Imagine an aircraft itself showing whether and where damage has occurred after a hard landing. The European ReMAP research project is working on it.
Dr. Nan Yue en Agnes Broer at the press mimicking loads on aircraft panels (Photo: Jos Wassink)
Promovendus Agnes Broer en onderzoeker dr. Nan Yue zijn voor de foto even terug in het Structures & Materials-laboratorium van Luchtvaart- en Ruimtevaarttechniek. Daar hebben ze de afgelopen twee jaar een vliegtuigstructuur van ongeveer een vierkant meter belast onder een hydraulische pers. Het speciaal daarvoor gemaakte paneel was volgeplakt met tientallen licht- en geluidssensoren om de conditie van het composietmateriaal te kunnen volgen tijdens de kleine half miljoen schokken waar het aan onderworpen werd.
“We hebben de krachten nagebootst die op een vliegtuigvleugel werken”, vertelt Broer. “Bij turbulentie of een hobbelige landing bewegen de vleugels op en neer ten opzichte van de romp. Het meest kritische punt is de verbinding tussen vleugel en romp. Daar kan schade ontstaan.” Dus lieten de onderzoekers de hydraulische pers de herhaalde belasting van opstijgen en landen opwekken die een vliegtuig in dertig jaar doormaakt, en dat in een periode van dagen of weken. Die proeven werden een groot aantal keer herhaald met verschillende panelen en toenemende belastingen.
Sensors
PhD candidate Agnes Broer and fellow researcher Dr Nan Yue are back for a picture in the Aerospace Structures & Materials laboratory where, over the past two years, they have been loading an aircraft structure measuring about one square metre under a hydraulic press. The specially fabricated panel was packed with dozens of light and sound sensors to monitor the condition of the composite material during the nearly half million impacts it was subjected to.
“I simulated the forces acting on an aircraft,” says Broer. “The wings move up and down in relation to the fuselage during turbulence or a bumpy landing. I simulated this cyclic load on the test bench. The most critical point where damage can occur is the connection between wing and fuselage.” In a period of just a few weeks, the hydraulic press applied the repeated load of take-off and landing that an aircraft goes through in 30 years.
And unlike an aircraft, here the panel was loaded so heavily that it collapsed. At what pressure does that happen? Does fatigue play a role? How does a panel actually fail?
“We tested the panel to its breaking point,” says Broer. “We used the sensors to watch the damage accumulate. Built-in optical fibre and acoustic sensors acted as the eyes and ears of the material, allowing us to see what normally remains hidden.”
Researcher Yue shows a crushed panel. To be honest, it still looks fine. “No,” she says, “look at those dark diagonal stripes in the panel. Those aren’t normally there. That’s how you can tell it’s broken.”
Hidden damage is a big problem with the carbon composite material that many modern aircraft are made of. You can’t see any damage from the outside, but it could still be there. That’s why extensive inspections with various techniques to detect hidden damage are prescribed as a mandatory part of maintenance. Wouldn’t it be nice if sensors in the aircraft could indicate if and where damage has occurred? That concept is known as Structural Health Monitoring (SHM).
“Ingebouwde optische vezels en akoestische sensors fungeerden als de ogen en oren van het materiaal waardoor zichtbaar werd wat normaal verborgen blijft.” Foto: Jos Wassink)
Zooming out
Broer’s materials research was part of the four-year European ReMAP (Real-time Condition-Based Maintenance for Adaptive Aircraft Maintenance Planning) research programme that started in 2018 as part of the Horizon 2020 European innovation programme. Partners in the research are aircraft manufacturer Embraer (Portugal) and composites manufacturer Optimal Solutions (Portugal). The sensors were supplied by Cedrat Technologies (France) and Smartec CA (Switzerland). In addition to the University of Patras, the French Ecole Nationale Superieur d’Arts en Metiers was also involved, especially in the data acquisition.
The ultimate goal of the research is not just the monitoring of the structural condition of a single aircraft (SHM) but an automated and integrated maintenance system of an entire fleet of aircraft that is based on need rather than a fixed maintenance schedule. That ideal is known as the Integrated Fleet Health Management Tool. TU Delft and KLM are working on developing this tool in collaboration with no fewer than 11 international partners.
The next step is a six-month practical test at KLM starting in September 2021. This will involve testing the diagnostics and condition prediction (‘prognostics’) of aircraft, as well as adaptive software for maintenance planning.
Light sensors
The aircraft panel in the test bed is literally stuffed full of sensors. Do the researchers think that aircraft manufacturers will also install sensors in the fuselage, landing gear and wings? Broer thinks so. Not only because of the advantage in maintenance, but also because built-in sensors will enable aircraft manufacturers to build lighter aircraft. And in aviation, lighter is better. It has always been that way.
- The data from the tests, which were carried out at both TU Delft and the University of Patras (Greece), are being presented on Wednesday 16 June with some ceremony. Agnes Broer and her fellow researcher Dr Nan Yue will speak at the press conference, as will project coordinator Dr Bruno Santos and research leader Dr Dimitrios Zarouchas.
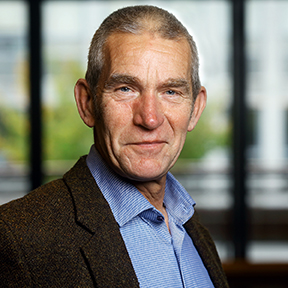
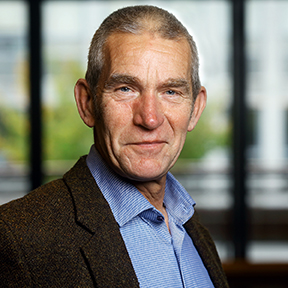
Do you have a question or comment about this article?
j.w.wassink@tudelft.nl
Comments are closed.