Harbours and mining companies can save huge amounts of energy if they would use a new kind of conveyor belt that is lighter and more flexible. Or so Professor Gabriel Lodewijks, who is developing this belt, believes.
Good news for the harbour of Rotterdam. If Professor Gabriel Lodewijks is right, if the harbour could make its conveyor belts function more energy efficiently with a new kind of rubber, it might be able to expand, an ambition which is now hindered by the goals the city of Rotterdam has set itself, as the city wants to have halved its carbon emissions by 2025. About 70 percent of the carbon emissions from the harbour can be attributed to the use of conveyor belts.
The professor of transport engineering and logistics (3mE faculty) has calculated that by processing aramid fibers – a class of strong, heat-resistant synthetic fibers used for ballistic body armor, for example – in rubber conveyer belts, the energy usage of these belts is reduced by 40 to 60 percent.
This however still needs to be proven with a test case. Prof. Lodewijks: “About a kilometre – 500 metres back and forth – of the belt will be installed in the harbour as a test case before the end of the year.”
By using aramid, the belt can be made lighter and more flexible, which reduces the rolling resistance.
An aramid called twaron was already being applied in conveyor belts as reinforcement since the 1990s. Prof. Lodewijks, in collaboration with a company called Teijing Aramid, added another type of aramid, called sulfron, to the rubber. “Recent technologies to glue the fibres together and form long chains, and new insights into the tensions in the joint, have made the production of this new type of belt possible,” the professor says.
Lodewijks studied the properties of the material and combined his findings with the outcome of a prior study of his on the energy consumption of a conveyor belt used in a mine in South Africa. This led to his conclusion that the new belt is 40 to 60 percent more energy efficient.
Manufacturing the belt is about 20 percent more costly than manufacturing a conventional belt. These costs however would be recovered in three months, thanks to the lower energy costs.
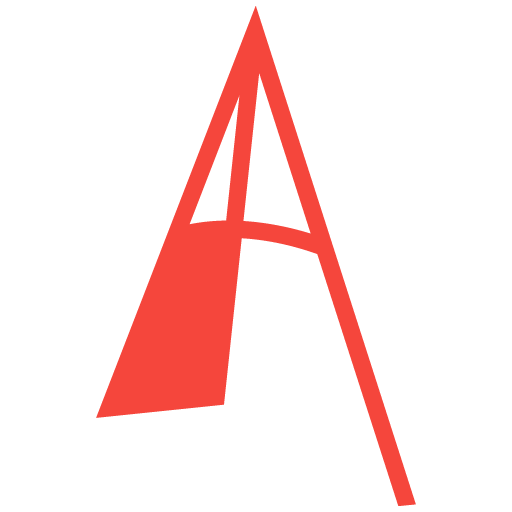
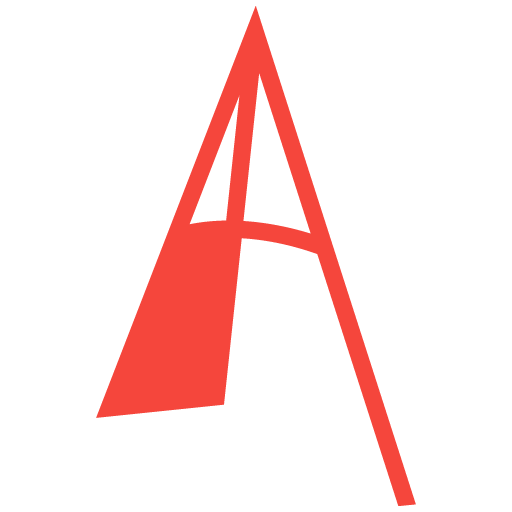
Comments are closed.