Tata Steel in IJmuiden is under pressure to produce steel more cleanly and sustainably, but how? Delta spoke to experts from TU Delft and outlines the options.
The HIsarna pilot plant on the Tata site explores the future of steel production with lower CO2 emissions. (Photo: Tata Steel, John de Koning)
Patience was running out at the beginning of September. Residents of Wijk aan Zee and Beverwijk had long been fed up with the soot specks on their washed sheets, but the National Institute of Public Health and the Environment (RIVM) report (in Dutch) on harmful substances in the environment was the proverbial last straw. It said ‘In Wijk aan Zee, Beverwijk, Velsen-Noord and IJmuiden, outdoor levels of PAH (polycyclic aromatic hydrocarbons) and metals are higher than at locations outside the IJmond region. They are highest in Wijk aan Zee. There, quantities of some metals such as iron, manganese, vanadium and chromium, as well as PAH, have been measured that are 20 to 100 times higher’. The RIVM is particularly concerned about lead particles that children ingest through street dust. ‘The exposure to the quantities of lead and PAH in dust that has settled is undesirable for the health of children.’
In response, the NRC newspaper headlined that the right of the steel plant to exist had now become a political issue. It added that with annual emissions of 12 million tonnes of CO2, Tata Steel was responsible for 7% of the Netherlands’ greenhouse gas emissions. But because of the enormous number of jobs (9,000), nobody is arguing for closure. So, the question is: can steel production be done better, cleaner and greener?
You can’t just convert an existing factory
TNO and the Netherlands Environmental Assessment Agency (PBL) answered that question in the affirmative in a 2019 report with no fewer than nine options for Tata to go green. The authors also point out that the steel plant, which has been there since 1918, has made a lot of progress in the last 30 years in reducing waste flows and in making the production process more energy efficient (32%). In 2010, the HIsarna pilot plant, which aimed to reduce CO2 emissions in the production of liquid iron from coal and iron ore by 20%, was built on the Tata site. But according to Professor of Energy Dr Kornelis Blok (Faculty of Technology, Policy and Management), the HIsarna pilot plant is not a harbinger for development in IJmuiden. “The HIsarna process requires a whole new factory. You can’t just convert an existing factory”, he explains. Blok expects a new modern factory like this to be built in India, the company’s motherland, which has more growth potential.
1. Over on natural gas
Tata Steel announced its own choice last week (in Dutch). It would be stopping the use of coal and switch to natural gas instead and later to hydrogen. The technology for this gas-based process is already available. It is based on the conversion of natural gas into hydrogen and carbon monoxide. This gas mixture (syngas) reduces iron ore to iron. The flue gas consists of almost pure carbon dioxide. This makes it easy to concentrate it for underground storage. Tata announced that within eight years one of the current three blast furnaces will be replaced by a natural gas installation. The CO2 reduction of this operation will be 3.9 million tonnes by 2030. That would amount to 1/3 of Tata’s total emissions of 12 tonnes per year.
2. CO2 capture and storage
Professor Blok would recommend the Tata factory carbon dioxide capture from the flue gases as the most cost-effective option. This can be fitted to the existing structures as an end-of-pipe solution. Capture with gas scrubbers costs about EUR 100 per ton of CO2, plus EUR 10-20 per ton for storage in an empty gas field under the North Sea. The flue gases will have to be cleaned first, which may reduce the emission of PAHs and metals into the environment. Carbon dioxide capture would reduce annual emissions by five million tonnes, and could also be implemented earlier than the replacement of one of the blast furnaces.
‘We have to leave coal behind’
Blok thinks natural gas as an alternative energy source in unfit because its price (in euros per joule), which is currently three to five times higher than coal. “Natural gas is very expensive for several reasons. The winter gas stocks are not full and that is making people nervous. On top of that, demand is rising as coal-fired power plants are being closed and gas-fired plants are taking over.”
3. Blue hydrogen
“We have to leave coal behind,” says Prof Andrea Ramirez, Professor of Low Carbon Systems & Technologies (also at TPM). “Flue gases from the chimney only contain 15% CO2. That low concentration makes it expensive and cumbersome to filter out the CO2.” She would therefore prefer a process that produces no CO2 at all: iron production with hydrogen or Direct Reduction Hydrogen (DR-H).
A recent article, Hydrogen Ironmaking: How it Works, explains that hydrogen can well be used to make iron from ore. Electricity can be used to turn the iron into steel. The expected CO2 emissions from this new route are less than 10% than from current blast furnaces.
“The production of hydrogen should be low in CO2,” Ramirez stresses. But green hydrogen, generated with green electricity, is not an option for the time being. That would require the output of all current Dutch wind turbines on land and at sea. (NRC – in Dutch). So Ramirez opts for a mix of mainly blue hydrogen (produced from natural gas with carbon dioxide capture and storage) and a bit of green. “But that is not a permanent solution,” she warns.
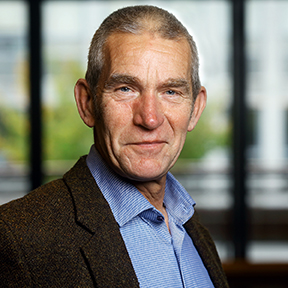
Do you have a question or comment about this article?
j.w.wassink@tudelft.nl
Comments are closed.