Predicting how deep a submarine can dive is like reading tea leaves. Or better, it was. John MacKay developed a new technique to predict when the vessel will collapse.
Everyone is holding their breath. Squeaky noises. The hull will collapse if the vessel dives much deeper. 7 mega Pascal, 8 mega Pascal… And then an ear deafening ‘Bang!’
“This is how my experiments went at first; the models were completely torn to pieces,” says John MacKay, who during his PhD research destroyed about 50 scaled submarines of about half a meter in length in a pressure chamber.
“The explosions were so violent that I couldn’t use the strain gages – or any other instrumentation attached to the model – anymore. I quickly decided to fill the models with mineral oil, which absorbs some of the energy.”
MacKay, who will defend his thesis at 3mE on 28 June, performed his experiments at DRDC, the research and development arm of the Canadian Ministry of Defense. His goal: to develop a methodology with which one can predict more accurately when submarines will collapse. His doctoral research was part of a collaborative project by the Canadian Department of National Defence (DND) and the Netherlands Ministry of Defence.
The conventional technique to predict the pressures submarines can withstand results in a margin of error of 20 percent. So, you may for instance think that you can dive up to 1 kilometer deep, while in fact your hull will collapse at 800 meters. Narrowing down the error is no unnecessary luxury.
MacKay believes that the conventional technique – which involves analytical buckling equations, empirical design curves and simple numerical models – is terribly outdated. “The designers of submarines are conservative and are lagging behind. Computing power has grown exponentially, allowing for the use of finite element analysis instead,” says the researcher, who himself used finite element (FE) analysis.
“With FE one can accommodate the complex geometry, material, imperfections and structural response of real hulls, and one can assess the consequences of in-service damage due to, for example, collisions or corrosion.”
With his method, MacKay found that he narrowed the margin of error down to 10 percent. For landlubbers, this may not sound very reassuring. According to MacKay, though, “it’s a step in the right direction.”
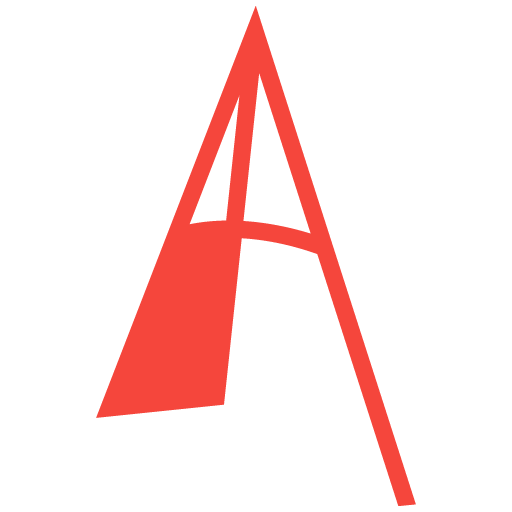
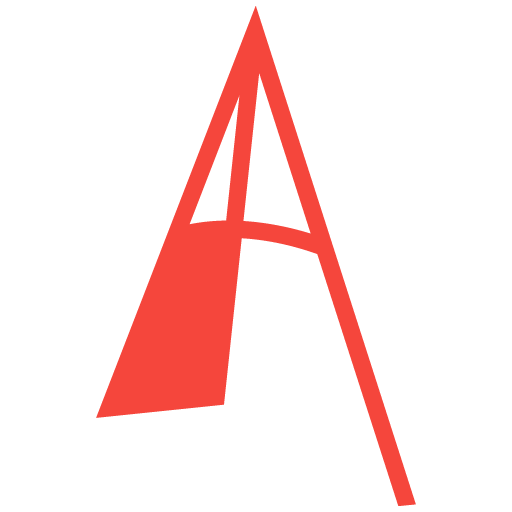
Comments are closed.