Project groups of first-year mechanical engineering students were given 10 minutes to stack 25 crates using a machine they designed themselves. But in the finals, everyone finished much sooner.
Team WB109 stacked 25 crates in 3 minutes 47 and took second place. (Photo: Thijs van Reeuwijk)
Every year it is the same and yet every year it is different: the annual design competition for first-year Mechanical Engineering students (Faculty of Mechanical Engineering, ME). This year, the task for the more than 100 groups of up to six students was to create a mechanical crate stacker. The machine was to make the highest possible stack of empty crates (20 by 30 centimetres and 12 centimetres high, weight 400 grams) within 10 minutes by continuously adding a crate to the bottom of the stack and lifting the rest. What was special this time was that students had been handed two different electric motors to experiment with right at the beginning of the design project.
On Wednesday 12 June, students demonstrated the machines they had been working on for the past five months on the lawn behind the ME building.
At the beginning of the track, crates are lined up neatly behind each other in rows. The stacker picks one up, moves to the next one and puts the stack on top of the next one. The machine repeats this and the tower of empty crates gets ever higher and heavier. Only the bottom four crates may be touched. There is a rail on either side of the row of crates to help the stacker.
The organisers gave the groups 10 minutes for the task and were surprised to see that all eight finalists managed to produce a three metre high stack of 25 crates well within that time. The winner, team WB061 took just 2:25 minutes to finish. Second was team WB109 at 03:47 minutes, and third was WB004 at 04:09 minutes. They were awarded their prizes by René Delfos, the Education Director.
Besides the competition winners, there were four jury prizes.
- The 3D-CAD Award for team WB109 for the most ingenious 3D computer model (from Visiative, Walter Poot).
- On the suggestion of jury chairman Anton van Beek, the Green Award for the most sustainable design went to WB093.
- The Science Centre Award for the design with the most visible technology, in the eyes of Michael van der Meer and Thomas van Zeijl, went to team WB024.
- The Constructor’s Award by Maarten Hooftman (Huisman Equipment) was given to team WB103 for the ‘most technically innovative design’.








The design process is getting better and better every year, notes lecturer Dr Regine Vroom. The 100+ first-year teams are assigned five manufacturing points in time with access to the workshop. By reminding students that they must have a working prototype after the third workshop visit, the groups have the time to test extensively, leaving one to two sessions for improvements. This generally worked well, says Vroom who was impressed by the ‘steep learning curve’ that students went through in their first year.
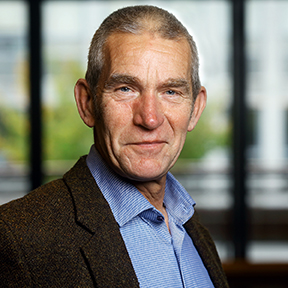
Do you have a question or comment about this article?
j.w.wassink@tudelft.nl
Comments are closed.