Wastewater from the Mars factory in Veghel, the largest chocolate producer in Europe, feeds bacteria in an STW-funded pilot plant, producing bioplastic.
To arrive at the Mars factory, you could navigate by smell. An air of caramelised sugar hangs over most of the place, except for the part where the pilot plant is housed: at the rear of the factory where a stream of cream-coloured wastewater flows into the sewer.
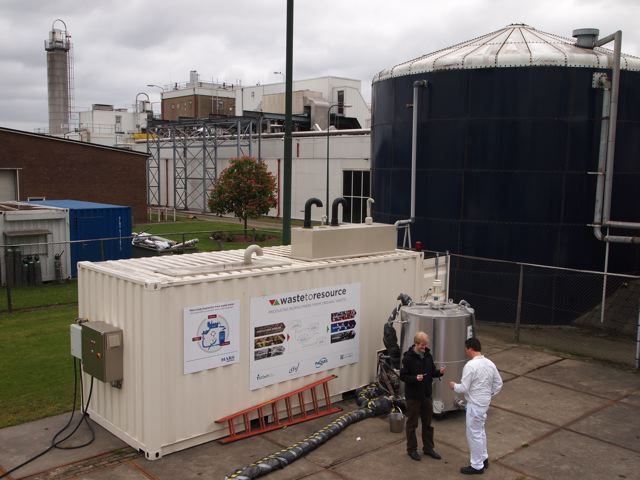
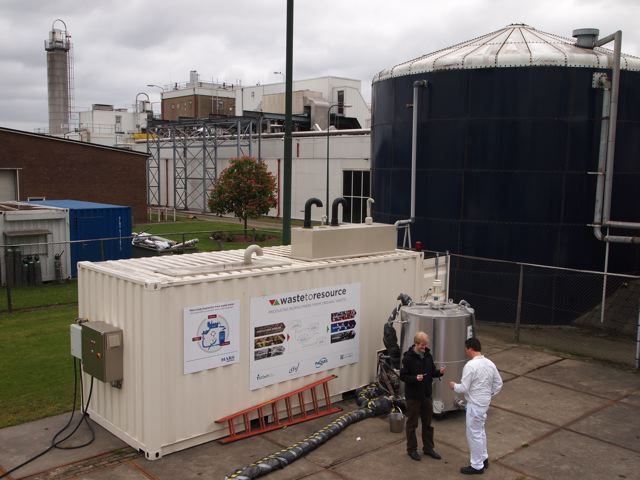
A tiny part (much less than a percent) of this stream containing sugars and fatty acids is drawn off toward a white container that houses the pilot plant. Operations here are run by Avans Academy student Casper Borsje and TU PhD-student Jelmer Tamis MSc. The process runs in three steps: fermentation, selection and accumulation.
In the first step, wastewater is fermented by microbes that convert all sugars in the solution into a mix of fatty acids like acetic acid, butyric acid and caproic acid. “It smells a bit like mussels today”, remarks Tamis.
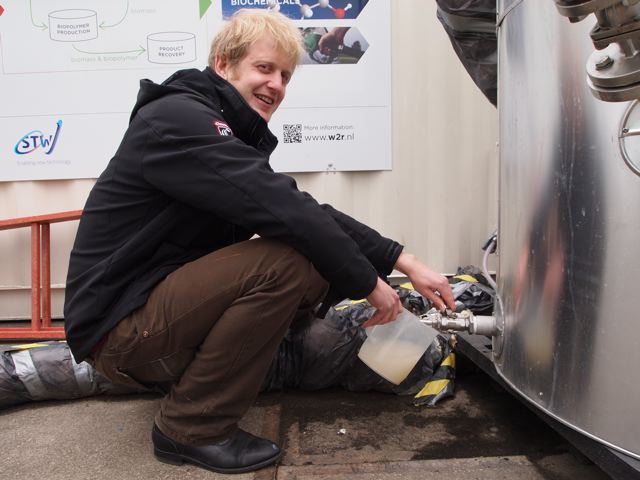
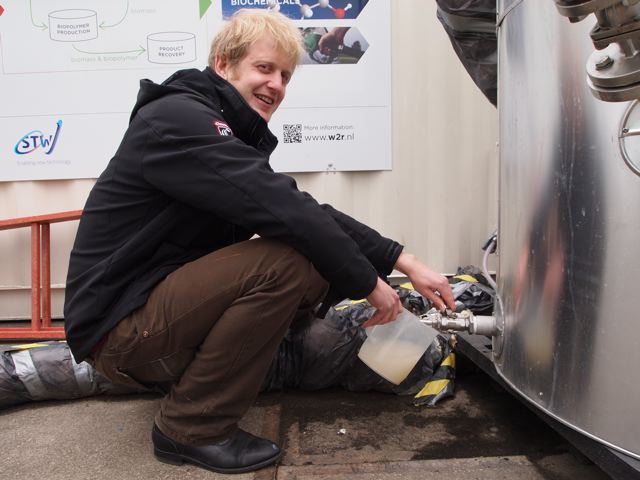
The fatty acid mix is kept in a steel vessel to be fed intermittently to the plastic-producing bacteria.
The set-up is based on earlier laboratory research by, amongst others, Dr. Katja Johnson, Leonie Marang MSc. and Dr. Yang Jiang, who did their PhD’s with Professor Mark van Loosdrecht (Faculty of Applied Sciences). They showed that if you apply a feast-famine regime to a mix of bacteria drawn from a wastewater treatment plant in Rotterdam, you end up with a population that quickly digests fatty acids into a sort of bacterial fat known as polyhydroxy alkanoate or PHA. This substance can be used as a bioplastic that is both biobased and biodegradable.
The natural selection of plastic-producing microbes takes place in the second step of the process by feeding the culture for an hour, followed by eleven hours of starvation. “It’s ecology applied in industry”, says Borsje. This survival of the fattest results in a microbial population that quickly converts fatty acids into PHA which is a microbial fat to bacteria but, because of its favourable properties is seen as a bioplastic by humans.
This population then goes on into the third phase in which they are fattened up into the extreme. In the lab, bacteria grew so obese that 80 to 90 percent of their dry body mass consisted of the PHA polymer. Such values have as yet not been attained in the pilot plant.
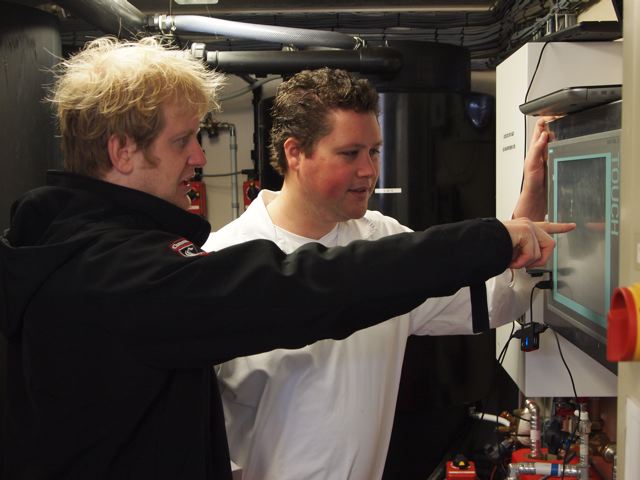
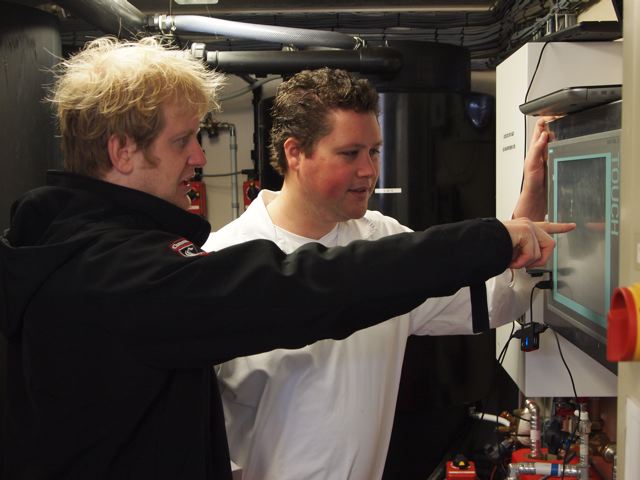
What makes selection harder in the pilot plant is the varying composition of the feeding wastewater. Moreover there are some compounds in the wastewater that make only a side population grow without PHA production. This parasite population limits the plastic content in the biomass to values below the laboratory standard. Currently Tamis contemplates the best ways for “bacterial genocide” to get rid of the side population.
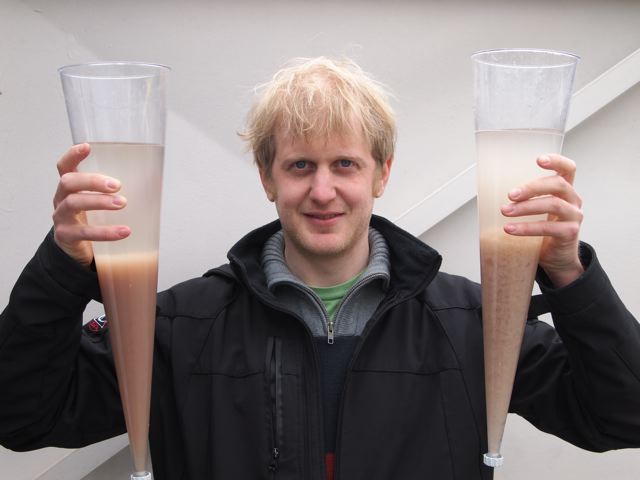
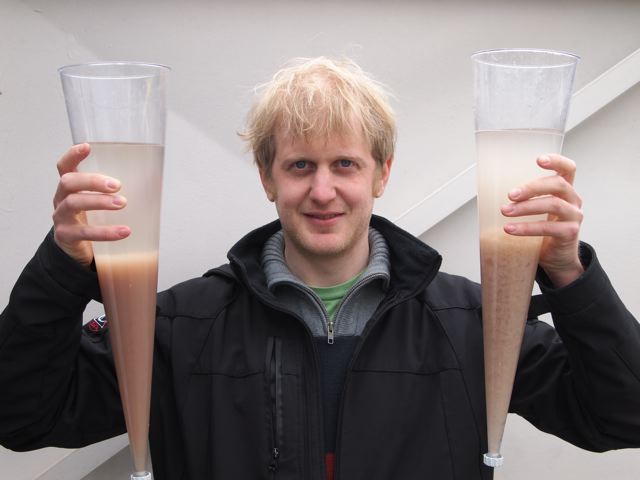
The pilot plant, which was built by Paques BV, has been operational since November 2012 and will probably be in use until the end of 2013. By that time, Tamis hopes to have increased the PHA content of the produced biomass. The production has to be optimised to bring down the production costs of currently about 8 euro/kilogram to 2 euro/kilogram. The candy factory Mars would like to use bioplastics for its wrappers, but will only do so if the cost is comparable to the fossil plastics it uses thus far. “In the end”, says Tamis, “it’s always economics that rules over sustainability.”
Hein Mous, environmental coordinator with Mars, does not agree. He refers to the ‘Sustainable within a Generation’ programme in which additional costs for products and processes are accepted if they contribute to an increase in sustainability.
More information on this and other waste to resource projects on w2r.nl
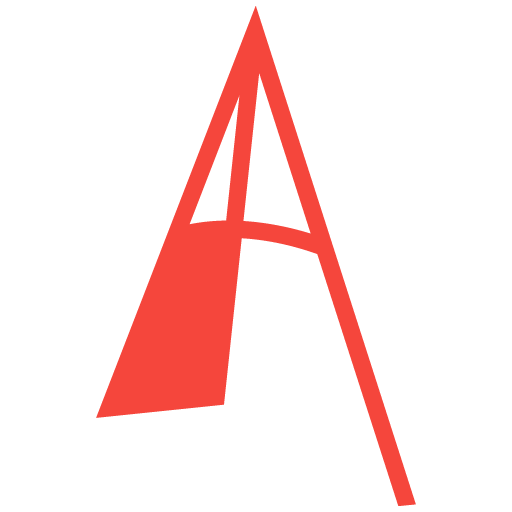
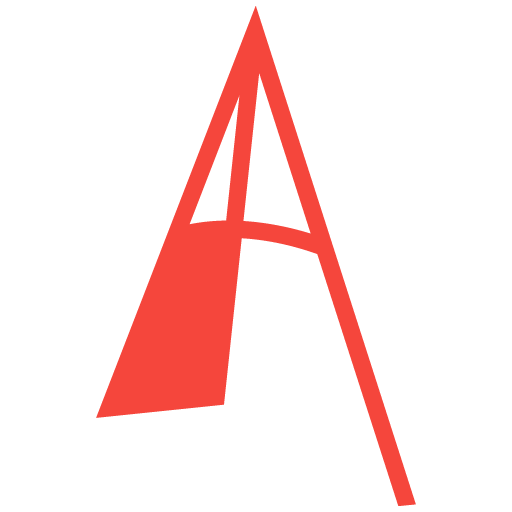
Comments are closed.