The new multiphase flow tunnel is a unique research facility in Europe, says Dr Cornel Thill. So what is so special about the device – apart from its appearance?
Dr Cornell Thill at the observation window of the new multiphase flow tunnel behind the 3mE building. (Photos: Jos Wassink)
Flow researcher Dr-Ing Cornel Thill (Faculty of Mechanical Engineering, Maritime Engineering and Materials Science) makes a flying start on the guided tour. The tunnel is made of super duplex stainless steel, he says, which makes it resistant to salt water. This is important because air bubbles, which are the subject of much research, behave differently in fresh water than in salt water.
Furthermore, the construction, with its many external ribs and thick steel plates, is exceptionally strong which allows it to work both at negative pressure and at two bar overpressure, and to limit the deformation to a 0.4% maximum. Thill does not know of a comparable facility in the world.
Powerful machine
There are numerous details that Thill is happy and proud to elaborate on. He mentions the special 110 kilowatt pump in the basement that manufacturer VOITH managed to make very quiet with modified rotor blades. The pump is followed by a wide flat box through which the water flows slowly (about 1 m/s max.) to capture all the air bubbles before flowing past the test piece in the glass section at a speed of up to 13 metres per second. The total capacity of the flow tunnel is 17,500 litres.
The entire structure takes up three floors of the 3mE building and is housed in the same wing as the drag tank (where ship models are measured). The initiative came from research leader Prof. Tom van Terwisga (TU Delft Faculty of 3mE and MARIN) who worked together with flow experts Prof. Jerry Westerweel and Prof. Christian Poelma on both the design and the means for realisation. The first design dates back to 2017 and was created by PhD student Swaraj Nanda. That design was updated by Cornel Thill with flow experts from TU Delft and Marin. In addition to five years, the tunnel cost about EUR 1.5 million, in which TU Delft itself invested half and research funder NWO the other half.
The heavy execution in extreme stainless steel resulted from two types of research that will take place here: cavitation and air lubrication.
Part of a bronze ship’s propeller gnawed by cavitation. The surface was originally completely smooth and shiny.
Damage to the propelleri
Cavitation research often involves negative pressure. If the local pressure is low enough, even cold water will start to ‘boil’. The formation of vapour bubbles (‘boiling’) under water on a ship’s propeller is known as cavitation. This occurs more quickly at low pressure, which simplifies the research.
In practice, cavitation can cause considerable damage to ships’ propellers and hulls because a great deal of energy is released locally when vapour bubbles implode. Besides it’s the cause for lots of underwater noise.
“For efficient propulsion, it is important to find a balance between maximum efficiency and acceptable cavitation on the propeller,” says Van Terwisga. “The tricky thing is that these two goals conflict with each other in the design. So, vibration nuisance, radiated noise, and damage to the propeller must be reduced to acceptable levels.”
The occurrence of cavitation and potential preventive measures can be researched here realistically in salty water. “Air bubbles are smaller in salty water,” explains Thill. “This is why foaming seawater looks whiter than freshwater, which remains transparent for longer because of larger bubbles.”
A slide of bubbles
The other branch of research is using layers of bubbles to reduce friction. There are known situations where a layer of bubbles reduced the propulsion energy by about 15%. This includes the energy needed for generating the bubbles. “We want to better understand that friction reduction,” says Thill.
To that end, a ceiling has been installed in the tunnel. Force transducers measure the friction of the water flowing past, and an air supply release set amounts of bubbles to the ceiling. This allows the promising phenomenon to be systematically studied in salt and fresh water. The pressure in the entire tunnel can be increased to up to two bars for realistic measurements at a depth of 20 metres.
The technicians will continue to work on fine-tuning the control systems in the coming period, but by the end of the calendar year, Thill and his team expect the tunnel to be usable for research and lab courses in the fields of cavitation and air lubrication – two important topics for shipping.
A scale model shows the hidden part of the tunnel with the pump two floors below.
The 110 kW whispering pump is located in the steel box above the composite U-bend.
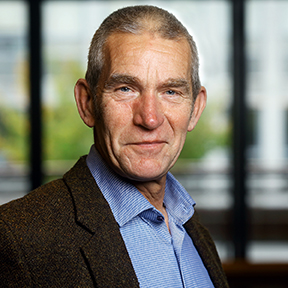
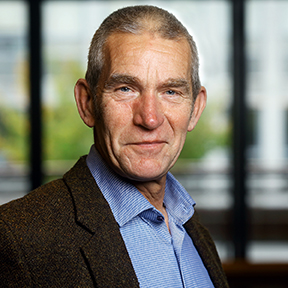
Do you have a question or comment about this article?
j.w.wassink@tudelft.nl
Comments are closed.