Next generation offshore windturbines will have their vulnerable gearboxes replaced by hydraulic pumps. Power generation will be centralized for a number of turbines. Dr. Niels Diepeveen explored the future of offshore windparks.
According to Professor Gijs van Kuik it is time to reconsider the concept for offshore wind turbines which has proven to be successful onshore. As wind turbines keep getting bigger (5 megawatt and beyond), the weight on top of the tower becomes too large and the gearbox that transfers the energy from the rotor into a lower torque and higher speed rotation for the benefit of the generator, will increasingly prove to be the weakest link.
Besides, exchanging the heavy metal bulk in the top of the mast at open sea is frankly a nightmare. The Delft Offshore Turbine (DOT) is a new concept, originating from Dr. Jan van der Tempel (director at Ampelmann), for offshore turbines that avoids these problems. The DOT proposes to get rid of the gearbox altogether and to transfer the power down the mast by means of hydraulics.
DOT envisions a hydraulic pump directly driven by the rotor’s shaft in the top of the mast (in the nacelle). High pressure oil transports the energy down the mast to a hydraulic motor coupled to a (sea) water pump in the base. A water line then transports the energy over a longer distance (up to kilometres) to a central power generator.
In his PhD-research Dr. Niels Diepeveen (Civil Engineering and Geo-sciences) has tested the feasibility of the DOT concept by literature study, simulations and scaled-down test setups.
Diepeveen studied the dynamic response of the hydraulic system in detail. If the system is too stiff, sudden gusts in the wind may lead to ‘hammer effects’ in the flow. If it’s too sluggish, large overshoots in pressure may occur. However, relatively simple precautions as putting an accumulator or a pressure control valve in the high-pressure line will soften the edges of the hydraulic response.
Experiments with a 1-megawatt oil-hydraulic transmission unit showed that variations in the torque (in both high and low frequencies) were quickly damped, leading to as smoothened electrical output. It confirmed the theoretical findings that a fluid power transmission line can be configured in such a way that no active form of control is required.
Subsequent tests with a wind turbine model in the wind tunnel showed that the passive hydraulic power transmission behaved just as well as expected.
Diepeveen calculated that the overall efficiency from rotor to hydro turbine (three conversion steps) is around 80 percent.
He concludes that when indeed hydraulic pumps of multi megawatt dimensions become commercially obtainable in a few years, as is expected, the DOT concept for offshore windparks will become technically feasible and indeed preferable to the current set-up in which each turbine has its own generator and gearbox. The design will be significantly less complex, says Diepeveen.
In the meantime, he proposes to build a 1-megawatt hydraulic drive train prototype as a proof-of-principle and a test bench for the DOT-concept, since the step from laboratory experiments to a 5 MW real turbine is too large.
Niels Diepeveen, ‘On fluid power transmission in offshore wind turbines’, 29 August 2013, PhD supervisor Professor Gijs van Kuik (AE).
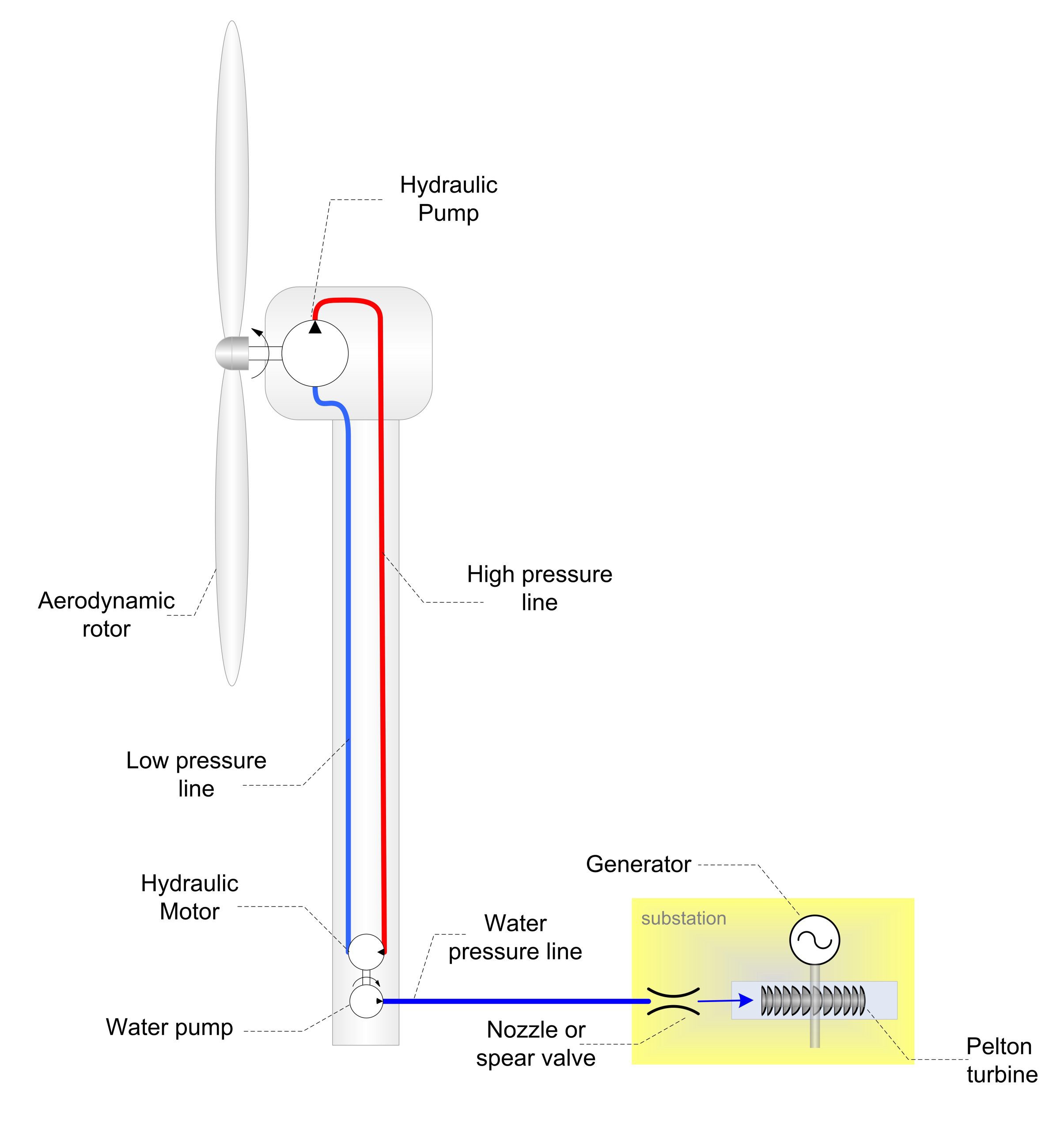
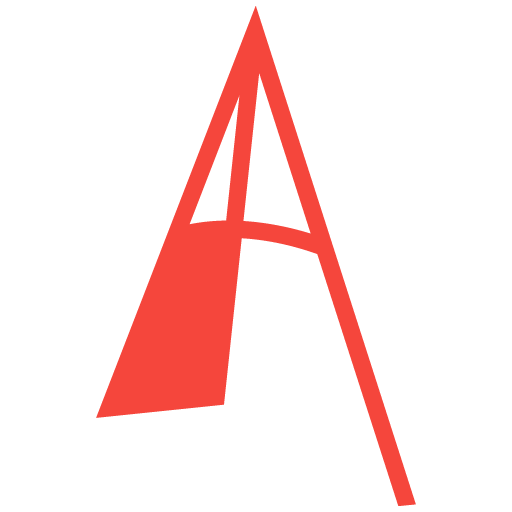
Comments are closed.