Some 130 aerospace engineering master students have been working on building an aircraft since 2017. They do this during the hands-on course Aircraft Manufacturing Lab, a hands-on course where you learn to be consistent and to never cover up mistakes.
Gabriel Sa and Nicolas Pantelias take care of the PR, Matan Neumark is the team manager for team 13 of the Aircraft Manufacturing Lab. (Photo: Thijs van Reeuwijk)
Sloppy work can make panels fall off an airplane in mid-flight, as the incident with a Boeing 737 showed last January. During the Aircraft Manufacturing Laboratory (AML) course, students build a real aircraft from a home-built kit from manufacturer Van’s Aircraft. This is how they learn to work responsibly, to strictly follow the assembly manual, and to contact the aircraft kit manufacturer, if questions arise. Students are required to make their own riveted aluminium toolbox before they’re even allowed to approach the airplane.
Joris Melkert, who teaches the course together with his colleague John-Alan Pascoe, knows the value of hands-on experience from his own time as a student. Between 1989 and 1995, he and other TU Delft students built a Lambach HL II biplane from a manual. It was a precursor to today’s Dream Teams, Melkert explains.
As in the Dream Teams, aircraft manufacturing requires taking responsibility, quality control, project management, safety management, keeping control over the inventory and being open about mistakes or incidents that have taken place, instead of covering them up.
“I see that over the coming decades many thousands of aircraft will be commissioned,” says Melkert. “So, I think that a fair share of our students will be working in the supervision of aircraft construction. The AML course is the perfect preparation.
According to Joris Melkert: ‘Until 2040, we expect to have to build some 30-40,000 passenger planes. More than 1,000 planes a year are already being built and that rate will only increase.’






Since the beginning in February 2017, 13 teams have worked in the Aircraft Manufacturing Lab thus far. The current team is working on section 35 of 54 from the construction manual. They’re emptying the sixth crate. The seventh crate contains the engine. At the current pace of nearly three sections per semester, the aircraft manufacturing lab may take another two to three years.
Melkert isn’t really interested in the completion of the kit. “When it’s finished, we’ll probably fly it around for a bit and then we’ll sell it off to finance a new kit.” Evidently, it’s the manufacturing that counts, rather than the aircraft itself.
- Read more on the website of the Aircraft Manufacturing Laboratory
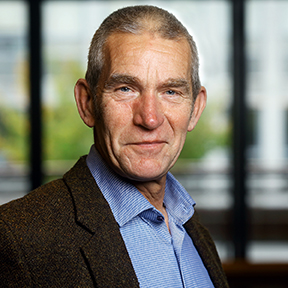
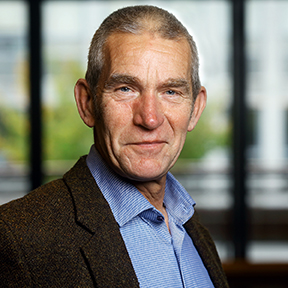
Do you have a question or comment about this article?
j.w.wassink@tudelft.nl
Comments are closed.