Cars today are mainly made of steel. Aluminium is a lighter and better option. Problem is, aluminium cars wear out too quickly. A special new coating for aluminium can prevent this.
/strong>
A large mark underscores the date of his graduation. “Less than one month!” Iulan Apachitei exclaims, looking as he just found out the date today. “Sure I’m a bit nervous. It’s natural and I suppose I need it. Today’s an extra hectic day because I have to go to the printer to print my thesis.”
During his PhD research, Iulian Apachitei produced and characterised special composite coatings on aluminium substrates. These coatings provide hardness, and wear- and corrosion-resistance for aluminium components used in the electronics, automotive, aerospace, and aircraft industries. “Modern technologies are increasingly interested in using light materials to producing lightweight constructions. Among the lighter metals, aluminium and its alloys are used extensively. By 2005, the amount of aluminium used in cars will have doubled compared to 1995.”
Aluminium and its alloys have a low specific density (three times less than steel), good strength, ductility, thermal and electrical conductivity, and are easy to shape and recycle. But despite this excellent combination of properties, aluminium-based alloys have poor surface properties. “Without a proper surface modification or coating, they cannot meet the requirements for durability and functionality when used in applications where they are exposed to wear, corrosion and friction.”
The coatings Apachitei synthesized consists of a matrix that contains nickel phosphorus. In this matrix, there are tiny (1-10 micrometers) embedded ceramic particles that determine the coatings morphology and certain properties. “Uniquely, my coating can cover every part of the product that must be coated. Like a cup which is thrown in a bucket of paint.”
Plans
The principle behind the coating process is fairly straightforward: The coating precipitates automatically on aluminium, owing to the chemical reduction of nickel ions on the pre-activated aluminium surface. When particles are finally added to the solution, however, the deposition mechanism becomes rather complex.
The process Apachitei uses saves energy. “Our coatings are produced close to ‘room temperature’ or eighty degrees, compared to most other processes, which are produced at temperatures of five hundred degrees or more. However, at these high temperatures, aluminium substrates become soft or can even melt.”
Apachitei and his colleagues at the Forming, Coatings & Powder Technology group developed the set up for the coating synthesis.
Industry has already shown interest in the method of coatings Apachitei uses. “Our group is thinking of patenting this process, but it will take a long time. As a PhD I can’t wait for that; I want to publish my findings.”
Apachitei can’t say what really fascinates him about this field of study, nor, for that matter, is he willing to say much at all about himself. “I didn’t really choose for this kind of research. Igot more and more interested as I worked in this area because there is so much to explore in the area of nanostructured and nanocomposite coatings,” he says, grudgingly.
The researcher is full of plans for after he receives his PhD. “The particles we use now are about one to ten micrometers big. I’d like to synthesize particles in coatings that are between one and a hundred nanometers. The coatings now are relatively rough. The smaller the particles the smoother the coating.”
Apachitei will defend his thesis on December 7th, at 10.30 am.
Cars today are mainly made of steel. Aluminium is a lighter and better option. Problem is, aluminium cars wear out too quickly. A special new coating for aluminium can prevent this.
A large mark underscores the date of his graduation. “Less than one month!” Iulan Apachitei exclaims, looking as he just found out the date today. “Sure I’m a bit nervous. It’s natural and I suppose I need it. Today’s an extra hectic day because I have to go to the printer to print my thesis.”
During his PhD research, Iulian Apachitei produced and characterised special composite coatings on aluminium substrates. These coatings provide hardness, and wear- and corrosion-resistance for aluminium components used in the electronics, automotive, aerospace, and aircraft industries. “Modern technologies are increasingly interested in using light materials to producing lightweight constructions. Among the lighter metals, aluminium and its alloys are used extensively. By 2005, the amount of aluminium used in cars will have doubled compared to 1995.”
Aluminium and its alloys have a low specific density (three times less than steel), good strength, ductility, thermal and electrical conductivity, and are easy to shape and recycle. But despite this excellent combination of properties, aluminium-based alloys have poor surface properties. “Without a proper surface modification or coating, they cannot meet the requirements for durability and functionality when used in applications where they are exposed to wear, corrosion and friction.”
The coatings Apachitei synthesized consists of a matrix that contains nickel phosphorus. In this matrix, there are tiny (1-10 micrometers) embedded ceramic particles that determine the coatings morphology and certain properties. “Uniquely, my coating can cover every part of the product that must be coated. Like a cup which is thrown in a bucket of paint.”
Plans
The principle behind the coating process is fairly straightforward: The coating precipitates automatically on aluminium, owing to the chemical reduction of nickel ions on the pre-activated aluminium surface. When particles are finally added to the solution, however, the deposition mechanism becomes rather complex.
The process Apachitei uses saves energy. “Our coatings are produced close to ‘room temperature’ or eighty degrees, compared to most other processes, which are produced at temperatures of five hundred degrees or more. However, at these high temperatures, aluminium substrates become soft or can even melt.”
Apachitei and his colleagues at the Forming, Coatings & Powder Technology group developed the set up for the coating synthesis.
Industry has already shown interest in the method of coatings Apachitei uses. “Our group is thinking of patenting this process, but it will take a long time. As a PhD I can’t wait for that; I want to publish my findings.”
Apachitei can’t say what really fascinates him about this field of study, nor, for that matter, is he willing to say much at all about himself. “I didn’t really choose for this kind of research. Igot more and more interested as I worked in this area because there is so much to explore in the area of nanostructured and nanocomposite coatings,” he says, grudgingly.
The researcher is full of plans for after he receives his PhD. “The particles we use now are about one to ten micrometers big. I’d like to synthesize particles in coatings that are between one and a hundred nanometers. The coatings now are relatively rough. The smaller the particles the smoother the coating.”
Apachitei will defend his thesis on December 7th, at 10.30 am.
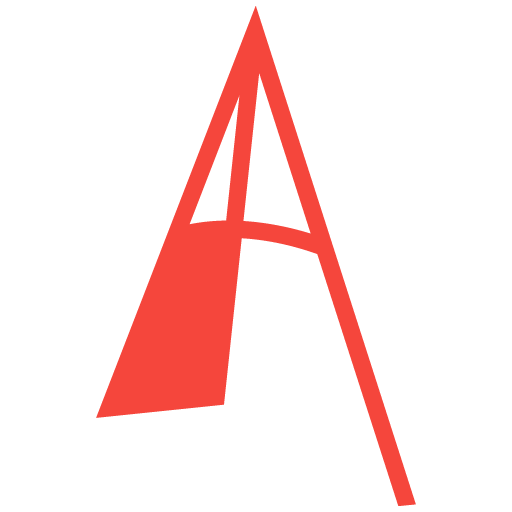
Comments are closed.