Together with his supervisors, Adi Hascaryantono developed a new method for examining the growth of cracks in aluminium alloy in a corrosive environment, such as seawater.
His research may make aircraft safer.
Cracks in aluminium alloy structures increase over time. In normal air, this process has been thoroughly studied; however, in corrosive environments, such as seawater, the phenomenon is not wholly understood.
The conventional method of studying crack growth rates uses a hydraulic machine which pulls and pushes both sides of a metal sheet, changing with frequencies up to 10 hertz to simulate the changes in a load on, for example, a ship. The effect of a load on a particular aluminium structure over several years can be simulated in one week. However, by using these high frequencies, the hydrogen in the seawater, which is element that corrodes aluminium, is unable to properly interact with the aluminium, because the hydrogen is continuously pushed and pulled out and into the crack. For this reason, the frequency of load changes must be decreased to 0.1 hertz.
Using this frequency, however, would have resulted in problems for Hascaryantono, a MSc student from Indonesia: “I developed a quicker method because my project had to be finished in six months. With the conventional method, it would’ve taken almost two months to do one experiment. The new method performs the same experiment in one week.”
In his new method, Hascaryantono keeps the frequency low; but during the experiment, he increases the load from about 25 kN to 80 kN. To validate his method, Hascaryantono compared the new and the old method in air, which resulted in his discovery of how many cycles with an increasing load are needed to give the same effect as the conventional method. Hascaryantono is currently determining the crack growth rates in seawater.
Afraid
His new method will be presented in Spain, in September, by his supervisor. Hascaryantono will be back in Indonesia by then, returning to the aircraft company he worked for before coming to Delft. “I want to see what my position is over there. There’s been a reorganisation during my absence and I don’t even know what division I’m in. I hope there’s still a job for me.”
He had joined the company as a research engineer, working on methods to optimise products, which also involved using methods for predicting crack growth. “I used methods without really understanding why they worked. I like being an engineer, but it’s good that I now know more about the fundamental aspects.”
He was interested in the crack growth in a corrosive environment, because the lifetime of an aircraft is shorter when they regularly fly over the sea. “Therefore we have a problem with corrosion with our aircraft,” Hascaryantono says. “It can be dangerous if cracks become larger faster than we predicted, because of humidity from the sea. Aircraft always fly with small cracks in their bodies, as thin as a hair. But when a crack becomes too large, the component must be replaced to guarantee safety. This is checked on a regular basis. However, it would be ideal to be able to predict the crack growth better.”
Perhaps not surprisingly, Hascaryantono doesn’t like flying: “Knowing about the cracks makes me a bit afraid. Although I know the cracks are checked regularly and therefore flying is safe, I don’t fly unless it’s absolutely necessary.”
Together with his supervisors, Adi Hascaryantono developed a new method for examining the growth of cracks in aluminium alloy in a corrosive environment, such as seawater. His research may make aircraft safer.
Cracks in aluminium alloy structures increase over time. In normal air, this process has been thoroughly studied; however, in corrosive environments, such as seawater, the phenomenon is not wholly understood.
The conventional method of studying crack growth rates uses a hydraulic machine which pulls and pushes both sides of a metal sheet, changing with frequencies up to 10 hertz to simulate the changes in a load on, for example, a ship. The effect of a load on a particular aluminium structure over several years can be simulated in one week. However, by using these high frequencies, the hydrogen in the seawater, which is element that corrodes aluminium, is unable to properly interact with the aluminium, because the hydrogen is continuously pushed and pulled out and into the crack. For this reason, the frequency of load changes must be decreased to 0.1 hertz.
Using this frequency, however, would have resulted in problems for Hascaryantono, a MSc student from Indonesia: “I developed a quicker method because my project had to be finished in six months. With the conventional method, it would’ve taken almost two months to do one experiment. The new method performs the same experiment in one week.”
In his new method, Hascaryantono keeps the frequency low; but during the experiment, he increases the load from about 25 kN to 80 kN. To validate his method, Hascaryantono compared the new and the old method in air, which resulted in his discovery of how many cycles with an increasing load are needed to give the same effect as the conventional method. Hascaryantono is currently determining the crack growth rates in seawater.
Afraid
His new method will be presented in Spain, in September, by his supervisor. Hascaryantono will be back in Indonesia by then, returning to the aircraft company he worked for before coming to Delft. “I want to see what my position is over there. There’s been a reorganisation during my absence and I don’t even know what division I’m in. I hope there’s still a job for me.”
He had joined the company as a research engineer, working on methods to optimise products, which also involved using methods for predicting crack growth. “I used methods without really understanding why they worked. I like being an engineer, but it’s good that I now know more about the fundamental aspects.”
He was interested in the crack growth in a corrosive environment, because the lifetime of an aircraft is shorter when they regularly fly over the sea. “Therefore we have a problem with corrosion with our aircraft,” Hascaryantono says. “It can be dangerous if cracks become larger faster than we predicted, because of humidity from the sea. Aircraft always fly with small cracks in their bodies, as thin as a hair. But when a crack becomes too large, the component must be replaced to guarantee safety. This is checked on a regular basis. However, it would be ideal to be able to predict the crack growth better.”
Perhaps not surprisingly, Hascaryantono doesn’t like flying: “Knowing about the cracks makes me a bit afraid. Although I know the cracks are checked regularly and therefore flying is safe, I don’t fly unless it’s absolutely necessary.”
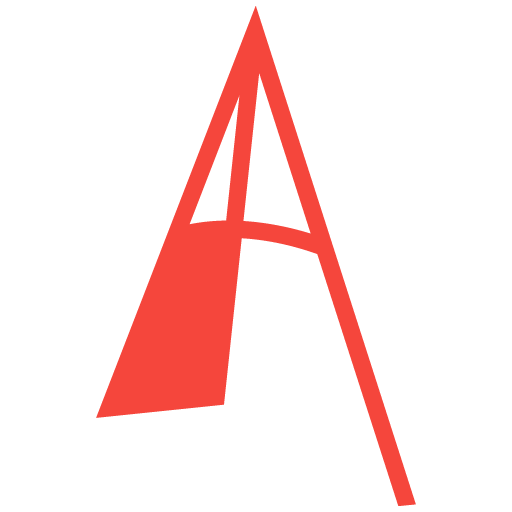
Comments are closed.