De Renault Clio heeft kunststof spatborden en de motorkap van de Citroen BX is eveneens van plastic. Steeds meer onderdelen van auto’s worden van kunststof gemaakt.
Was vroeger alleen de bumper van plastic, tegenwoordig zijn er auto’s waarvan de gehele carrosserie uit kunststof bestaat. De koper wil echter wel dat het plastic onderdeel dezelfde kleur heeft en net zo mooi glanst als de rest van de auto. De lak die daarvoor nodig is, blijkt de kunststof brosser te maken. Gronings chemicus dr. Martin Bosma onderzocht hoe dat komt en wat eraan te doen is.
Het grote voordeel van kunststof is dat het niet roest en dat het niet veel weegt, waardoor brandstofverbruik en uitstoot van schadelijke stoffen verminderen. Bovendien zijn de investeringskosten lager en de flexibiliteit groter bij het vervaardigen van kunststof onderdelen. ,,Je ziet dat de carrosserie van sommige sportwagens, die in kleine hoeveelheden gemaakt worden, geheel van kunststof is, omdat het persen van metalen onderdelen voor zo’n kleine oplage niet rendabel is”, zegt Bosma. Hij promoveerde 14 oktober.
Waarom worden, gezien al deze voordelen, dan nog niet alle auto’s van kunststof gemaakt? Bosma: ,,Recycling van kunststof is nog steeds een probleem. Hergebruikte plastics bestaan onbedoeld vaak uit verschillende kunststoffen door elkaar heen, waardoor ze niet meer geschikt zijn voor hoogwaardige toepassingen. ,,Dan is het alleen nog maar goed genoeg voor bermpaaltjes. Het is dus belangrijk dat materialen gescheiden gehouden worden.”
In Duitsland moeten alle auto’s na gebruik weer terug naar de fabrikanten. In Duitsland mag namelijk sinds twee jaar geen kunststof meer verbrand worden. De fabrikanten proberen nu ook steeds meer dezelfde kunststof voor de verschillende auto-onderdelen te gebruiken zodat hergebruik later weer makkelijker wordt.
,,De lak op de kunststof is wat hergebruik betreft minder gunstig, maar toch vaak een noodzakelijk kwaad”, stelt Bosma. ,,Nog afgezien van het feit dat de klant vindt dat de auto mooi van kleur en glans moet zijn, en er dus niet uit moet zien als een tupperware bakje, beschermt lak de kunststof tegen UV-straling en oplosmiddelen zoals benzine. Bovendien zijn lakken harder dan de plastic carrosserie waardoor het geheel beter bestand is tegen krassen.”
Een probleem is echter dat de lak het kunststof sneller doet breken. Dat is een vervelende eigenschap, zeker bij autobotsingen. Bros breken van materiaal biedt de passagiers minder bescherming dan wanneer het materiaal alleen vervormt, ofwel taai deformeert. Het bros breken van materialen, versplinteren, wil de automobielindustrie dus ook zoveelmogelijk proberen te voorkomen.
Dit ‘oppervlakteverbrossingseffect’ is een bekend probleem bij het lakken van kunststof. Ondanks de geringe dikte van de lak (ongeveer 0,05 millimeter) is gelakte kunststof door dit effect zwakker dan ongelakte kunststof. Bosma deed bij Akzo onderzoek naar deze problematiek. ,,Doel was het uitzoeken welke parameters een rol spelen bij de verbrossing van de kunststof en het opstellen van een model dat het breukgedrag van gelakte kunststoffen beschrijft.”
Kerf
Vroeger was de veronderstelling dat de verzwakking van de kunststof altijd veroorzaakt werd door de oplosmiddelen in de lak. Dat blijkt niet altijd het geval. ,,Men heeft namelijk de treksterkte van een stuk kunststof dat gelakt is geweest maar waar de lak weer vanaf geschuurd is, vergeleken met een ongelakt stuk kunststof. Deze bleek gelijk te zijn.” De oplosmiddelen hebben in dit geval dus geen invloed gehad.
De verklaring daarvoor ligt ergens anders. Lak breekt onder invloed van trekspanning eerder dan het kunststof substraat waarop het gehecht zit, omdat lak harder is en dus minder rekbaar is. Als de lak eenmaal gescheurd is dan groeit de scheur vaak door in het substraat. ,,Vergelijk het met een overhemd. Als daar eenmaal een scheurtje in zit, dan trek je hem heel gemakkelijk helemaal kapot”, legt Bosma uit.
Zo ook met de lak. Een scheur in een goed hechtende lak kan als een soort kerf werken. Als de spanningsconcentratie aan de tip van deze kerf erg hoog wordt, zal de scheur door het substraat groeien en een breuk veroorzaken. Een dergelijke kerf in de lak kan bijvoorbeeld ontstaan door trekspanning vanwege vervorming bij een botsing.
Diverse factoren zijn van invloed op het breukgedrag van materialen. Uiteraard speelt de temperatuur een belangrijke rol. ,,Iedereen weet dat een boterhamzakje dat net uit het vriesvak komt sneller breekt dat een zakje bij kamertemperatuur. Dit geldt voor vrijwel alle materialen”, zegt Bosma. Alleen de temperatuur waarbij het materiaal van taai overgaat in bros is voor materialen verschillend. Lak en kunststof zijn bij hoge temperaturen even taai. Dan zal de lak ook geen negatief effect hebben op de oppervlakteverbrossing. ,,Als je dan toch per se een deuk in je auto wil rijden, dan kun je dat maar beter in de Sahara doen.” Maar bij temperaturen van bijvoorbeeld min vijftig is lak veel brosser dan kunststof. Daardoor vormt de lak de zwakke schakel en bezwijkt het geheel eerder.
Testen
Bosma ontwikkelde een aantal testen om deze theorie te onderbouwen, parameters te ontdekken en het proces te kwantificeren. Hij deed trekproeven en ontwikkelde scheurtesten bij verschillende temperaturen en hechtingstesten.
In de trekproeven werden de twee uiteinden van een al dan niet gelakt kunststof staafje in een trekbank geklemd. De staaf werd met hoge snelheid, duizend keer zijn eigen lengte per minuut, uit elkaar getrokken. Daarbij keek hij naar deuitreklengte en de kracht waarbij het materiaal het begaf. Tevens werd tijdens de meting gekeken wanneer de lak kapot ging. Dit werd geregistreerd door de weerstand te meten van een heel dun laagje grafiet dat van tevoren aangebracht was aan de gelakte zijde. Zodra de weerstand oneindig werd, wist Bosma dat het grafiet, en dus de lak, gebroken was.
Bij de scheurtesten keek Bosma met de microscoop naar de scheurranden van de lak bij verschillende temperaturen. Als het materiaal taai deformeert zie je een gladde scheurrand. Bij bros breken een sterk gekartelde scheurrand. Deze overgangstemperatuur is heel scherp en wordt de scheurovergang genoemd. Men streeft ernaar dat die temperatuur voor de lak zo laag mogelijk is en dus zo dicht mogelijk bij de scheurovergang van het kunststof komt.
Met de hechtingstest werd bepaald hoeveel energie er nodig is om een eerste begin van onthechting te veroorzaken. Uit deze meting bleek onder andere dat de mate van hechting van de lak sterk beïnvloed wordt door de voorbehandeling van het kunststof alvorens de lak wordt aangebracht. Schoonmaken met loog en alcohol verbetert de hechting aanzienlijk.
Taaiheid
Bosma concludeerde dat verbrossing afhankelijk is van een aantal factoren zoals de taaiheid van de lak, de hechting van de lak aan het substraat, breukstoppend vermogen van het substraat en de dikte van de lak.
,,Het is allemaal heel logisch”, zegt Bosma. ,,Als de lak taai is en dus niet breekt zal het substraat ook niet bezwijken. Als de lak niet sterk hecht en loslaat van het substraat zodra het onder te grote spanning komt, is er ook geen probleem. De hechting van de lak kan natuurlijk niet oneindig zwak zijn want je wil ook niet dat de lak van de auto waait als je tachtig rijdt. En als het substraat scheuren stopt, in vaktermen minder kerfgevoelig is, zal het niet breken door een kerf in de lak en is er ook niets aan de hand.” Tenslotte geldt, hoe dikker de lak, hoe groter de spanning onder in de kerf aan het grensvlak met de kunststof en dus hoe sneller het substraat bezwijkt. Zo dun mogelijk lakken dus. Deze factoren heeft Bosma kwantitatief in een model verwerkt.
De volgende stap is nu aan de autolakindustrie. Die moet er nu eentje uitzoeken die hard is maar toch taai, of een lak die vrij goed hecht maar die loslaat onder extreme omstandigheden. ,,De meeste gebruikte lakken bestaan uit wel twintig verschillende componenten waarvan niet altijd iedereen precies weet waar sommige componenten voor dienen.” Wie weet komt er nu wel weer een geheimzinnig component bij.
Steeds meer delen van de carrosserie zijn van kunststof
De Renault Clio heeft kunststof spatborden en de motorkap van de Citroen BX is eveneens van plastic. Steeds meer onderdelen van auto’s worden van kunststof gemaakt. Was vroeger alleen de bumper van plastic, tegenwoordig zijn er auto’s waarvan de gehele carrosserie uit kunststof bestaat. De koper wil echter wel dat het plastic onderdeel dezelfde kleur heeft en net zo mooi glanst als de rest van de auto. De lak die daarvoor nodig is, blijkt de kunststof brosser te maken. Gronings chemicus dr. Martin Bosma onderzocht hoe dat komt en wat eraan te doen is.
Het grote voordeel van kunststof is dat het niet roest en dat het niet veel weegt, waardoor brandstofverbruik en uitstoot van schadelijke stoffen verminderen. Bovendien zijn de investeringskosten lager en de flexibiliteit groter bij het vervaardigen van kunststof onderdelen. ,,Je ziet dat de carrosserie van sommige sportwagens, die in kleine hoeveelheden gemaakt worden, geheel van kunststof is, omdat het persen van metalen onderdelen voor zo’n kleine oplage niet rendabel is”, zegt Bosma. Hij promoveerde 14 oktober.
Waarom worden, gezien al deze voordelen, dan nog niet alle auto’s van kunststof gemaakt? Bosma: ,,Recycling van kunststof is nog steeds een probleem. Hergebruikte plastics bestaan onbedoeld vaak uit verschillende kunststoffen door elkaar heen, waardoor ze niet meer geschikt zijn voor hoogwaardige toepassingen. ,,Dan is het alleen nog maar goed genoeg voor bermpaaltjes. Het is dus belangrijk dat materialen gescheiden gehouden worden.”
In Duitsland moeten alle auto’s na gebruik weer terug naar de fabrikanten. In Duitsland mag namelijk sinds twee jaar geen kunststof meer verbrand worden. De fabrikanten proberen nu ook steeds meer dezelfde kunststof voor de verschillende auto-onderdelen te gebruiken zodat hergebruik later weer makkelijker wordt.
,,De lak op de kunststof is wat hergebruik betreft minder gunstig, maar toch vaak een noodzakelijk kwaad”, stelt Bosma. ,,Nog afgezien van het feit dat de klant vindt dat de auto mooi van kleur en glans moet zijn, en er dus niet uit moet zien als een tupperware bakje, beschermt lak de kunststof tegen UV-straling en oplosmiddelen zoals benzine. Bovendien zijn lakken harder dan de plastic carrosserie waardoor het geheel beter bestand is tegen krassen.”
Een probleem is echter dat de lak het kunststof sneller doet breken. Dat is een vervelende eigenschap, zeker bij autobotsingen. Bros breken van materiaal biedt de passagiers minder bescherming dan wanneer het materiaal alleen vervormt, ofwel taai deformeert. Het bros breken van materialen, versplinteren, wil de automobielindustrie dus ook zoveelmogelijk proberen te voorkomen.
Dit ‘oppervlakteverbrossingseffect’ is een bekend probleem bij het lakken van kunststof. Ondanks de geringe dikte van de lak (ongeveer 0,05 millimeter) is gelakte kunststof door dit effect zwakker dan ongelakte kunststof. Bosma deed bij Akzo onderzoek naar deze problematiek. ,,Doel was het uitzoeken welke parameters een rol spelen bij de verbrossing van de kunststof en het opstellen van een model dat het breukgedrag van gelakte kunststoffen beschrijft.”
Kerf
Vroeger was de veronderstelling dat de verzwakking van de kunststof altijd veroorzaakt werd door de oplosmiddelen in de lak. Dat blijkt niet altijd het geval. ,,Men heeft namelijk de treksterkte van een stuk kunststof dat gelakt is geweest maar waar de lak weer vanaf geschuurd is, vergeleken met een ongelakt stuk kunststof. Deze bleek gelijk te zijn.” De oplosmiddelen hebben in dit geval dus geen invloed gehad.
De verklaring daarvoor ligt ergens anders. Lak breekt onder invloed van trekspanning eerder dan het kunststof substraat waarop het gehecht zit, omdat lak harder is en dus minder rekbaar is. Als de lak eenmaal gescheurd is dan groeit de scheur vaak door in het substraat. ,,Vergelijk het met een overhemd. Als daar eenmaal een scheurtje in zit, dan trek je hem heel gemakkelijk helemaal kapot”, legt Bosma uit.
Zo ook met de lak. Een scheur in een goed hechtende lak kan als een soort kerf werken. Als de spanningsconcentratie aan de tip van deze kerf erg hoog wordt, zal de scheur door het substraat groeien en een breuk veroorzaken. Een dergelijke kerf in de lak kan bijvoorbeeld ontstaan door trekspanning vanwege vervorming bij een botsing.
Diverse factoren zijn van invloed op het breukgedrag van materialen. Uiteraard speelt de temperatuur een belangrijke rol. ,,Iedereen weet dat een boterhamzakje dat net uit het vriesvak komt sneller breekt dat een zakje bij kamertemperatuur. Dit geldt voor vrijwel alle materialen”, zegt Bosma. Alleen de temperatuur waarbij het materiaal van taai overgaat in bros is voor materialen verschillend. Lak en kunststof zijn bij hoge temperaturen even taai. Dan zal de lak ook geen negatief effect hebben op de oppervlakteverbrossing. ,,Als je dan toch per se een deuk in je auto wil rijden, dan kun je dat maar beter in de Sahara doen.” Maar bij temperaturen van bijvoorbeeld min vijftig is lak veel brosser dan kunststof. Daardoor vormt de lak de zwakke schakel en bezwijkt het geheel eerder.
Testen
Bosma ontwikkelde een aantal testen om deze theorie te onderbouwen, parameters te ontdekken en het proces te kwantificeren. Hij deed trekproeven en ontwikkelde scheurtesten bij verschillende temperaturen en hechtingstesten.
In de trekproeven werden de twee uiteinden van een al dan niet gelakt kunststof staafje in een trekbank geklemd. De staaf werd met hoge snelheid, duizend keer zijn eigen lengte per minuut, uit elkaar getrokken. Daarbij keek hij naar deuitreklengte en de kracht waarbij het materiaal het begaf. Tevens werd tijdens de meting gekeken wanneer de lak kapot ging. Dit werd geregistreerd door de weerstand te meten van een heel dun laagje grafiet dat van tevoren aangebracht was aan de gelakte zijde. Zodra de weerstand oneindig werd, wist Bosma dat het grafiet, en dus de lak, gebroken was.
Bij de scheurtesten keek Bosma met de microscoop naar de scheurranden van de lak bij verschillende temperaturen. Als het materiaal taai deformeert zie je een gladde scheurrand. Bij bros breken een sterk gekartelde scheurrand. Deze overgangstemperatuur is heel scherp en wordt de scheurovergang genoemd. Men streeft ernaar dat die temperatuur voor de lak zo laag mogelijk is en dus zo dicht mogelijk bij de scheurovergang van het kunststof komt.
Met de hechtingstest werd bepaald hoeveel energie er nodig is om een eerste begin van onthechting te veroorzaken. Uit deze meting bleek onder andere dat de mate van hechting van de lak sterk beïnvloed wordt door de voorbehandeling van het kunststof alvorens de lak wordt aangebracht. Schoonmaken met loog en alcohol verbetert de hechting aanzienlijk.
Taaiheid
Bosma concludeerde dat verbrossing afhankelijk is van een aantal factoren zoals de taaiheid van de lak, de hechting van de lak aan het substraat, breukstoppend vermogen van het substraat en de dikte van de lak.
,,Het is allemaal heel logisch”, zegt Bosma. ,,Als de lak taai is en dus niet breekt zal het substraat ook niet bezwijken. Als de lak niet sterk hecht en loslaat van het substraat zodra het onder te grote spanning komt, is er ook geen probleem. De hechting van de lak kan natuurlijk niet oneindig zwak zijn want je wil ook niet dat de lak van de auto waait als je tachtig rijdt. En als het substraat scheuren stopt, in vaktermen minder kerfgevoelig is, zal het niet breken door een kerf in de lak en is er ook niets aan de hand.” Tenslotte geldt, hoe dikker de lak, hoe groter de spanning onder in de kerf aan het grensvlak met de kunststof en dus hoe sneller het substraat bezwijkt. Zo dun mogelijk lakken dus. Deze factoren heeft Bosma kwantitatief in een model verwerkt.
De volgende stap is nu aan de autolakindustrie. Die moet er nu eentje uitzoeken die hard is maar toch taai, of een lak die vrij goed hecht maar die loslaat onder extreme omstandigheden. ,,De meeste gebruikte lakken bestaan uit wel twintig verschillende componenten waarvan niet altijd iedereen precies weet waar sommige componenten voor dienen.” Wie weet komt er nu wel weer een geheimzinnig component bij.
Steeds meer delen van de carrosserie zijn van kunststof
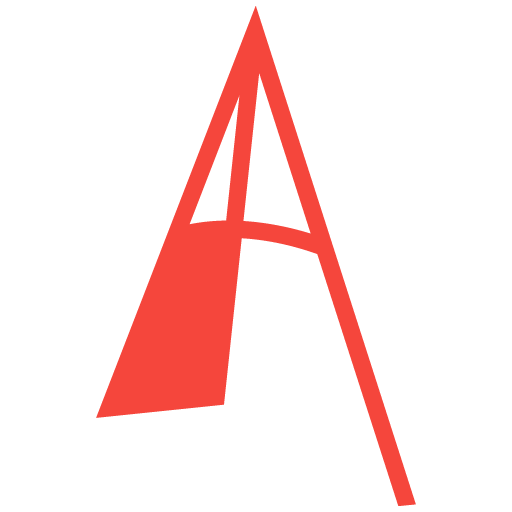
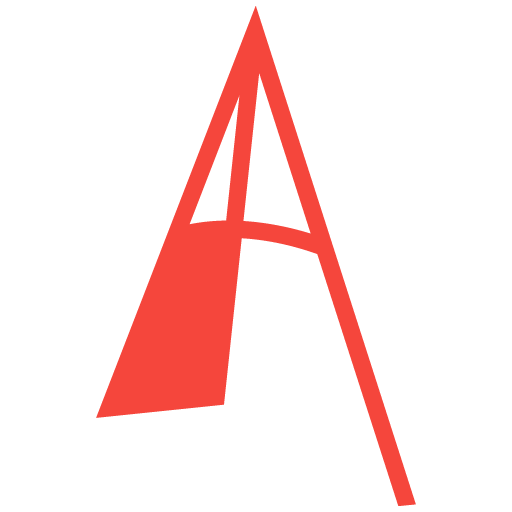
Comments are closed.