TU Delft researchers are developing new coatings with unicellular algae, that may prevent corrosion in aluminium airplane structures.
Santiago Garcia (left) and Paul Denissen develop an environmentally friendly alternative to chromium-6 coating with the external skeletons of diatoms. (Photo: Tomas van Dijk)
“And here are our pets. Thousands of them.” PhD researcher Paul Denissen is giving a tour through the Novel Aerospace Materials group’s lab, a group that lives up to its name. The ‘pets’ Denissen is referring to are diatoms, a group of unicellular algae. The PhD researcher picks up a little glass container with murky sea water from the windowsill. He and his supervisor, Associate Professor Santiago Garcia, are using the algae to create a revolutionary new kind of corrosion protective coatings.
Diatoms have the unique feature of forming highly ordered hollow porous silica exoskeletons, called frustules. Typically these consist of two symmetrical sides held together. Because of their characteristics, the diatom exoskeletons are described as forming ‘pill-box’ structures. The availability, morphological characteristics and potential application of the bio-based diatom exoskeletons as carriers has recently attracted significant attention in the biomedical field where their use as drug delivery systems has been studied.
But they have not only attracted attention in the medical field. At the Novel Aerospace Materials group, the two researchers are using these microalgae as carriers for corrosion inhibitors. These inhibitors are chemical compounds that, when added to a liquid or gas, reduce the corrosion rate of metals.
Carcinogenic salt
An infamous example of a corrosion inhibitor is chromium-6. This salt is extremely effective, but is also carcinogenic. Because of its toxicity, chromium-6 is banned in the EU. There is one exception, however. Chromium-6 is permitted in situations where there are no good alternatives, such as in aircraft corrosion prevention. The TU Delft research focuses on using the external skeletons of diatoms to develop an environmentally friendly alternative.
Chromium-6 is a so-called active corrosion-inhibitor. When a surface treated with chromium-6 is damaged, through scratches for example, chromium-6 ions are released. These then create a thin layer of chromium oxide on the exposed metal surface, preventing further corrosion.
There are a number of alternative more environmentally friendly corrosion-inhibitors that are also very good at creating protective barriers. Take Cerium salts, with which the TU Delft researchers have been experimenting for years. Unlike chromium-6, however, these alternative inhibitors oxidise only once and the protective layer they create is not permanent. Long-term protection therefore requires the continuous release of these inhibitors. And that is where the diatoms come into play.
Fill the exoskeletons with the alternative corrosion-inhibitors, add the loaded shells to the primer coating and the pill-box structure will prevent the unwanted chemical reaction between inhibitors and coating, the Delft researchers reasoned. Moreover the pores would allow the immediate and sustained release of these inhibitors when the protective layers are damaged and the metal surface is exposed.
‘We saw full protection’
The algae shells are easily available at low cost. Diatoms can be cultivated in bioreactors. Or one can use diatomaceous earth, which consists of the fossilised remains of diatoms. Diatomaceous earth can be mined. Diatoms from diatomaceous earth are often used as a filtration aid and as a mild abrasive in products such as metal polish and toothpaste. Initially, the two TU Delft researchers are experimenting with diatomaceous earth. But one disadvantage of this material is that most diatoms are broken and that intact skeletons in the earth are from different species and thus differ in shape and size.
Still, preliminary results with diatomaceous earth seem promising. The researchers performed test where they made one millimetre wide scratches on samples of airplane aluminium which were treated with a variety of their test ‘algae-coatings’. The samples were subsequently immersed in a highly corrosive environment. “We saw full protection from corrosion, even after 30 days of immersion. Only a couple of alternative solutions come this close to the results obtained with chromium-6”, Denissen says.
The next step in the process is to pick one specific diatom species with the optimal shape, size and nano pores, and cultivate it instead of using the diatomaceous earth grit with its myriad of shapes and sizes. “To do that, we will have to install a bioreactor here in the lab,” says Garcia. “And we will look for marine biology interns to work with us.”
‘Next we have to install a bioreactor’
There are still many hurdles to cross before diatoms find their way into coatings though. “The Dutch Ministry of Defence wants proof that alternatives will protect their military equipment for 20 years,” Denissen says. “But there are no good methods to accelerate the process and to evaluate and validate it in a short time-span.” And many of the tests used to validate the efficacy of new coating materials are designed specifically for chromium-6. “It is not a level playing field. It means that you have to prove that your alternative coating behaves in a similar way to chromium-6, rather than prove that it provides adequate protection.”
But rather than waiting for coating manufacturers to replace chromium-6, airplane manufacturers are now actively developing their own solutions as well and the TU Delft researchers are at the heart of these developments.
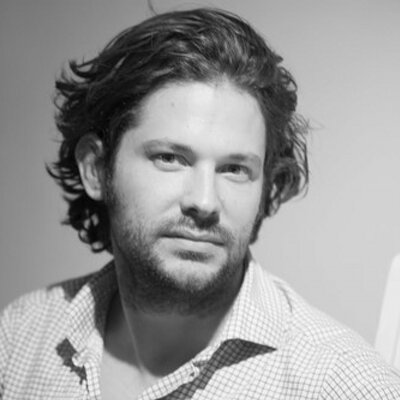
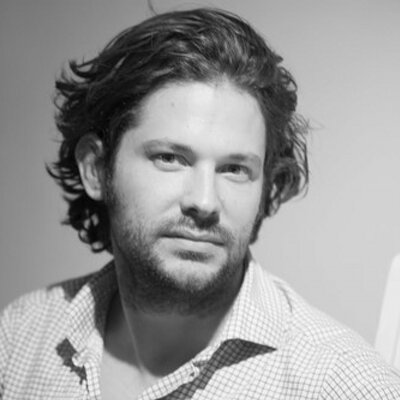
Comments are closed.