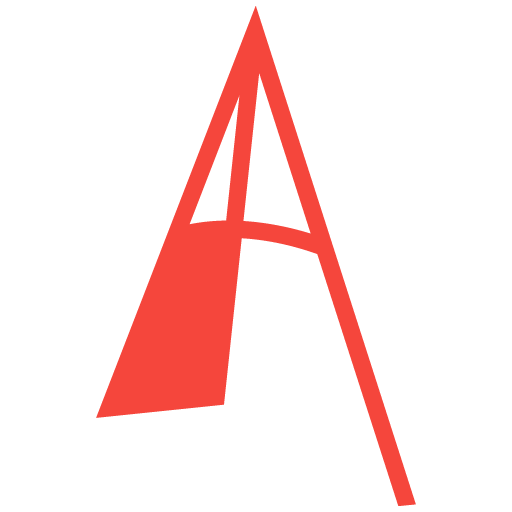
Comments are closed.