Industrial design student Bob van Putten makes biomaterials out of algae. He dreams of a world in which product packaging will be completely biodegradable.
The lawn is freshly mown and all kinds of flowering plants neatly arranged. At the edge of the garden is a clear stream, where ducks and swans and little well-kept boats float. This idyllic back garden will become a rubbish dump if Bob van Putten has his way.
That is to say: a dump site for the biomaterials that students at the department of design for sustainability (faculty of Industrial Design) are currently developing. Van Putten makes bio-based material from the algae growing abundantly in the water next to his parent’s back garden. He hopes to make packaging material out of it, among other uses.
If his plan works out, throwing candy wrappers in the garden every now and then will no longer be a crime, but rather a good thing to do for Mother Nature, since the completely biodegradable plastics will add nutrients to the soil. This is also in line with the cradle to cradle philosophy (an extreme approach to recycling in which materials are viewed as nutrients circulating in the environment).
For his ingenuity, Van Putten was recently awarded a ‘Young Wild Idea’ grant, worth ten thousand euro, to be used to help him further develop the material and products.
“If you press hard enough on the algae, the plants will form a kind of felt,” Van Putten explains, while holding a bunch of the plants on a stick he has just dipped in the water. “The strains are held together by a group of compounds called exopolysaccharides. These chemicals protect the cells against pathogens and serve as natural binding agents. This stuff is often what makes algae slimy to touch.”
Press even harder, like two hundred kilo Newton, and the sheet becomes wafer-thin, smooth and shiny, like plastic. Van Putten is now ameliorating this material by adding different kinds of additives that will bind the fibres together even stronger, much like resins in carbon fibre. As far as he knows, nobody has tried this before. He plans to patent his technique.
The next step is to figure out what products to make out of this biomaterial. “It has to be suitable for mass production,” says Van de Putten. “One difficulty lies in the fact that you can’t deform the material once it’s made. Thus, as you make the biomaterial, you have to make sure it’s immediately given the right shape. You therefore have to press the algae and resins in a mall that withstands two hundred kilo Newton per square meter and has openings that allow the water to escape.”
Van Putten has not yet figured out what kind of products he will start producing: “Perhaps picnic sets, or trays used during festivals for glasses of beer. Things that people throw away easily and that irritate me.”
But as environmentally friendly as his eventual products may seem, in order to be truly cradle to cradle they must be more than just biodegradable alone. “If lots of packaging was to be made out of this material, your garden would soon become too small,” says Renee Wever, one of Van Putten’s supervisors. “And throwing the material out on the streets would make a mess. One of the things you also have to think of then, is in what waste circuit the products and wrappings will end up.”
Failing to do so as a green innovator can land you in serious trouble, Wever says: “Take for instance the bottles of the company Innocent, which made their smoothie bottles biodegradable. But the trouble was that some people still threw them in the bins for plastic bottles, which caused problems for the plastic recyclers processing the plastic. Innocent had to stop making biodegradable bottles. The same could happen with the algal material if, for example, too much of it ends up in the recycle paper bins.”
Van Putten is aware of this. “But”, he says, “I think in the long run countries will develop new methods for collecting biodegradable products, making it easier for people to throw them away without causing harm to other recycling circuits.”
Het Delftse racing team DUT-09 presenteerde woensdagavond zijn nieuwe ontwerp. In vergelijking met de winnende auto van afgelopen jaar wordt de racer iets groter en toch lichter, aldus teammanager Stef de Jong. Nieuwe voorschriften vereisen een binnenruimte die gelijk is aan Formule 1-wagens. Voor het Delftse team, dat de kleinste en lichtste wagens maakt in de Formula Student Racing Competitie, betekende dat vooral een hogere beenruimte. De neus werd verhoogd en de wielophanging naar beneden verplaatst.
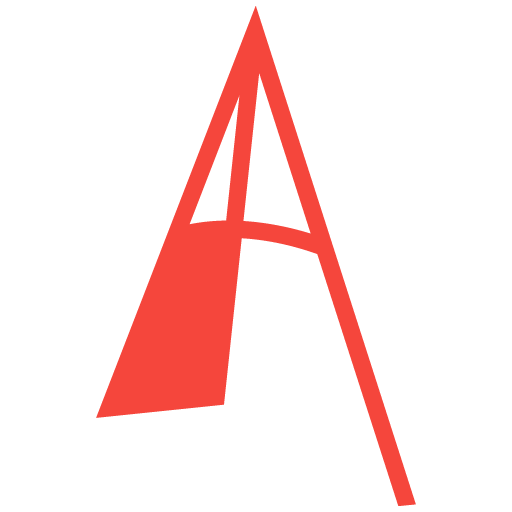
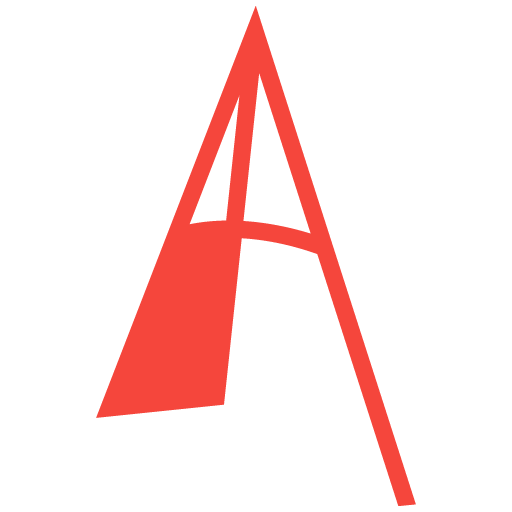
Comments are closed.