This year, first-year Mechanical Engineering students had to design a safe door. A different team got the keys and had to unlock it, without forcing. That was not always easy.
For the design competition, students dove into the role of master crackers. (Photo: Thijs van Reeuwijk)
In the project Mechanical design engineering, first-year students Mechanical Engineering learn to draw by hand and build carton models. After years of building marble machines, the design assignment took a different direction. “I wanted them to design an actual tool,” explains creator and lecturer Erik Thomassen (Faculty of Mechanical Engineering). He initially considered a rivet tool project, but it was too straightforward, leaving little room for creativity.
The safe door project is a different story. The material is 4 millimetre thick MDF (fibreboard) cut by a laser, making complex shapes easy to create. The door requires two keys, with a number code also counting as one of the keys. Once unlocked, the door should fall out of its frame naturally, without pulling or forcing.
The 128 groups, each with seven students on average, had eight weeks to design and build their safe doors. Monday, 28 October 2024, was the big day when each design was publicly tested.
Escape Challenge
Thomassen set up the tests as an ‘escape challenge’. Eight safe doors were displayed at the front of the lecture hall. Representatives from each team stood not by their own door but by the next one over so that a student in another team had to unlock it purely by following instructions and using two keys. Once they succeeded, they could grab the keys to the next door. Meanwhile, the clock was ticking. The eight teams that opened all the doors the fastest were the winners. Times ranged from just over three minutes to well beyond 10.
The audience in the hall had the best view, watching lock mechanisms move, pins slide, pieces fall out, and locks open. “A bit more,” someone would call out. And if someone got frustrated and yanked the door, the crowd would shout, “Whoa, whoa!” or “Slide it, to the left.”
The hardest part for the first years? Watching someone else struggle to open their design and resisting the urge to jump in. Instructions were allowed. “Turn it – no, not that way. The other way. Yes, like that, now pull!”
Students were welcome to explain their designs over the mic while the doors were being opened. “Your own design is always the simplest,” one noted. “Too bad they don’t see it that way,” the interviewer shot back.
To Science
In the end, all the doors gave in – sometimes with a bit of force, advice from the designers, or simply a quick peek over the barrier to see what was going wrong. No jury objected. The ‘challenge’ was more theatre than competition.
Outside the lecture hall, students immediately began disassembling the safes. Rings, bolts, and nuts went into separate trays, while MDF pieces went into a collection box. The alternative was to donate the door to Thomassen as a teaching aid for next time. Student Thom Weber opted for this and ceremoniously left his team’s creation ‘to science’.







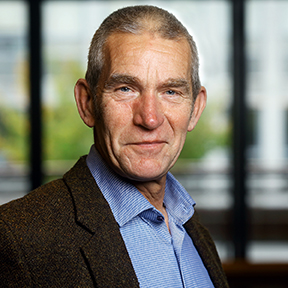
Do you have a question or comment about this article?
j.w.wassink@tudelft.nl
Comments are closed.