PV panels at the French processing plant Galloo Halluin near Kortrijk (Photo: Laurent Julliand).
Solar panels are becoming increasingly important in electricity production. But what happens to them when they reach the end of their life? We’re at the start of a massive waste stream, set to grow to 60 million tonnes globally by 2050. Researchers at CEG and EEMCS are working hard on solutions.
This article in 1 minute
- From a disadvantaged position, the Netherlands has risen to become a solar energy leader within Europe.
- That means 40 trucks of discarded solar panels every day by 2070.
- Recycling of solar panels is in bad shape because nobody thought about it at the time.
- The market is too small for specialised recycling companies, but that is starting to change.
- A European university-industry programme aims to recover metals from waste.
- TU Delft is an active research partner.
- Recycling solar panels will not succeed without additional funding, TNO calculated
The first solar panels made with recycling in mind are now coming onto the market.
Starting from a disadvantaged position, the Netherlands has risen to become a leader in solar energy in Europe. On average, there are more than three solar panels per person installed on rooftops or in fields across the country.
The first solar panels from the 21st century, with lifespans of 25 to 30 years, are now ending up in landfills, and this waste stream is growing rapidly, mirroring the installed capacity from those same years.
By 2070, the Netherlands will discard 40 lorry loads of solar panels every day
A recent study by the Faculty of Electrical Engineering, Mathematics and Computer Science (EEMCS) calculates that by 2030, the Netherlands will generate 40,000 tonnes of discarded solar panels per year, rising to 120,000 tonnes by 2050 and 200,000 tonnes by 2070. That’s 14,000 lorries carrying 14 tonnes of PV waste, or 40 lorries every day.
In about 2010, Dr Malte Vogt (EEMCS), who supervised the study, initially focused on simulating solar cell processes as part of his physics studies at Leibniz University Hannover. A growing sense of social urgency led him to work on material circularity in sustainable energy.
Vogt expects solar energy to account for one to two-thirds of global energy by 2050. Vogt is unsurprised by the International Energy Agency’s (IEA) projection of just 35%. “Solar energy has been underestimated for 50 years.” However, this explosive growth comes with a delay of 25-30 years before a massive waste problem surfaces, for which there are no clear solutions.
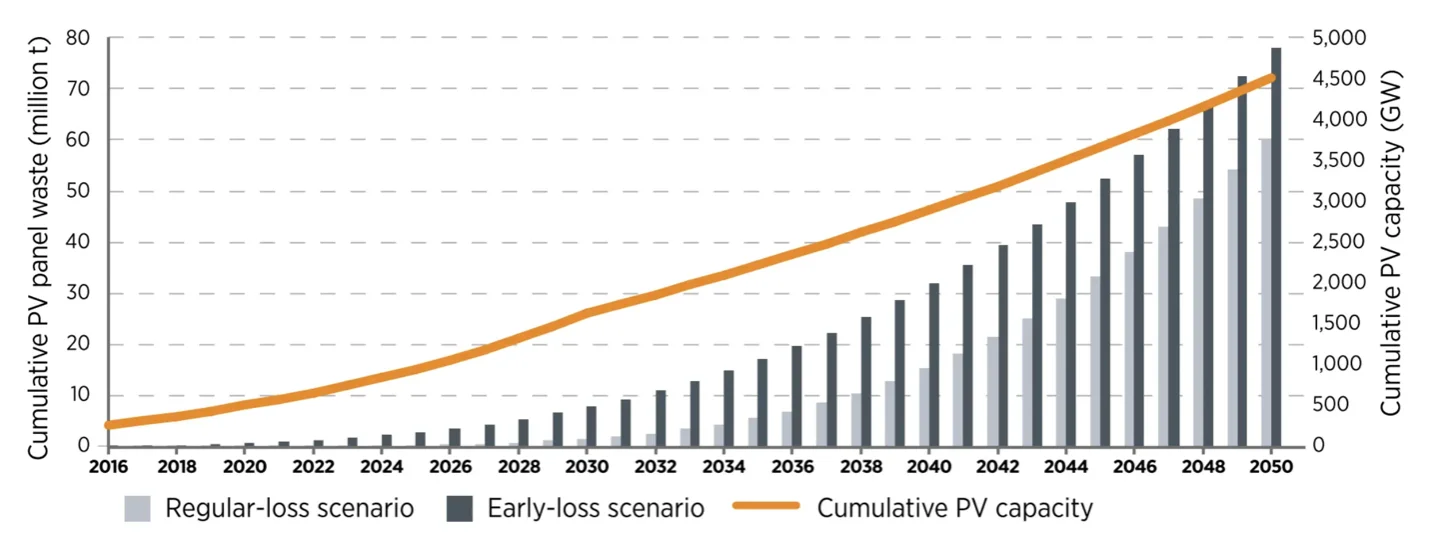
It’s a chicken-and-egg problem. With only a small number of panels currently being discarded, few waste facilities are able to process the undocumented mix of glass, plastic, aluminium, and silicon in PV (photovoltaic) panels. As a result, 90% of discarded or defective panels worldwide end up in landfills, wasting valuable resources. How can this be improved?
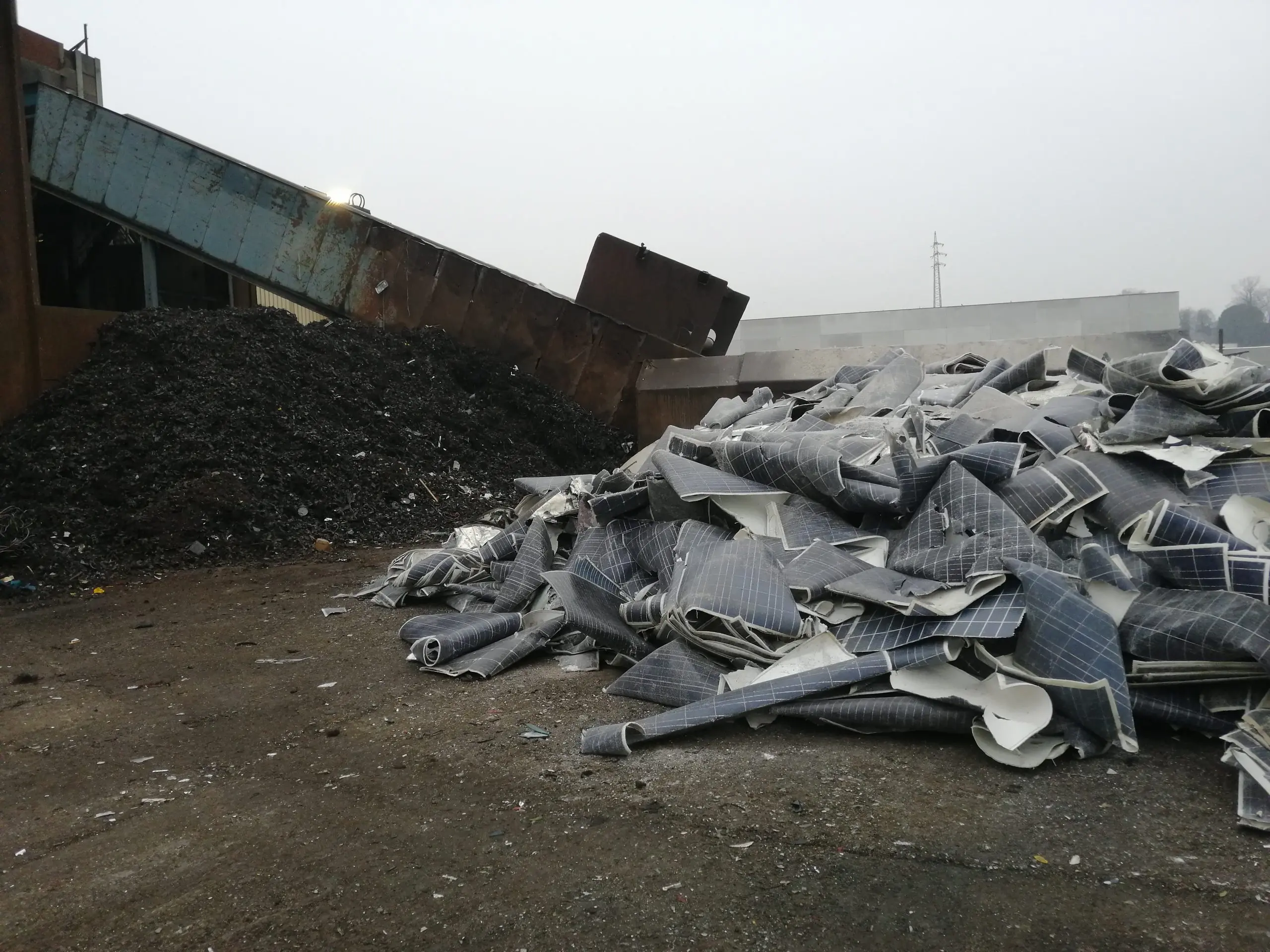
Europe’s Approach
The European Union (EU) classifies solar panels as large electrical waste under the WEEE (Waste Electrical and Electronic Equipment) Directive. This legislation aims to collect increasing amounts of electronic waste, as it contains valuable raw materials that are scarce in Europe. Since 2018, 85% of all PV waste is supposed to have been collected, with 80% being recycled. However, this target has only been met in half the member states.
Europe’s first PV recycling factories are ramping up
The first recycling facilities are now opening in Europe. In 2017, ROSI (Return of Silicon) opened a plant in Grenoble, France, which, according to the BBC, can recover not just aluminium but also copper and silver from PV panels. Another plant (in German) is set to open in Germany next year. In addition, Reiling, a waste processor near Münster, Germany, has begun handling solar panel recycling.
While the recycling of solar panels has significant potential as a growth market, the mixed materials used in their production require a range of technologies for effective recycling.
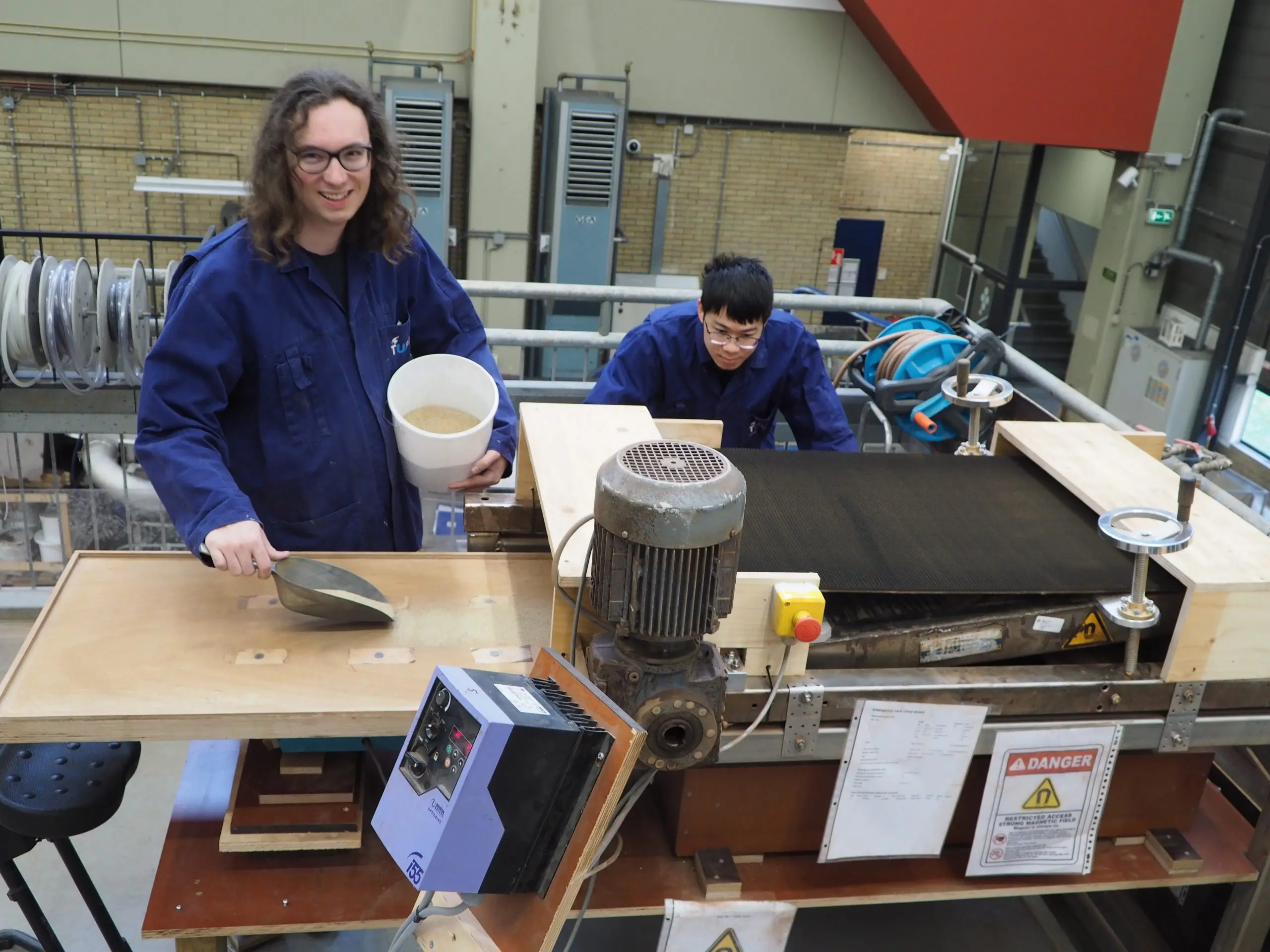
Technology Development
In 2021, a European research programme called Peacoc was launched to develop efficient methods for recovering silver and other precious metals. This programme, which brings together universities and industry, officially runs until April 2025, with a possible extension to 2026.
Dr Francesco Di Maio’s Resources & Recycling group at the Faculty of Civil Engineering and Geosciences is one of Peacoc’s research partners. At the Stevin Hall lab, researchers, including Max van Beek and Dr Hongli Su, grind up solar panels. While the aluminium frames are easy to separate, most components are glued together. Crushing the panels allows the materials to be separated. Under the microscope, grains of copper, iron, and silver can be seen, with silver being a key focus given its high price and looming shortages.
Media error: Format(s) not supported or source(s) not found
Bestand downloaden: https://delta.tudelft.nl/wp-content/uploads/2024/12/VID_20240716_132736.mp4?_=1Technician Ron Penners in the Stevin lab TU Delft sifts PV grind to different sizes. The finest grind contains the most metal. (Video: Max van Beek)
The research aims to use separation techniques based on size, density, and magnetism to increase the silver content. Once the concentration reaches around 10%, recovering the silver becomes economically viable. A range of machines in the lab shake, spin, and blow the crushed material to separate it into different parts.
“You can see the difference in colour,” says Van Beek, pointing to several buckets. “This is medium-coarse material, between 0.2 and 1 millimetre. The lighter material is sand-coloured, while the heavier material is grey due to the metal content.” The grey granules are the most interesting for recovery, and an industrial partner in the research programme will extract the metals.



Economic Feasibility
The viability of a PV recycling industry depends on balancing the costs of material recovery with the revenues from reclaimed materials. TNO researcher Martin Späth published a report on this in late 2022, outlining two recycling approaches.
Downcycling: Only the aluminium frame and copper cables are recovered, with the rest crushed into filler material. This method is low cost but generates low returns.
Solar panel recycling requires financial support
Advanced upcycling: This involves recovering nearly all the materials, including valuable metals. However, this technology is still under development, and the costs far exceed the value of the recovered materials. Späth suggests introducing a disposal fee, similar to that for electronics, to fund the development and construction of recycling technologies. Without this, downcycling would remain the only option and valuable materials would continue to be lost.
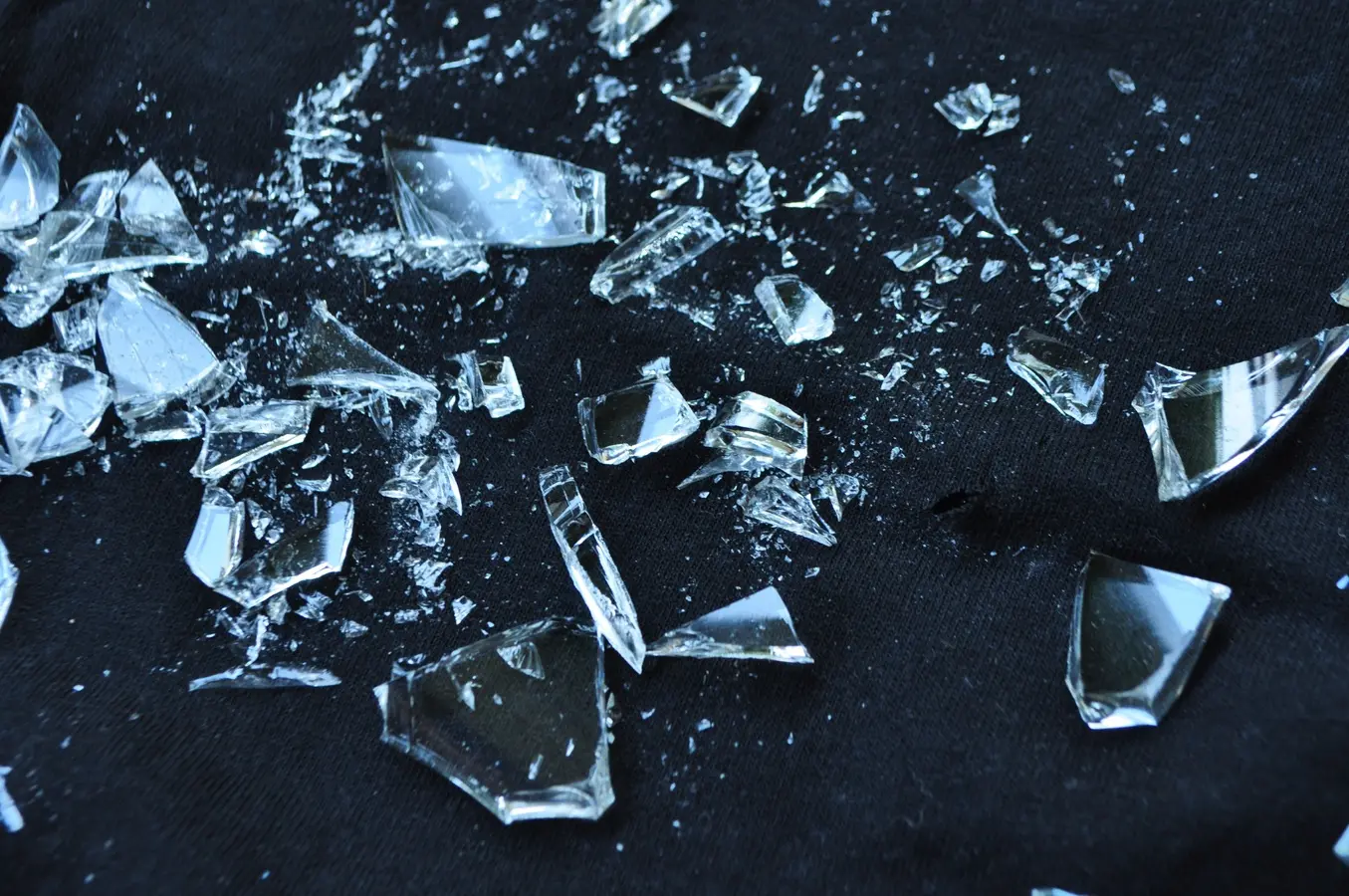
Glass with a problem
Most of the crushed material from solar panels – about 65% to 95% – is glass. However, this glass is often not recyclable.
Many solar panels contain antimony (Sb) to improve light transmission, but this element is banned in European glass production because of its toxicity. Even small amounts can disrupt production processes, making solar panel glass undesirable for recycling. Currently, its only use is as filler material.
Designed for Recycling
Some manufacturers are designing panels with recycling in mind. For example, Lithuania’s Solitek partners with Germany’s Lux Chemtech to produce fully recyclable panels.
In the Netherlands, Solarge claims to produce fully circular panels using thermoplastics, which can be melted and separated at relatively low temperatures. Meanwhile, Rotterdam-based Biosphere Solar avoids adhesives entirely, using a vacuum between two glass sheets. A prototype has been installed at The Green Village, and panels that can be disassembled will be available next year. Biosphere Solar is one of seven partners in the Fair-PV project run by the Amsterdam Institute for Advanced Metropolitan Solutions.
Dr Malte Vogt views these developments as a moral responsibility. “Solar energy has become the cheapest form of electricity thanks to decades of technological progress. It should at least be used sustainably.”
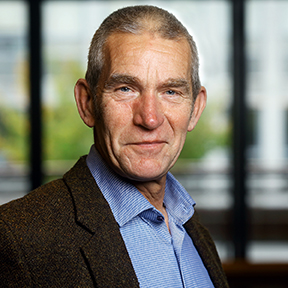
Do you have a question or comment about this article?
j.w.wassink@tudelft.nl
Comments are closed.