TU Delft mathematicians kicked off a €4.3 million, EU-funded research project earlier this month to help enhance the competitiveness of Europe’s heavy industry manufacturers.
As part of the EU’s Horizon 2020 research and innovation programme, the MOTOR Project aims to develop new types of numerical simulation and automatic shape optimization technologies for aircraft engines, ship propellers, water turbines and rotary screw compressors. Coordinated by TU Delft, the research will be conducted by an international consortium that will explore new mathematical concepts and advanced computational tools over the next three years. The idea is to harmonize the geometry and mathematical language used in computer-aided design and engineering systems, making it possible to virtually analyse machine designs in greater detail.
“In this project, we will create new software tools for optimizing the shapes of these so-called fluid energy machines to finally increase their overall efficiency,” said Matthias Möller, Assistant Professor of Numerical Analysis. “Mathematics is omnipresent in this project. It starts with the accurate algorithmic modelling of the rotor geometries, which are so-called functional free-form surfaces. Next, numerical simulation and optimization algorithms are entirely based on rigorous mathematical concepts like calculus of variation or iterative solution algorithms for systems of equations.”
Having worked in the field of isogeometric analysis for a number of years, Möller began to apply this computation approach to simulate the complex flow phenomena occurring in screw compressors. Together with two colleagues, Möller extended the analysis to fluid energy machines, eventually forming an international research consortium consisting of colleagues from academia and industry. By integrating computer-aided design, simulation-based analysis and automated shape optimization into real industrial design workflows, the new software tools should largely improve the speed and flexibility of developments cycles of fluid energy machines, thereby strengthening the competitiveness of Europe’s heavy industry manufacturing.
“In the first place, the industrial partners will benefit from the new simulation and automatic optimization technologies that they will integrate into their daily design workflows,” Möller explained. “The goal is to significantly reduce the time to production and to improve the efficiency of the resulting products. What is quite unique about the MOTOR project is that researchers and industrial partners from very different fields of applications are working together to solve common challenges. In that sense, we all benefit from synergy effects between different industry sectors.”
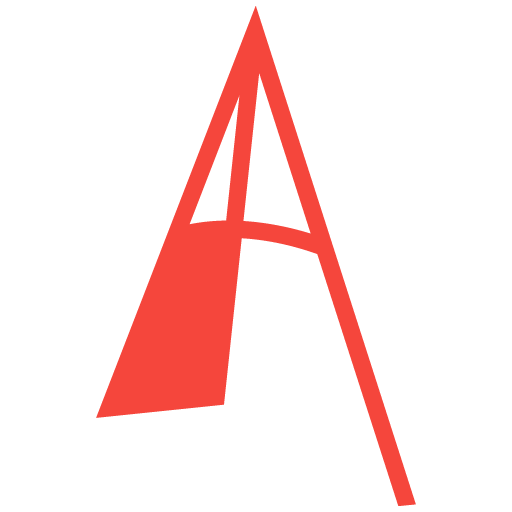
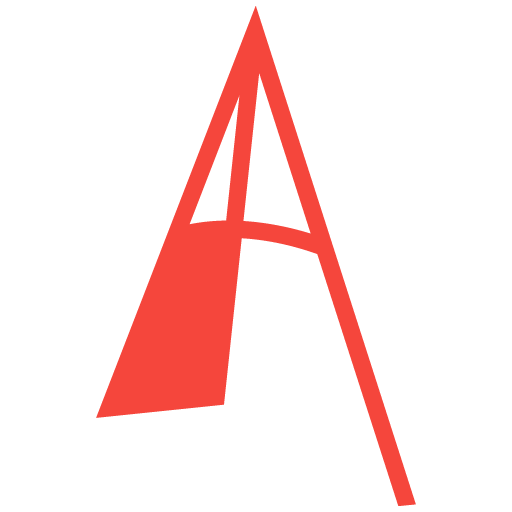
Comments are closed.