The hexapod is a unique testing facility for the dynamic testing of structures. Professor Mirek Kaminski, who invented the machine four years ago, proudly demonstrated the 60 ton monster to the press.
Dressed in his suit, he bends over and picks up a welded piece of steel piping to make his point. The heavy piece has been tested on the hexapod. “The machine not only pulls the pipe, but rotates it as well. Either simultaneously or out-of-phase. Combinations of loads occur in practice and may cause damage through unexpected material fatigue,” he explains. The hexapod can simulate the whole range of pulling, pushing, and rotating loads in any direction with forces of up to 100 tonnes.
“This machine can simulate the effect of 20 years of shipping on welded construction parts within four weeks,” Kaminski adds. As a professor in maritime and offshore constructions at the 3mE Faculty, shipping is the first application that springs to mind. Later, he adds numerous other applications such as the unexpected micro cracks in the Merwede bridge; broken chassis or axes in trucks; and even simulating the effects of earthquakes on constructions.
The five million euro hexapod is a unique machine in terms of the combination of the pure force it applies (up to 100 tons) with a sub-millimetre displacement precision. The precision is important for the accuracy of the scientific datasets.
Failures of constructions, explains Kaminski, are indicative of shortcomings of our construction models. Dynamic testing should help to improve these models with the ultimate goal of making constructions safer and less dependent on inspection and maintenance.
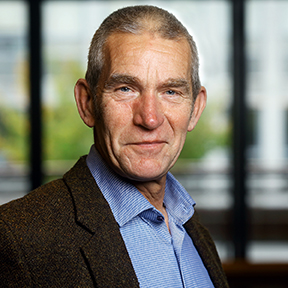
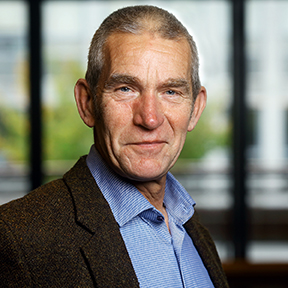
Heb je een vraag of opmerking over dit artikel?
j.w.wassink@tudelft.nl
Comments are closed.