A rubbish heap is more than just a collection of junk; it is also a goldmine. This is because many valuable raw materials can be found amongst the paper napkins, broken plates and broken telephones. TU Delft is developing devices to remove these raw materials from the mountain of waste.
Fifteen large bags full of rubble have just been delivered to TU Delft’s recycling lab. Peter Rem, Professor of Resources and Recycling sifts through the ground concrete in the bags. He takes a handful and lets the pieces fall back into the bag, as if they’re jingling gold coins from a hoard of treasure. “This isn’t just waste; it’s also a treasure trove,” he says, enthusiastically.
Not many people have this association with junk. It stinks, is in the way and therefore seems a nuisance more than anything. We produce huge amounts of waste every day, all over the world, both privately in our homes and in industry. So much so that it is a millstone around our neck, because what do we do with it?
From a financial perspective it also represents a considerable burden. “In the Netherlands, we spend seventeen billion euros a year on materials, to make cars, build houses and manufacture cups and other products. We then spend another ten billion euros to dispose of that waste in a tidy way,” explains Rem.
So, above all, waste is perceived as something negative. The recycling lab wants to change that, by showing that the rubbish heap can also be a source of raw materials. For example, it is very useful to be able to reclaim raw materials that are becoming increasingly scarce, and to reuse waste such as plastic and concrete as much as possible. “Many European research groups are involved in waste control. We are one of the few groups to develop devices with which valuable materials can be reused. Instead of extracting copper from a mine, we reclaim it from waste. This is both profitable and good for the environment.”
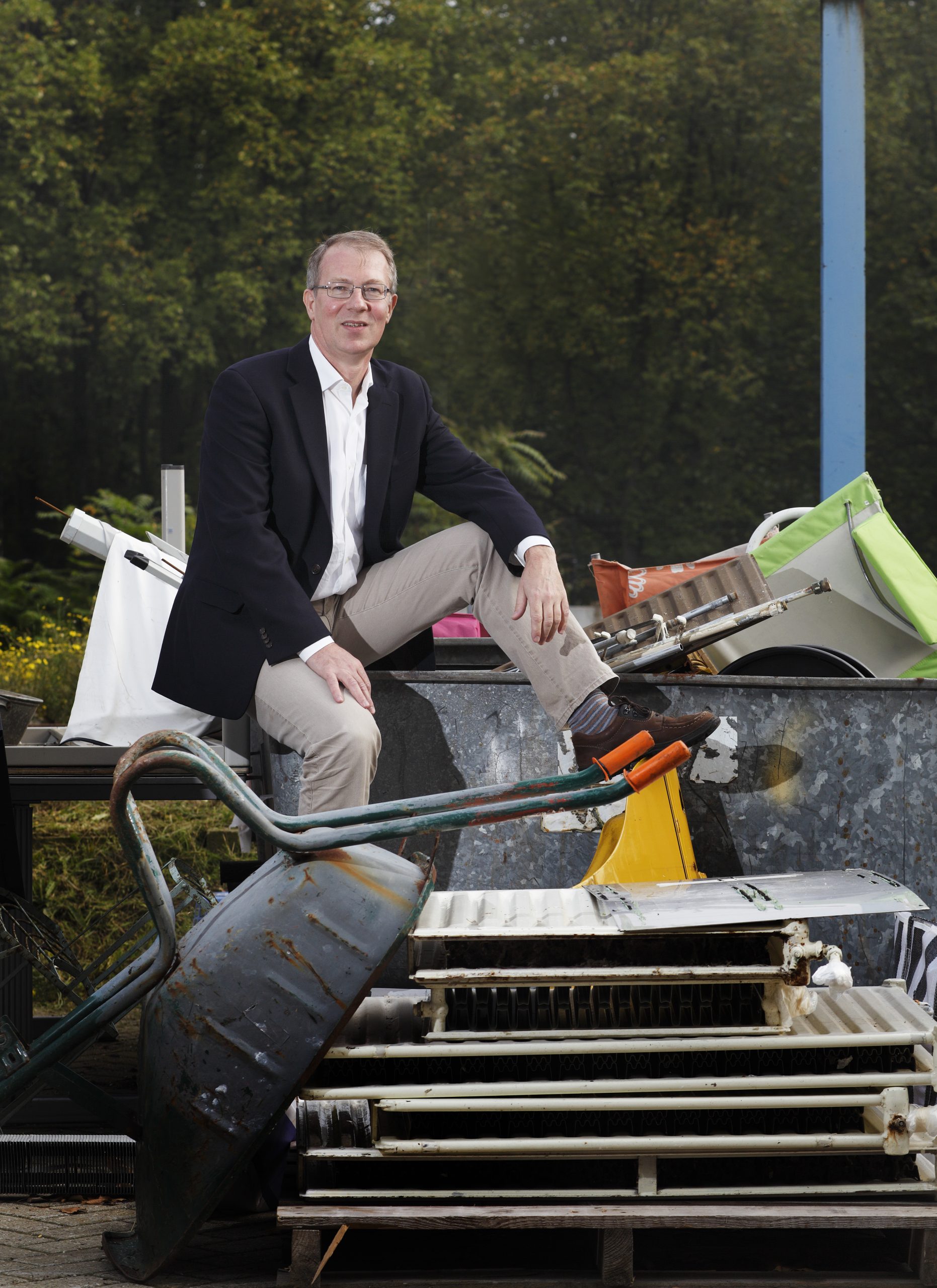
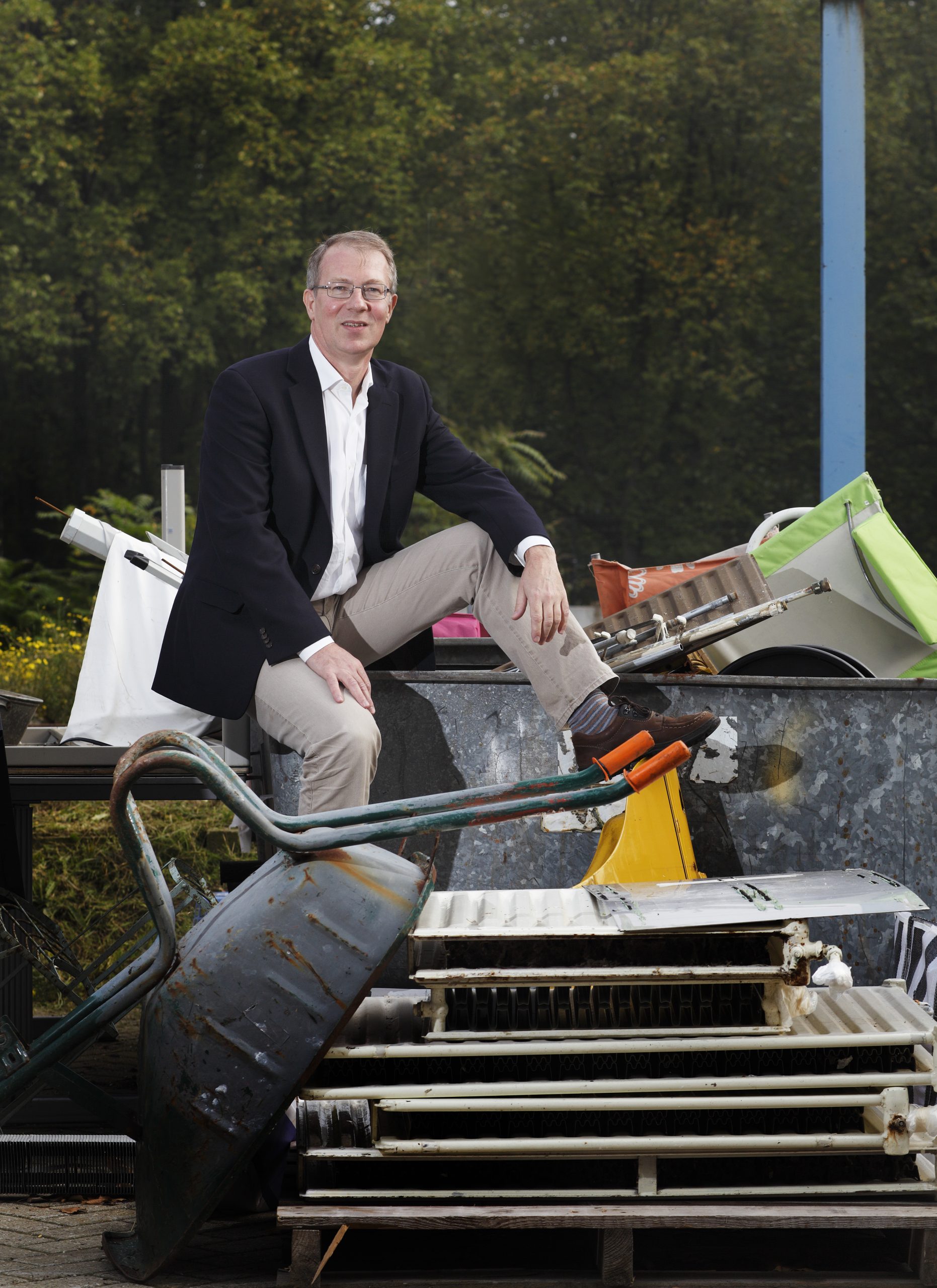
Surprising reuse
The pulverised concrete that Rem let run through his fingers like gold coins comes from a demolished building, and he has ambitious plans for it. But many companies are sceptical about reused concrete. How can you ever make broken concrete strong enough to build bridges or buildings with it? Won’t a car just fall right through it? “Nonsense,” says Rem confidently. Indeed, research by TU Delft and the University of Wroclaw in Poland recently concluded that reused concrete is even stronger than newly produced concrete. “That was a real stroke of luck, as nobody had really anticipated such positive results. We are now trying to find out why this is the case.”
Rem has a theory. “Concrete is often made from river gravel or broken stone. It’s nothing special, and above all cheap. This is bonded together with cement and then used. We receive it after a crusher has compressed it into small pieces and removed the reinforcing bars from it. We use a drum to grind down the stones that remain. The blocks grind over each other and rattle the cement off. Large and small pieces are removed and a specially developed technique is used to separate the cement and fine sand from the moist mixture. We then rebond the modified surface area, and this is probably where the surprise comes in. After rebonding, within the space of a week, the material is thirty percent stronger than ordinary concrete.”
It was already possible to demolish a concrete structure and construct a new building from the same material. “This has already been done in Groningen. Two government buildings were demolished, and the material was used to build an underground car park on the same site. I think we can do this even better now, thanks to our extra-strong reused concrete.”
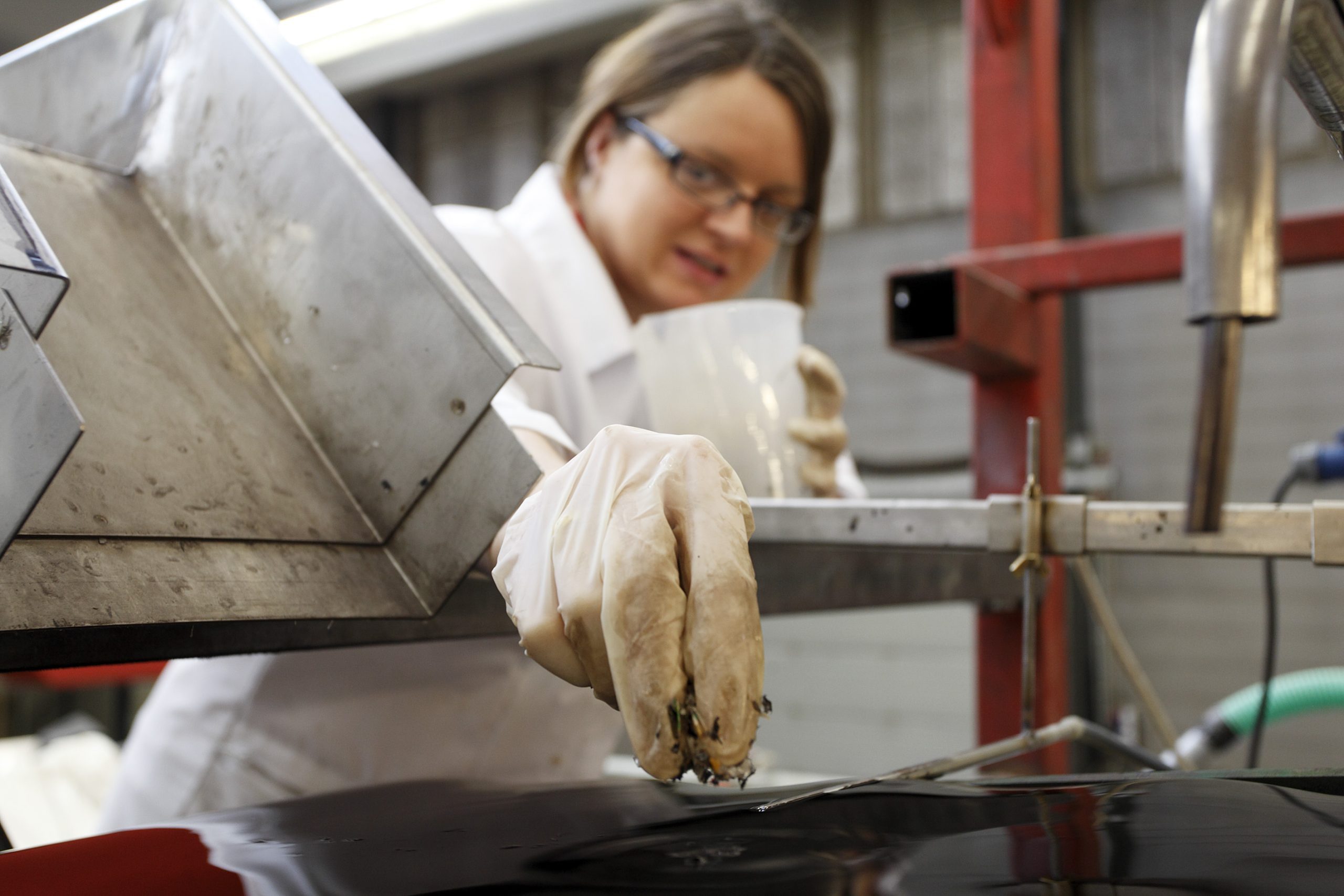
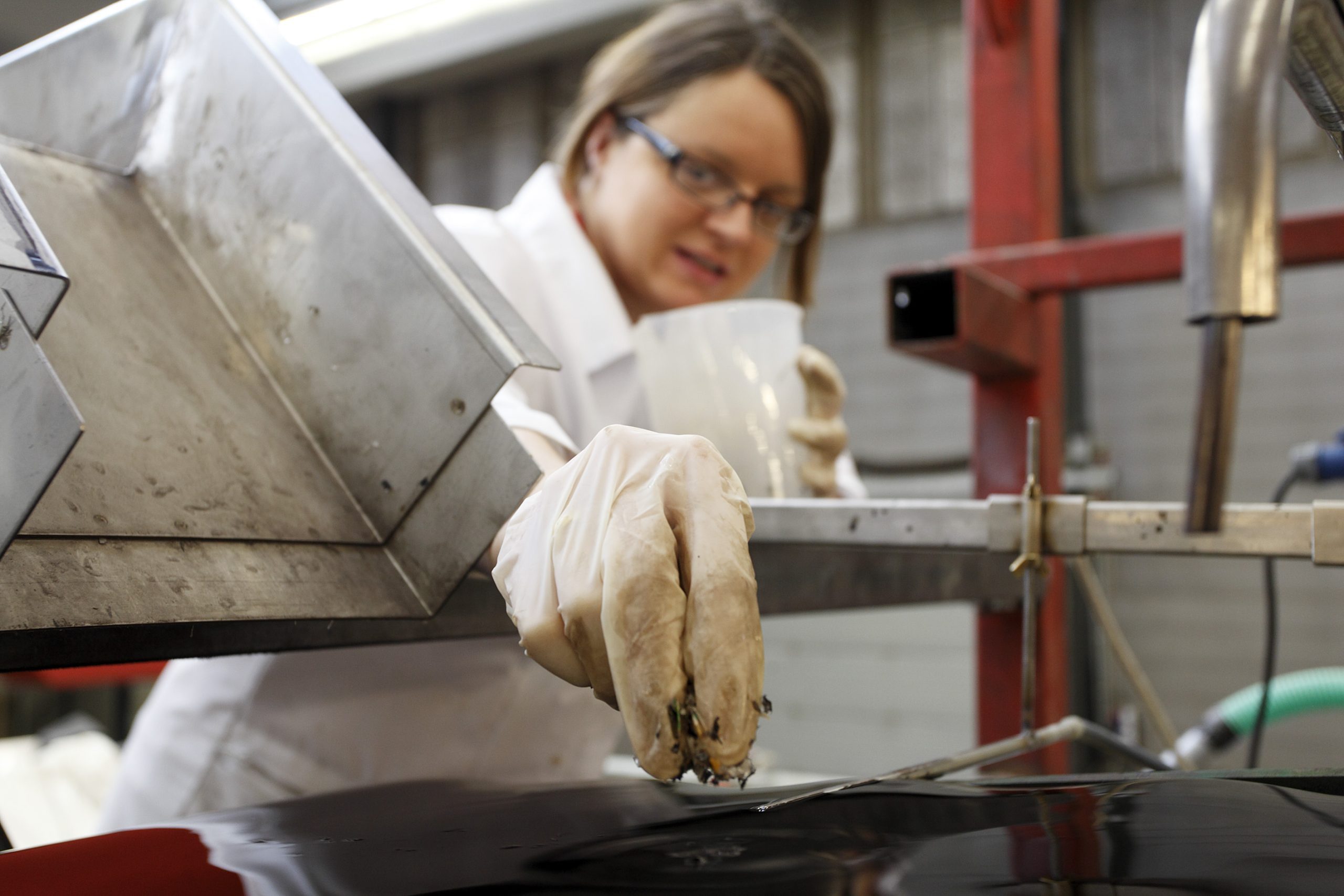
River of plastic
As well as concrete, plastic is also ideal for reuse, stresses Rem. Of course, this has been done for some time and all sorts of things are made from recycled plastic, from soft drink bottles to children’s toys. But the separation of plastic from other waste is still a fairly difficult, time-consuming and therefore expensive process. The recycling lab is developing methods to improve this, such as a special technique that uses a magnetic liquid. In the lab Rem holds up a bottle containing a dark liquid. “There are four little balls in here, but you can’t see them now.” He places the bottle on a magnet and the four coloured balls start moving, ending up at different levels. “We use the same principle to separate plastic.”
Not all plastics are alike. Rem points to the desk in his office. “There’s a plastic box containing teabags. That box is different from the stirrers, packaging or bottles. Therefore, we are developing a method that enables us to separate different types of plastic from one another.”
Standard technology based on infrared has already been developed in Germany. This can be used to separate polypropylene from polyethylene on a conveyor belt. The same types of plastic are sorted together. “We are developing a complementary technology. We process the objects to make flakes, a bit like confetti. We wash them and then separate them into different types.”
This is done using a liquid that contains magnetic iron ore. It is the same substance used to make ink for printers. “This liquid does not have a single density, but varies from high to low when we place it over a magnet. This is useful, because different types of plastic also have different densities. Therefore, we make a large channel through which a river of plastic flows. The liquid causes the plastics to position itself at four or five different levels. The mixture gradually flows through the channel at a rate of thirty centimetres per second. At the back, the different types of plastic are simply suctioned away, separating them into the different types.”
This method has recently been used to build an industrial separator by a company in Winterswijk. Rem wants to develop the technology further. “We use a hundred million euros worth of plastic in Europe each year. I hope that we will be able to produce around three billion euros per year using our method within the next ten years. This may not sound very ambitious, but compared to the two billion euros worth of reused plastic currently used throughout the whole of Europe, this would be a real breakthrough. However, it will take some time before that happens. The waste-processing industry is fairly conservative.”
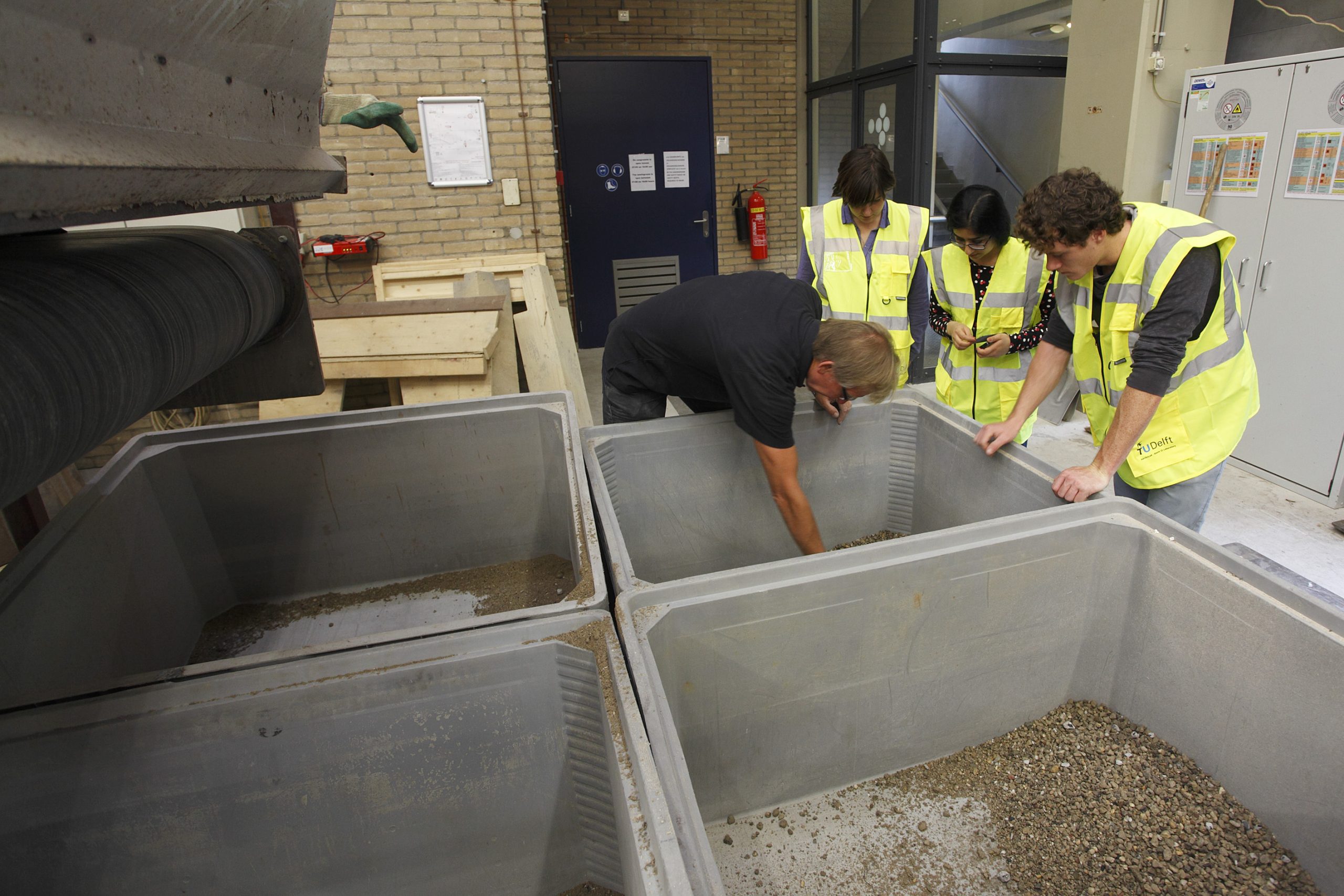
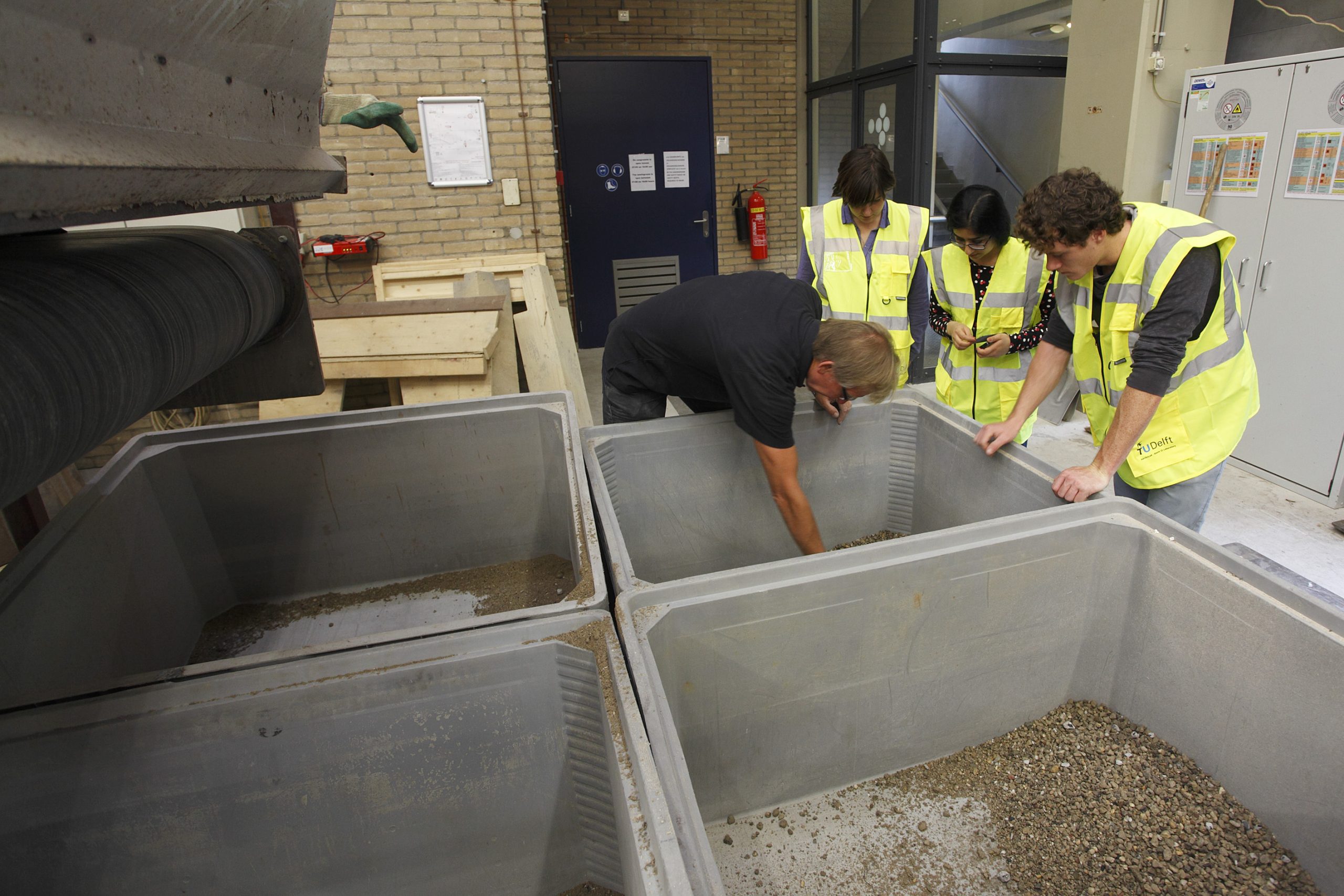
Increased cooperation
We can actually reuse anything, says Rem. “It is simply a matter of organisation. In recycling, the entire chain is fragmented. The government makes the rules, the logistics industry is responsible for the collection and other parties clean and reuse the items. This is all very complex and sometimes rather inconvenient. For the companies that wish to reuse materials, it would be nice to be able to collect separated waste, so that they receive the correct materials in the cleanest state possible. But that’s not up to them.”
We need more cooperation, so that everyone knows what wishes and possibilities exist, according to Rem. “Packaging manufacturers and product designers also need to be involved in this. If a designer uses coloured polymers, the material becomes incredibly difficult to reuse. A label on transparent material is much better for recycling purposes. But, unfortunately, companies are often unaware of this.”
Recycling is not just good for the environment. According to European Commissioner for the Environment Janez Potočnikit can also provide a significant boost to the economy and employment. “I agree with him. Reuse is prime example of innovation and is good for the Netherlands and for Europe as a whole; however, it also pushes out existing activities, which is a sensitive issue. Just consider importers of oil, for example. Oil is an important raw material in plastics. The importers have no interest in recycling and are lobbying against it. That’s a shame. The Netherlands is currently a moderate player in terms of reuse. Germany is far more innovative. It has a long-term vision, which provides a sense of security, and a less fanatic oil lobby. Efficient recycling requires an extensive and centralised approach, so that processes can be standardised and made affordable. But the politicians want municipal authorities to organise waste processing themselves. That’s something I find alarming. Small municipalities can’t do that.”
Strategic value
Everything that is developed must be as cost-effictive as possible. “The benefits of our technology have to outweigh the costs. Everything is focused on providing instruments that are actually used. Otherwise they’re of no use to anyone. They also have to tie in well with existing waste processing practices. Nobody’s going to convert or rebuild a plant because a new recycling method is available.”
But it’s not all about money. Rem walks over to a large conveyor belt. “This is where we conduct research that can save lives. Waste processors and recyclers want to know the quality of their materials, which is why employees take samples. But that’s extremely dangerous and fatal accidents occur on a regular basis. It is not a suitable environment for people to walk around in, because of the conveyor belts, trucks and the large excavators driving around.”
Rem’s lab is developing a new method in collaboration with the University of Bologna. “We want to use a laser to determine the exact composition of the rubble. That’s difficult because the heavy and fine pieces are found on top while the light and coarse are on the bottom. An algorithm will be used to correct the distribution and indicate the right composition and particle size.”
Meanwhile, researchers in white coats are walking back and forth with broken items. More and more waste is being brought into the lab. Rem looks at it approvingly. For him this does not represent a contamination of his research environment, but rather more welcome ingredients to develop new technologies with, so that, over time, the rubbish dump can gradually turn into the treasure trove he already sees in it.
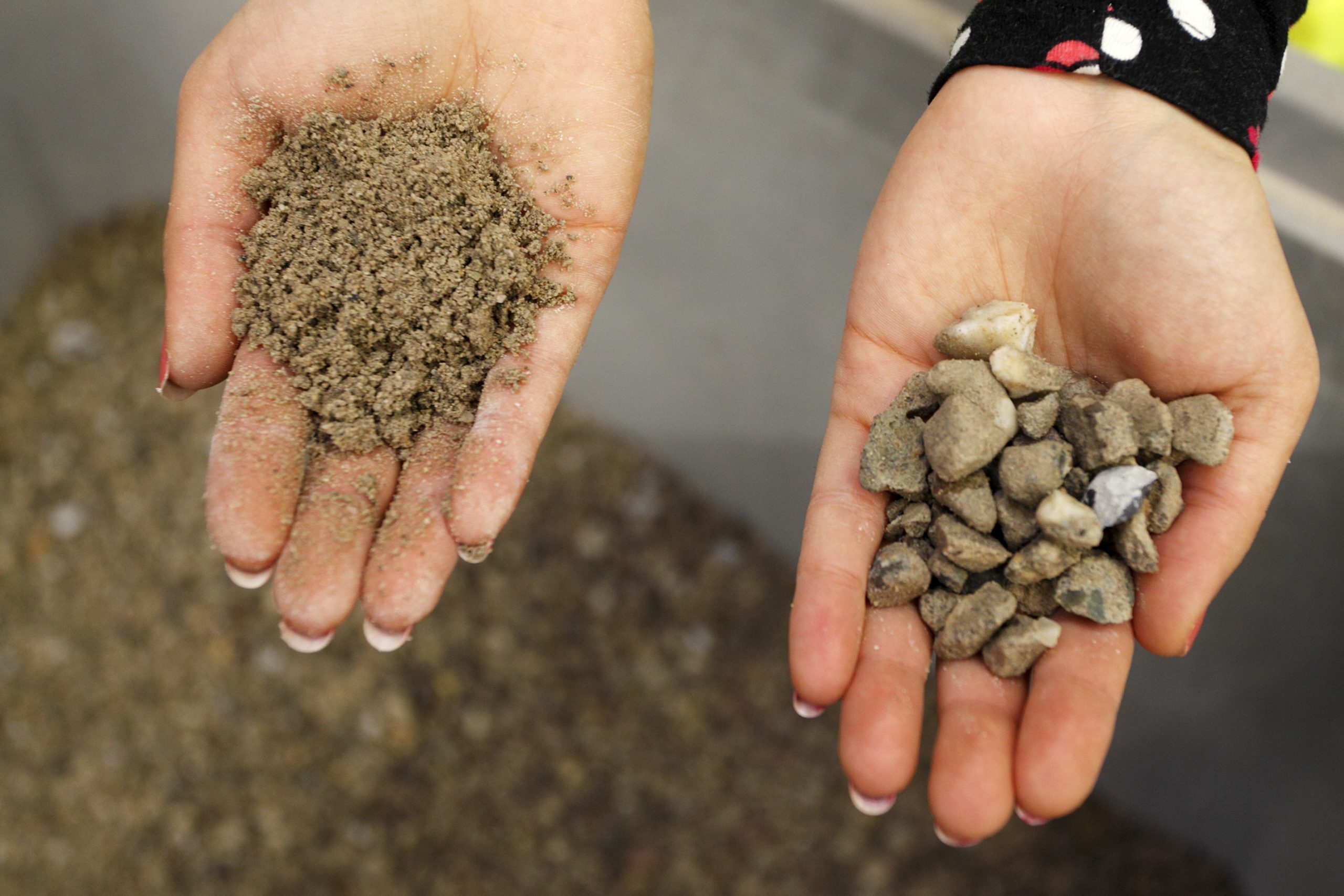
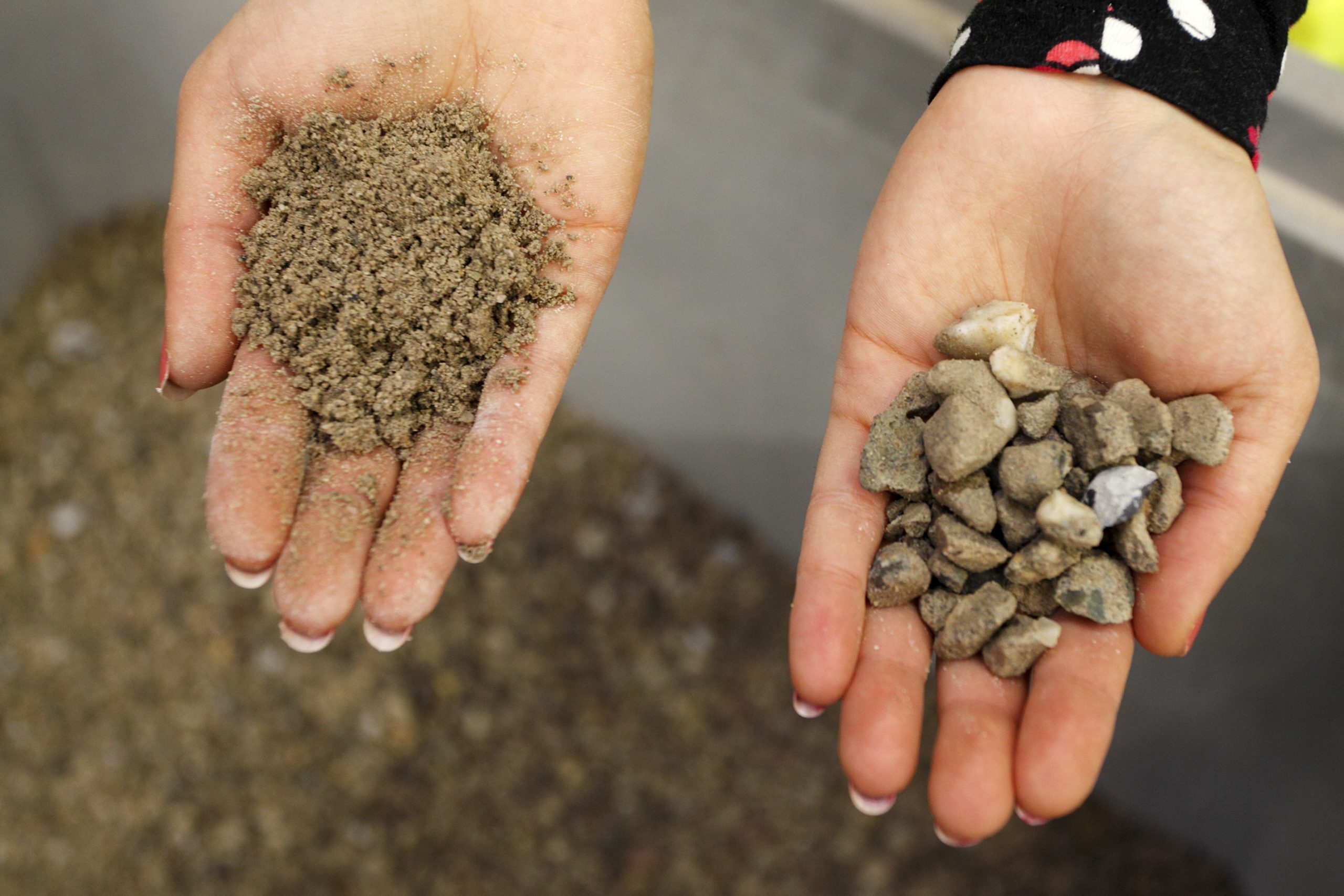
Smartphone pudding
The magnetic liquid is currently being used in tests to reclaim the scarce material indium. Indium is found in screens of mobile phones and tablet computers. “It is becoming increasingly scarce and therefore more and more expensive. We are investigating whether we can reclaim indium,” says post-doctoral researcher Dr Anna Grzech.
Grzech stands beside a set-up measuring 2.5 by 2 metres. She points towards a large container with small pieces of copper wire, plastic and glass. These used to be smartphones and LCD and plasma televisions. The parts are placed on a conveyor belt with a magnet underneath it. The liquid lies on top of the conveyor belt like a pudding. The belt advances at a rate of two centimetres per second.
“We use the magnetic liquid to separate the indium-containing glass from the rest. Glass has a different density to metals and plastic. Most metals are heavier and sink to the bottom, while glass floats. The conveyor belt is positioned at an angle so that the metals fall down while the glass moves up with the conveyor,” the Polish researcher explains. “This sounds simple, but it’s not. We want the cleanest glass possible and the densities are very similar.”
In this way the recycling lab is developing the separation method. Meanwhile, chemists in Sweden are working on the next step, trying to remove the indium from the glass. Grzech: “Our goal is to have a large plant in which you feed in an LCD television and get out indium. We hope to then be able to reclaim ninety percent of the glass from pieces measuring a hundred microns to four millimetres.” The project is scheduled to run until the end of 2016.
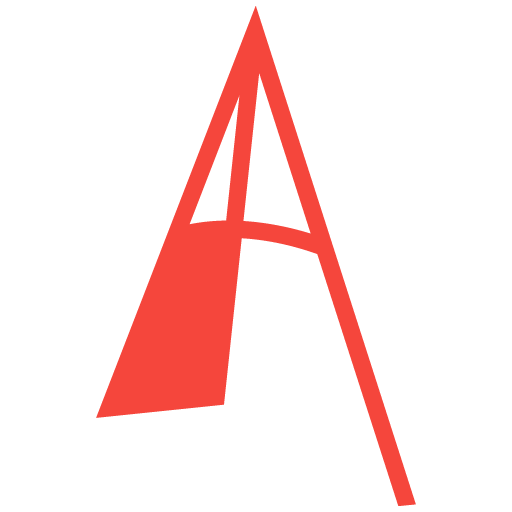
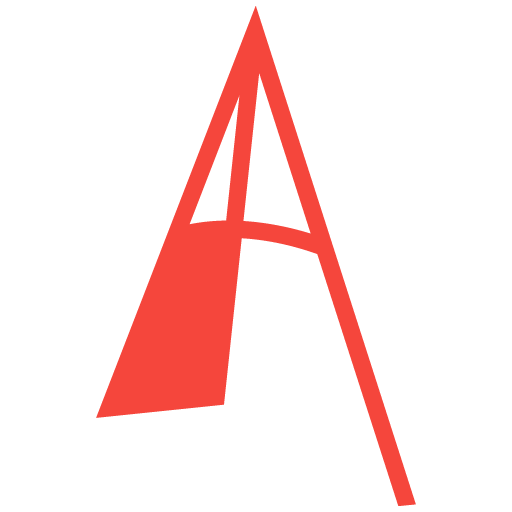
Comments are closed.