Elke student wil de mooiste stage op zijn cv zetten: Shell, Philips, liefst een internationale stage bij een industriegigant. Maar de overheid ziet dat een slagje anders.
Het midden- en kleinbedrijf moet ook – en veel vaker -profiteren van academische kennis. Dus worden stimuleringsprogramma’s bedacht om studenten bij kleine ondernemers te stationeren. Ook Shell heeft hiervoor een apart stageprogramma in het leven geroepen. In dat landelijke programma (SEE) hebben drie Delftenaren de eerste, tweede en de aanmoedigingsprijs gewonnen. Zij kozen voor de vrijheid van een klein bedrijf.
In een roeiboot zijn allerlei onderdelen van kunststof. De huid, de constructie, de riemen. Kasper Snijder, zevendejaars lucht- en ruimtevaart en actief bij Proteus-Eretes, vond dat de riggers ook wel eens verbeterd konden worden. Toevallig stuitte hij op de enige Nederlandse bouwer van roeiboten.
Snijder kende een bedrijfje in composietmaterialen van twee afgestudeerde lucht- en ruimtevaartstudenten die hem vroegen stage te komen lopen. Bij nadere beschouwing bleek het te gaan om een opdracht die de enige Nederlandse botenbouwer, Busman bv, bij het Delftse tweemansbedrijf had geplaatst. ,,Zij vroegen zich af of de rigger van een boot, het onderdeel waar de riemen op rusten, niet van kunststof gemaakt zou kunnen worden. Dat zou een lichtere constructie betekenen. Door een lichter gewicht ligt de boot minder diep en heeft hij minder weerstand.”
Een groot voordeel van een eventuele kunststof rigger is dat zij doorlopend gemaakt kan worden, in plaats van één rigger aan elke kant. Hierdoor zijn de krachten beter in balans en kunnen de zware spanten in een boot lichter gemaakt worden.
Een Zwitsers bedrijf had al eerder een kunststof rigger ontworpen die voor de roeier langs liep. ,,Dat had het nadeel dat de dol, het draaiende onderdeel waar de riem in ligt, bovenop de rigger moest staan. Daarom moest de rigger stevig uitgevoerd worden om alle krachten goed te kunnen opvangen.”
Snijder rekende een constructie door waarbij de rigger achter de roeier langsloopt. ,,Hierdoor kan de dol gemonteerd worden in het verlengde van de rigger. Ook de – voor roeiers heel belangrijke – dolhoek ligt hierdoor beter vast.”
Na twee maanden tekenen en rekenen besteedde Snijder veel tijd aan het maken van full-colour plaatjes. ,,Een goed plaatje zegt veel meer dan woorden. Volgens mij was dat ook een van de redenen om mij uit te kiezen voor de finale.”
Snijder verdiende met zijn presentatie de eerste prijs, duizend gulden plus een weekend Londen. ,,Voor de presentatie had ik een net pak gekocht. Die duizend gulden is dus al weer op.”
De toekomst voor productidentificatie ligt niet in streepjescodes, maar in denieuwe techniek van transponders: kleine kristallen die reageren op een elektromagnetisch veld. Maar wat als je wel een transponder hebt maar nog geen toepassingen?
Désirée van Baal, inmiddels afgestudeerd bij Industrieel Ontwerpen, kwam voor haar afstudeerstage terecht bij een klein bedrijfje met drie mensen met een elektrotechnische achtergrond. ,,Zij hadden een transponder ontworpen die niet bestond uit een chip, maar uit kristallen die bijvoorbeeld hoge temperaturen tot tweehonderd graden aankunnen.”
Van Baal werd gevraagd om de behuizing te ontwerpen voor deze transponder. ,,Toen ik vroeg: ‘Wat willen jullie eigenlijk doen met die transponders’, hadden ze geen antwoord. Een marktonderzoek hadden ze nooit gedaan.”
Van Baal onderzocht een tiental markten. ,,Producten die gesteriliseerd moeten worden zijn een logische keus. Uiteindelijk heb ik als meest veelbelovende markt het steriliseren van instrumenten voor de operatiezaal uitgekozen.” Met de transponder kunnen instrumenten dan in het hele ziekenhuis worden getraceerd, want bij transport door toegangspoortjes worden ze geregistreerd. ,,Je zou instrumenten waar haast bij is sneller kunnen laten schoonmaken.”
Van Baal vond het doorlopen van het hele ontwerpproces het leukste aan het project. ,,In zo’n klein bedrijf kun je alles zelf doen, het marktonderzoek, het onderzoek naar de specificaties tot aan het ontwerpen van de hittebestendige behuizing.”
In de wereld zijn er drie fabrikanten die schaalmodellen van de formule 3 bouwen. Eén daarvan zit in Nederland. Over enkele jaren worden in de EG strikte geluidsnormen van kracht waar deze auto’s nog ruim boven zitten. Jan Martens, vijfdejaars Technisch Natuurkunde, ontwierp een demper tijdens zijn stage.
,,Die schaalmodellen van een op acht produceren zesentachtig decibel, vergelijkbaar met een forse motorfiets. Volgens de Europese wetgeving moet dit autootje voldoen aan de hinderwetvergunning van tachtig decibel. Als je bedenkt dat de decibel schaal logaritmisch is, betekent dat twee keer zo zacht.”
Alvorens te beginnen aan het ontwerp van een demper, heeft Martens het schaalmodel doorgemeten. Hij werd met alle egards onthaald door de hobbyisten op de racebaan. ,,Toen ik daar stond met kabels, een microfoon en een joekel van een meetinstrument, kwam iedereen op me af. Iedereen wilde weten hoeveel zijn auto aan geluid produceerde. Toen ik vertelde dat ik van de TU kwam gingen hun ogen wijd open.”
Volgens Martens is dat ook het unieke van het kleinbedrijf. ,,Ik was meteen de expert. Alles wat ik zei werd meteen aangenomen. Alleen zijn er in zo’n klein bedrijf niet altijd mensen beschikbaar om bijvoorbeeld meteen een demper te bouwen.”
Martens identificeerde drie bronnen van geluid in de modellen: de motor, de uitlaat en de inlaat. ,,Ik kwam erachter dat de inlaat het meest lawaai veroorzaakt. Voor de inlaat bestaan geen dempers, maar wel voor de uitlaat.”
Toepassen van dezelfde dempers op de inlaat voldeed echter niet: geen enkele haalde de vereiste geluidsreductie. ,,Tot ik in de laatste week van mijn stage bedacht om gewoon een cilinder van vijftien centimeter op de inlaat te zetten. Dat werkte, het scheelde zeven decibel. Op een autootje van veertig centimeter is zo’n pijp van vijftien centimeter echter niet esthetisch verantwoord.” Binnenkort gaat hij daarom terug om de laatste geluidsmetingen te doen.
Elke student wil de mooiste stage op zijn cv zetten: Shell, Philips, liefst een internationale stage bij een industriegigant. Maar de overheid ziet dat een slagje anders. Het midden- en kleinbedrijf moet ook – en veel vaker -profiteren van academische kennis. Dus worden stimuleringsprogramma’s bedacht om studenten bij kleine ondernemers te stationeren. Ook Shell heeft hiervoor een apart stageprogramma in het leven geroepen. In dat landelijke programma (SEE) hebben drie Delftenaren de eerste, tweede en de aanmoedigingsprijs gewonnen. Zij kozen voor de vrijheid van een klein bedrijf.
In een roeiboot zijn allerlei onderdelen van kunststof. De huid, de constructie, de riemen. Kasper Snijder, zevendejaars lucht- en ruimtevaart en actief bij Proteus-Eretes, vond dat de riggers ook wel eens verbeterd konden worden. Toevallig stuitte hij op de enige Nederlandse bouwer van roeiboten.
Snijder kende een bedrijfje in composietmaterialen van twee afgestudeerde lucht- en ruimtevaartstudenten die hem vroegen stage te komen lopen. Bij nadere beschouwing bleek het te gaan om een opdracht die de enige Nederlandse botenbouwer, Busman bv, bij het Delftse tweemansbedrijf had geplaatst. ,,Zij vroegen zich af of de rigger van een boot, het onderdeel waar de riemen op rusten, niet van kunststof gemaakt zou kunnen worden. Dat zou een lichtere constructie betekenen. Door een lichter gewicht ligt de boot minder diep en heeft hij minder weerstand.”
Een groot voordeel van een eventuele kunststof rigger is dat zij doorlopend gemaakt kan worden, in plaats van één rigger aan elke kant. Hierdoor zijn de krachten beter in balans en kunnen de zware spanten in een boot lichter gemaakt worden.
Een Zwitsers bedrijf had al eerder een kunststof rigger ontworpen die voor de roeier langs liep. ,,Dat had het nadeel dat de dol, het draaiende onderdeel waar de riem in ligt, bovenop de rigger moest staan. Daarom moest de rigger stevig uitgevoerd worden om alle krachten goed te kunnen opvangen.”
Snijder rekende een constructie door waarbij de rigger achter de roeier langsloopt. ,,Hierdoor kan de dol gemonteerd worden in het verlengde van de rigger. Ook de – voor roeiers heel belangrijke – dolhoek ligt hierdoor beter vast.”
Na twee maanden tekenen en rekenen besteedde Snijder veel tijd aan het maken van full-colour plaatjes. ,,Een goed plaatje zegt veel meer dan woorden. Volgens mij was dat ook een van de redenen om mij uit te kiezen voor de finale.”
Snijder verdiende met zijn presentatie de eerste prijs, duizend gulden plus een weekend Londen. ,,Voor de presentatie had ik een net pak gekocht. Die duizend gulden is dus al weer op.”
De toekomst voor productidentificatie ligt niet in streepjescodes, maar in denieuwe techniek van transponders: kleine kristallen die reageren op een elektromagnetisch veld. Maar wat als je wel een transponder hebt maar nog geen toepassingen?
Désirée van Baal, inmiddels afgestudeerd bij Industrieel Ontwerpen, kwam voor haar afstudeerstage terecht bij een klein bedrijfje met drie mensen met een elektrotechnische achtergrond. ,,Zij hadden een transponder ontworpen die niet bestond uit een chip, maar uit kristallen die bijvoorbeeld hoge temperaturen tot tweehonderd graden aankunnen.”
Van Baal werd gevraagd om de behuizing te ontwerpen voor deze transponder. ,,Toen ik vroeg: ‘Wat willen jullie eigenlijk doen met die transponders’, hadden ze geen antwoord. Een marktonderzoek hadden ze nooit gedaan.”
Van Baal onderzocht een tiental markten. ,,Producten die gesteriliseerd moeten worden zijn een logische keus. Uiteindelijk heb ik als meest veelbelovende markt het steriliseren van instrumenten voor de operatiezaal uitgekozen.” Met de transponder kunnen instrumenten dan in het hele ziekenhuis worden getraceerd, want bij transport door toegangspoortjes worden ze geregistreerd. ,,Je zou instrumenten waar haast bij is sneller kunnen laten schoonmaken.”
Van Baal vond het doorlopen van het hele ontwerpproces het leukste aan het project. ,,In zo’n klein bedrijf kun je alles zelf doen, het marktonderzoek, het onderzoek naar de specificaties tot aan het ontwerpen van de hittebestendige behuizing.”
In de wereld zijn er drie fabrikanten die schaalmodellen van de formule 3 bouwen. Eén daarvan zit in Nederland. Over enkele jaren worden in de EG strikte geluidsnormen van kracht waar deze auto’s nog ruim boven zitten. Jan Martens, vijfdejaars Technisch Natuurkunde, ontwierp een demper tijdens zijn stage.
,,Die schaalmodellen van een op acht produceren zesentachtig decibel, vergelijkbaar met een forse motorfiets. Volgens de Europese wetgeving moet dit autootje voldoen aan de hinderwetvergunning van tachtig decibel. Als je bedenkt dat de decibel schaal logaritmisch is, betekent dat twee keer zo zacht.”
Alvorens te beginnen aan het ontwerp van een demper, heeft Martens het schaalmodel doorgemeten. Hij werd met alle egards onthaald door de hobbyisten op de racebaan. ,,Toen ik daar stond met kabels, een microfoon en een joekel van een meetinstrument, kwam iedereen op me af. Iedereen wilde weten hoeveel zijn auto aan geluid produceerde. Toen ik vertelde dat ik van de TU kwam gingen hun ogen wijd open.”
Volgens Martens is dat ook het unieke van het kleinbedrijf. ,,Ik was meteen de expert. Alles wat ik zei werd meteen aangenomen. Alleen zijn er in zo’n klein bedrijf niet altijd mensen beschikbaar om bijvoorbeeld meteen een demper te bouwen.”
Martens identificeerde drie bronnen van geluid in de modellen: de motor, de uitlaat en de inlaat. ,,Ik kwam erachter dat de inlaat het meest lawaai veroorzaakt. Voor de inlaat bestaan geen dempers, maar wel voor de uitlaat.”
Toepassen van dezelfde dempers op de inlaat voldeed echter niet: geen enkele haalde de vereiste geluidsreductie. ,,Tot ik in de laatste week van mijn stage bedacht om gewoon een cilinder van vijftien centimeter op de inlaat te zetten. Dat werkte, het scheelde zeven decibel. Op een autootje van veertig centimeter is zo’n pijp van vijftien centimeter echter niet esthetisch verantwoord.” Binnenkort gaat hij daarom terug om de laatste geluidsmetingen te doen.
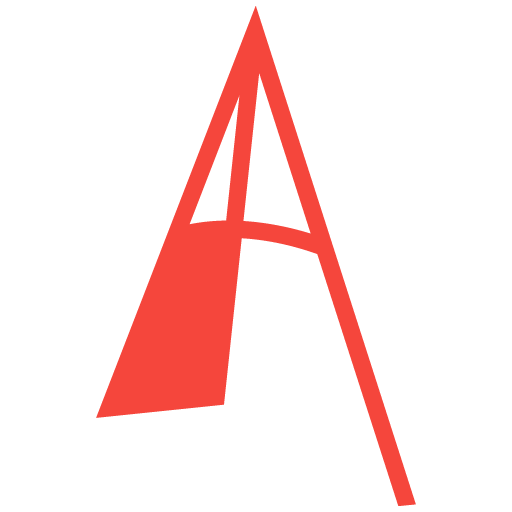
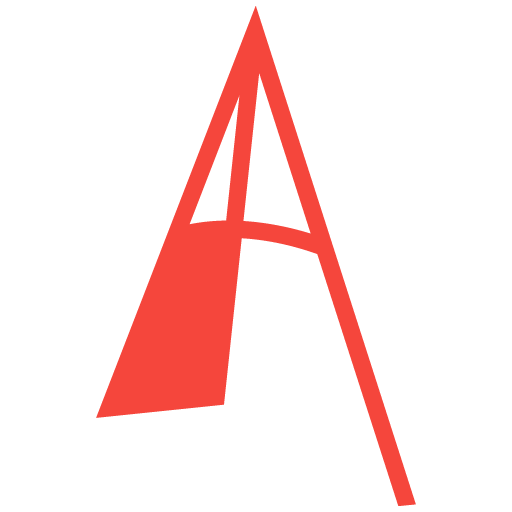
Comments are closed.