On December 3, 1984, the world’s worst chemical industry accident occurred when the Union Carbide Plant in Bhopal, India, exploded, killing 3,800 people and injuring thousands more.
Twenty years on, TU Delft’s Process Intensification group is developing the safety process designs and tools needed to ensure such industrial accidents never occur again.
On the cold wintry night of December 3, 1984, most of Bhopal’s residents had retired to their beds, having no inkling that many of them were doing so for the last time in their lives. At the nearby Union Carbide (India) Limited factory, a deadly chemical reaction had begun, which, at around midnight, culminated in the leakage of deadly Methyl Isocyanate (MIC) gas from one of the factory’s tanks. A cloud of toxic gas gradually descended and enveloped the city in lethal folds and this city of hills and lakes turned into a gas chamber. Bhopal was witnessing the worst ever industrial disaster, as thousands of the city’s residents died painfully from respiratory failure.
While western technology and companies surely benefit the local economies of many developing countries, the Bhopal disaster demonstrated that there can be a deadly downside to this. Since Bhopal, the chemical industry has changed however and institutions like TU are playing key roles in improving industrial safety processes.
Today, sustainability, safety in design, loss prevention, process intensification, and risks & hazards have become key concepts in the industry. Responsible cares, avoiding human errors and good manufacturing practices are also highly emphasized in day-to-day chemical industry operations. While other accidents have occurred since Bhopal, the paradigm shift to safer processes has been prominent.
Dr. Saul Lemkowitz, a TU assistant professor at Delft Chem Tech who teaches ‘Chemical Risk Management’ to graduate students, confirms that “inherently safer design has come a long way since Bhopal. Earlier, there wasn’t much emphasis on safety and the tools like Hazards and Operability Studies (HAZOP), and Fault Tree Analysis (FTA), which allow us to evaluate and find the the cause of accidents, weren’t available. However, the accidents made us take a broad view of this part of an Industry.” Lemkowitz says that today Risk Management is an independent topic of study and is given equal priority, as that of any unit operation, like distillation and reactors.
Dr. Andrzej Stankiewicz of DSM Research teaches Process Intensification at TU Delft. His Process Intensification group is currently working on designing the same plant as at Bhopal, but using Process Intensification (P.I.) tools that contemplate Chemical Risk Management. TU Delft has pioneered the P.I. program and can claim the world’s first batch of chemical engineers with Process Intensification qualifications. Using these P.I. tools, and supervised by Dr. Stankiewicz, they’re now conceptually designing the Bhopal Plant in a safer, more intensified way.
Dr. Stankiewicz says it’s now possible to avoid such accidents in the Process Industry by using these Process Intensification tools. Reducing the size of the chemical industry in techno-economic feasible way is now possible for many hazardous processes. For instance, a Micro-riser Reactor replacing the huge Fluidized Catalytic Cracking reactor in oil refinery is no longer a distant dream and one such project is currently being carried out by Delft Chem Tech’s Reactor & Catalysis Engineering (R&CE) group.
On December 3rd 2004, the world observes the 20th anniversary of the Bhopal disaster. Over the past 20 years, in part thanks to key research conducted by universities like TU Delft, the chemical industry has continued to implement safer and more sustainable approaches, and this development will continue in future. “Safety,” Lemkowitz says, “can no longer be traded off.”
On the cold wintry night of December 3, 1984, most of Bhopal’s residents had retired to their beds, having no inkling that many of them were doing so for the last time in their lives. At the nearby Union Carbide (India) Limited factory, a deadly chemical reaction had begun, which, at around midnight, culminated in the leakage of deadly Methyl Isocyanate (MIC) gas from one of the factory’s tanks. A cloud of toxic gas gradually descended and enveloped the city in lethal folds and this city of hills and lakes turned into a gas chamber. Bhopal was witnessing the worst ever industrial disaster, as thousands of the city’s residents died painfully from respiratory failure.
While western technology and companies surely benefit the local economies of many developing countries, the Bhopal disaster demonstrated that there can be a deadly downside to this. Since Bhopal, the chemical industry has changed however and institutions like TU are playing key roles in improving industrial safety processes.
Today, sustainability, safety in design, loss prevention, process intensification, and risks & hazards have become key concepts in the industry. Responsible cares, avoiding human errors and good manufacturing practices are also highly emphasized in day-to-day chemical industry operations. While other accidents have occurred since Bhopal, the paradigm shift to safer processes has been prominent.
Dr. Saul Lemkowitz, a TU assistant professor at Delft Chem Tech who teaches ‘Chemical Risk Management’ to graduate students, confirms that “inherently safer design has come a long way since Bhopal. Earlier, there wasn’t much emphasis on safety and the tools like Hazards and Operability Studies (HAZOP), and Fault Tree Analysis (FTA), which allow us to evaluate and find the the cause of accidents, weren’t available. However, the accidents made us take a broad view of this part of an Industry.” Lemkowitz says that today Risk Management is an independent topic of study and is given equal priority, as that of any unit operation, like distillation and reactors.
Dr. Andrzej Stankiewicz of DSM Research teaches Process Intensification at TU Delft. His Process Intensification group is currently working on designing the same plant as at Bhopal, but using Process Intensification (P.I.) tools that contemplate Chemical Risk Management. TU Delft has pioneered the P.I. program and can claim the world’s first batch of chemical engineers with Process Intensification qualifications. Using these P.I. tools, and supervised by Dr. Stankiewicz, they’re now conceptually designing the Bhopal Plant in a safer, more intensified way.
Dr. Stankiewicz says it’s now possible to avoid such accidents in the Process Industry by using these Process Intensification tools. Reducing the size of the chemical industry in techno-economic feasible way is now possible for many hazardous processes. For instance, a Micro-riser Reactor replacing the huge Fluidized Catalytic Cracking reactor in oil refinery is no longer a distant dream and one such project is currently being carried out by Delft Chem Tech’s Reactor & Catalysis Engineering (R&CE) group.
On December 3rd 2004, the world observes the 20th anniversary of the Bhopal disaster. Over the past 20 years, in part thanks to key research conducted by universities like TU Delft, the chemical industry has continued to implement safer and more sustainable approaches, and this development will continue in future. “Safety,” Lemkowitz says, “can no longer be traded off.”
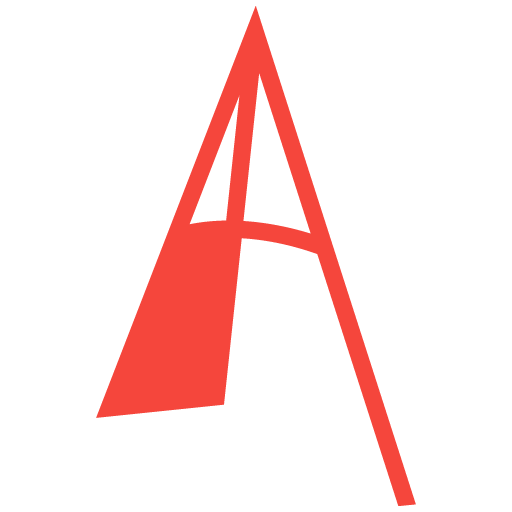
Comments are closed.