TU Delft students are braving the cold today in a bunker near Rijswijk to test the latest version of their Nimbus rocket engine. It’s the power house of the Stratos III rocket that will be launched in July and that will help the students retake the height record, they hope.
Filipe Barreiro in the Dream hall. (Photo: Nora de Vries)
“It’s a big bunker,” says Filipe Barreiro, chief propulsion engineer with project Stratos. “But there is no heating, and the days are long.” A larger rocket means a longer time to fill the oxidiser tanks and a longer time to heat them to build up pressure. The current rocket engine, Nimbus, is about twice as big as its predecessor, Stratos II+, that was launched in 2015. After a burn time of twenty seconds, the Stratos II+ broke the height record, reaching 21.5 kilometres. This record was later broken by students from Stuttgart University. The Delft Aerospace Rocket Engineering (DARE) team is confident that its current DHX-400 Nimbus engine will fire the Stratos III to a new record. Simulations predict a height of between 60 and 80 kilometres.
Burning time is essential for reaching high altitudes. From the launch, the engine accelerates the rocket into the sky. The longer the engine burns, the faster the rocket goes. After the engine has burnt out, the rocket rises against gravity through the very thin atmosphere to the apex of its trajectory.
Last week’s successful test registered thirty-eight seconds of burn time. This time, the students have filled the oxidiser tank with an extra fourteen kilograms of nitrous oxide (N2O), which should allow another two seconds of ‘liquid burn time’.
The team will also try and reduce the rocket’s weight
Barreiro explains: “We burn a certain part of liquid nitrous and then it becomes gas. The liquid burn time gives much higher thrust, so we want to increase the liquid burn time. We still have some place in the tanks. I’m interested to see how the engine will hold up. Two extra seconds of liquid burn time is quite a bit. It should help us a lot with altitude. Two seconds high up in the atmosphere with much less drag and little weight left helps a lot. Every little bit helps.”
In principle, the anatomy of the rocket is simple: a pressurised tank of oxidiser on top of a hollow fuel cylinder of about two metres long. The fuel is a mix of sorbitol (diet sugar), paraffin and aluminium powder. Below the fuel ‘grains’ there is a disk with three holes that mixes the gases, followed by the nozzle where the exhaust gases are accelerated.
The current team has improved the pre-chamber between the oxidiser tank and the fuel grains. The pre-chamber now effectively pre-heats the oxidiser before it flows through the fuel. Issues with cracking fuel grains and a cracked nozzle have been solved so that Barreiro thinks the engine now runs reliably.
The launch-site in Spain has been reserved for some time this summer. In the meantime, the team will try and reduce the rocket’s weight. One of the options is to replace the 5 mm thick aluminium housing by a carbon composite tube. Another possibility is making a 3D printed nozzle from titanium instead of the current full-carbon version.
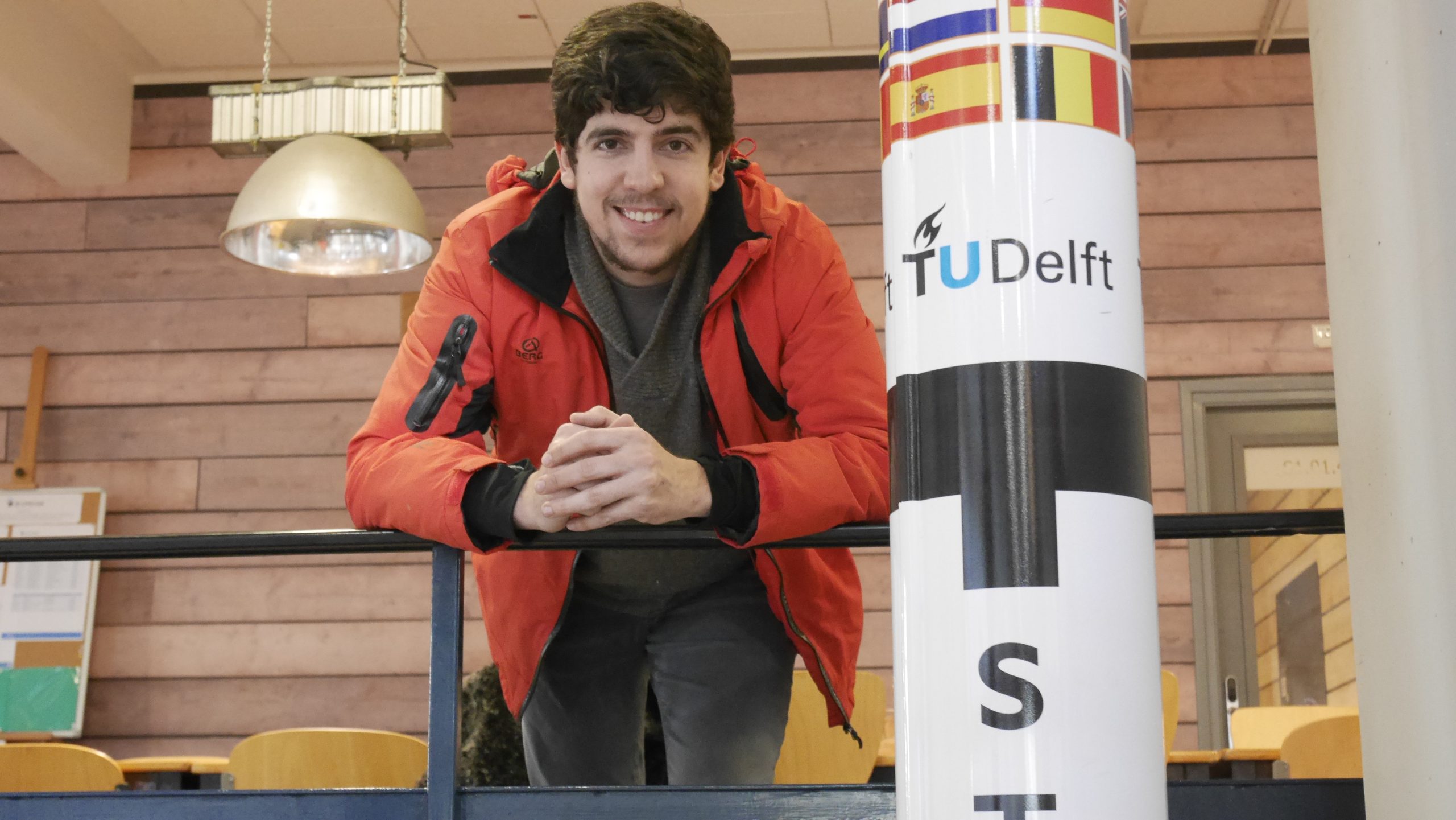
“If we get both working, we’re looking at fifteen kilograms weight reduction. That helps a lot,” says chief propulsion engineer Barreiro.
- 01 March 2018: EPILOGUE – Wednesday 28 February, the DARE team experienced too many delays in setting up the test launch, says Commissioner of External Relations, Weronika Dziarnowska. Eventually, the test was canceled and a new date will be set.
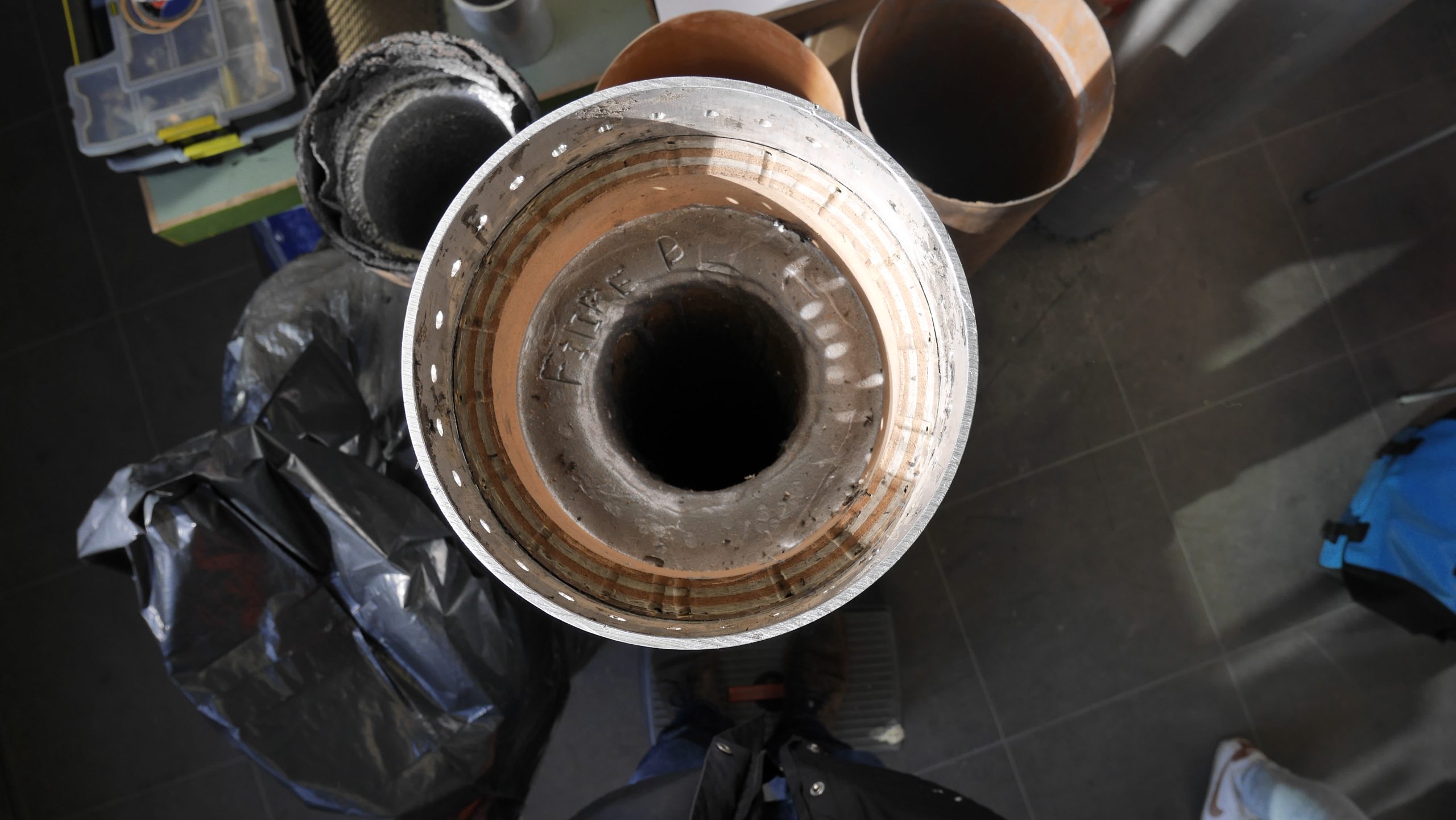
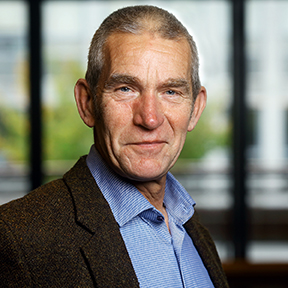
Heb je een vraag of opmerking over dit artikel?
j.w.wassink@tudelft.nl
Comments are closed.