Europa is voor elektrische producten afhankelijk van buitenlandse metalen. Binnen een EU-programma ontwikkelt de groep van Peter Rem technieken om waarde uit afval te winnen.
Metaalbedrijf MYNE in Harderwijk. (Foto: MYNE)
In het recycling lab van Civiele Techniek liggen kratten vol printplaten te wachten op verwerking. Ze komen uit radio’s, televisies, versterkers, telefoons en computers. Promovendus Max van Beek heeft een kennersblik ontwikkeld. Vroege printplaten zijn gebaseerd op papier en hebben een beige kleur, vertelt hij, moderne printplaten van glasvezel zijn groen. Componenten als weerstanden, condensatoren en transistors worden in de loop van de tijd steeds kleiner, chips daarentegen steeds talrijker en gecompliceerder.
Veel van die onderdelen bevatten kleine hoeveelheden zeldzame en waardevolle metalen zoals goud, zilver en palladium. Zijn die terug te winnen zoals de circulaire economie beoogt? Recyclingexpert prof.dr.ir. Peter Rem (faculteit Civiele Techniek en Geowetenschappen) denkt van wel: “Bij lage concentraties is terugwinning van zeldzame metalen niet lonend, maar bij hogere concentraties wel. Ik schat dat Europees elektronisch afval na scheiding en concentratie voldoende materiaal bevat voor één of twee terugwinningsfabrieken.”
Hoe staat het met de hoeveelheid elektrische en elektronische apparatuur en de inzameling ervan in Europa? De Engelstalige termen daarvoor zijn electric & electronic equipment (EEE) en waste electric & electronic equipment (WEEE). De jaarlijks verkochte hoeveelheid apparatuur met stekker of batterij (EEE) is sinds 2012 gestegen van 7,6 miljoen ton naar 12,4 miljoen ton in 2020, meldt het Europese bureau voor statistiek Eurostat. Geen wonder, want vrijwel alle producten bevatten tegenwoordig elektronica of elektromotoren. De hoeveelheid ingezameld elektrisch en elektronisch afval (WEEE) steeg van 3 naar 4,7 miljoen ton per jaar (10,5 kilogram per Europeaan) en bleef daarmee percentueel iets achter bij de aanschaf.
De Europese Unie wil steeds meer elektrisch en elektronisch afval inzamelen. In 2016 was het doel om 45 procent van het gewicht in te zamelen dat in de drie jaren ervoor op de markt was gekomen. Dat streefgetal bedraagt vanaf 2019 65 procent. In werkelijkheid lag in 2020 het Europees ingezamelde gemiddelde op 45 procent (de doelstelling van vier jaar eerder). De conclusie is dat de inzameling van elektrische en elektronische apparatuur in Europa beter kan.
Terugwinning
Maar dan? Wat te doen met dat ingezamelde afval? Tienduizend ton elektrisch en elektronisch afval per jaar klinkt veel, weet recycleprofessor Peter Rem, maar is slechts 1 procent van de miljoen ton bodemas die vuilverbranders in Europa jaarlijks produceren. Bodemas is het materiaal dat overblijft na verbranding van afval in een afvalenergiecentrale. Dat kleine percentage maakt de concentratie van waardevolle metalen veel te laag om ze uit bodemas terug te winnen. Wereldwijd wordt er overigens vijf keer zoveel stekker- en batterijafval weggegooid, namelijk 50 miljoen ton per jaar.
Daarom werken onderzoekers en industrie aan technieken om zoveel mogelijk waarde terug te winnen uit die aanzwellende afvalstroom. De groep van Peter Rem is een van negentien partners die binnen het Europese Horizon2020 onderzoeksprogramma Peacoc samenwerkt aan de ontwikkeling van ‘unieke, goedkope en milieuvriendelijke technologieën voor een efficiënte terugwinning van goud, zilver en platina uit afval’ aldus de website. Het onderzoeksprogramma is in 2021 van start gegaan en loopt tot april 2025.
Max van Beek en dr. Lin Wang gebruiken de rolsorteermachine om componenten te scheiden op basis van de kleinste afmeting. (Foto: Jos Wassink)
30-40 bakjes
Promovendus Max van Beek vertelt dat hij met 1 kilogram elektronische componenten begint met ongeveer 10 procent aan waardevolle componenten. Zijn onderzoek maakt deel uit van het NWO-programma Circular Circuits. Printplaten met elektronica zijn een klein maar waardevol deel van het WEEE-afval. Het gewichtspercentage loopt uiteen voor verschillende apparatuur (van warmtepomp tot laptop) maar ligt in de orde van 5 procent. Daar spitst het Delftse onderzoek zich op toe.
Het elektronica-afval in de emmer is het resultaat van het met de hand uit elkaar halen van apparatuur en de demontage van componenten van de printplaat (‘depopulation’). Dat afval doorloopt een serie van scheidingstechnieken: zeven, rolsorteren (componenten vallen tussen twee draaiende cilinders door, de plaats is afhankelijk van de dikte van de component); magnetische scheiding (een schuin geplaatste permanente plaatmagneet trekt componenten tegen een transportband. Hoe magnetischer de componenten hoe verder ze komen); en magnetische dichtheidsscheiding, waarover later meer. Aan het eind van het proces is er van de kilo elektrisch en elektronisch afval 150 gram over waarvan 96 gram (64 procent) bestaat uit waardevolle componenten.
De concentratie van waardevol materiaal wordt zo met een factor 6,4 verhoogd. Dat is van belang voor verdere verwerking met zogenaamde smelters om kostbare metalen terug te winnen. Smelters (de dichtstbijzijnde staan in Duitsland, België en Zweden) zijn roterende, schuinstaande cilinders met gesmolten koper waar het afval in belandt voor recycling. Plastic en printplaatresten verbranden of drijven als slakken op het vloeibare koper. Edele metalen zoals de sporen goud, zilver en platina lossen op in het vloeibare koper, maar zijn daaruit terug te winnen als in een metallurgische raffinaderij. Smelters staan voor een kostbaar en energiehongerig proces (kosten circa 900 euro per ton) dat alleen economisch haalbaar is bij een voldoende hoge beginconcentratie.
Delftse techniek
De nieuwste en meest geavanceerde stap in scheiding van elektrisch en elektronisch afval is zogeheten magnetische dichtheidscheiding (MDS). Eerder ontwikkelde Rem deze techniek om plastics van elkaar te scheiden op basis van minieme dichtheidsverschillen. Nu past postdoc dr. Lin Wang de techniek aan voor een optimale scheiding van elektronische componenten en kabels.
De bak waarin de scheiding plaatsvindt ziet eruit alsof er olie in staat, maar dat is schijn. De zwarte vloeistof is water met een suspensie aan magnetische nanodeeltjes. Een sterke permanente plaatmagneet onder de bak oefent een aantrekkende kracht uit op de vloeistof die de dichtheid vergroot. Onderdelen die in water zouden zinken blijven daardoor drijven.
De magneetplaat staat schuin onder het bassin opgesteld waardoor de dichtheid in de vloeistof afneemt met de afstand tot de magneet. Het invoerpunt bevindt zich aan de kant waar de afstand tot de magneet het kleinst is, en de dichtheid het grootst. Hier drijft alles nog. Onderdelen in de oplossing glijden langs lijnen met gelijke dichtheid en belanden op de bodem op een afstand van het invoerpunt die overeenkomt met de dichtheid.
‘Het zijn goedkope scheidingstechnieken’
Wang pompt de zwarte vloeistof weg en laat zien waar de componenten terechtgekomen zijn. Links met de hoogste dichtheid liggen (niet magnetische) metalen delen zoals aluminium koelvinnen en computerchips, in het midden liggen tulppluggen en andere connectoren van plastic en metaal, helemaal rechts liggen voornamelijk plastic onderdelen. Voor terugwinning van edelmetalen is het linkerdeel het meest interessant.
“Het zijn goedkope scheidingstechnieken”, benadrukt Rem. De magneten zijn permanent en het enige energieverbruik zijn wat draaiende elektromotoren. MDS is de voorlopige sluitsteen in het sorteer- en opwerkingsproces van elektrisch en elektronisch afval. Aan het eind van de rit is de inhoud van de emmer met gemengd elektronisch afval gesorteerd in 30 tot 40 bakjes.
Businessmodel
Begin november werd een industrieel prototype MDS-machine in het lab gebracht. Tot nu toe moest Wang het bassin vullen en leegpompen voor iedere nieuwe lading afvalcomponenten. Bij de industriële machine loopt onder het MDS-sorteerbassin een lopende band. Die zorgt voor een continue afvoer van gesorteerde componenten. Metaalrecyclingbedrijf MYNE, voorheen Reukema, uit Harderwijk sponsort het prototype.
Directeur Martijn van de Poll van het bedrijf nam al in 2014 contact op met Peter Rem. In die tijd werd al het elektronica-afval naar Azië geëxporteerd om daar met de hand uit elkaar gehaald te worden. Van de Poll zag elektronica-afval als een van de snelst groeiende afvalmarkten en zocht een manier om daarin mee te draaien. Zijn vraag aan Rem luidde: “Kunnen jullie een sorteertechnologie ontwikkelen die goedkoper is dan de handsortering in Azië?” Dat was het startpunt voor het onderzoek naar verwerking van elektrisch en elektronisch afval in Delft.
Metaalrecyclingbedrijf MYNE koopt inmiddels elektroschroot en kabelbomen uit Nederland, België, Duitsland en Frankrijk. Dat materiaal gaat niet meer naar Azië. De eerste MDS-machine die goedkoper moest sorteren dan handjes in Azië, is na tien jaar ontwikkeling gebouwd en staat voor tests in de het recycling lab van Civiele Techniek. De machine kan naar verwachting 1,5 ton per uur scheiden.
“Een recycling plant moet toch echt wel 30 duizend ton per jaar verwerken”, schat TU-alumnus Van de Poll (hij studeerde in 2001 af als technisch bestuurskundige aan de TU Delft). “Maar liever nog 50 tot 100 duizend ton om een installatie economisch goed draaiend te houden. Als je dan terugrekent kom je op vijf tot tien van de MDS-scheiders.”
“Als wij vijf van die machines aanschaffen dan doen we dat omdat we denken dat er een businessmodel in zit”, zegt Van de Poll die met zijn bedrijf MYNE ook deelneemt aan Circular Circuits. “We zien druk van alle kanten; er komt wetgeving aan op recycling om al bij het ontwerp rekening te houden met het hergebruik van grondstoffen. De grootste stap is nu wel dat de auto-industrie en Ikea bezig zijn met hun CO2-voetafdruk, en met herleidbaarheid van grondstoffen. Dat is een gigantische stap in vergelijking met vijf jaar geleden.”
Eerder ontwikkelde MYNE samen met de TU Delft de Xortrer, een sorteerstraat met 64 robots voor aluminiumlegeringen. (Foto: MYNE)
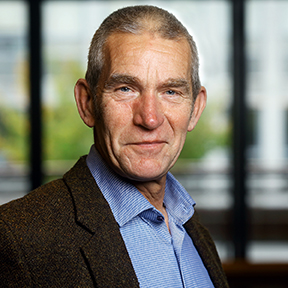
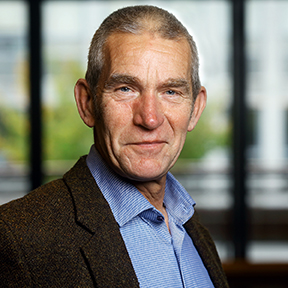
Heb je een vraag of opmerking over dit artikel?
j.w.wassink@tudelft.nl
Comments are closed.