C1 Connections (The Hague) and TU Delft developed and tested an improved system to bolt wind turbines to monopiles. “We’re just in time for the offshore wind expansion.”
As the tower is lowered, guide strips like shoehorns allow the tower to land precisely in place. (Photo: Casper van der Kloet)
Securing a wind turbine to a foundation pole at sea is a tricky job. You need a calm sea and more than a hundred bolts and nuts thicker than your wrist to securely fasten the flanges (fastening rings around the end of a tube) of the monopile and mast together. The bolt ring is a traditional mounting method, that works well on land. But with offshore wind farms becoming increasingly large, it’s Jasper Winkes’ growing conviction that this mounting technique has no place at sea.
Winkes is founder and director of C1 Connections, a Hague-based startup that developed safe and faster installation of large offshore wind turbines. He is working with major wind turbine suppliers to introduce the patented connection system he developed with TU Delft.
The ‘C1 Wedge Connection’, as the system is called, was successfully demonstrated with a Heerema lift vessel late last year. As the tower sank on the pile, guide strips like shoehorns allowed the tower to land precisely in place.
Winkes thinks that the large wind farms planned (in Dutch) in the North Sea until 2030 can be equipped with the C1 Wedge Connection. “We are just in time with it,” he says about that.
The placement of the wedges (‘fasteners’) is done after the positioning on the inside of the tower. (Photo: C van der Kloet)
About six years ago Jasper Winkes, a mechanical engineer from Eindhoven University of Technology, approached Professor Milan Veljkovic, steel construction expert at TU Delft’s Faculty of Civil Engineering and Geosciences, with a bold plan. He proposed replacing the traditional bolted L-flange with two perforated rings at the base of the tower. These rings fit on the inside and outside of the rim of the monopile, which has matching elongated holes. Patented bolt-driven wedges, or fasteners, are then pushed into all the holes from the inside and tightened with light equipment. A short animation on C1 Connections’ website shows the working principle. Note the outside ring, shielding the connection from weather and seawater.
The Mockup used for the fatigue tests was almost full-size. (Photo: Video still)
The first studies were feasibility studies and numerical analyses, says Veljkovic. It was only after the work of three master students that a PhD student embarked on experimental tests of the connections to test for material fatigue. A 4.5 metre diameter mock-up with the patented connection was tested and many samples were fatigue tested. “Basically, you apply the forces that you expect over a period of 25 years in a couple of weeks,” Veljkovic explains. The resulting research articles report that the fatigue resistance is very high. “It means that everything else on the wind turbine will fail sooner than the connection between pile and tower.”
Winkes says that a prototype of the C1 Wedge Connection was successfully field tested for a year and a half on “one of the largest wind turbines”.
Infographic about a 15 MW windturbine. (Image: C1 Connections)
What makes the C1 Connection so fatigue-resistant? “Imagine the bolted L-flanges,” Winkes explains. “Each gust of wind pulls the bolts on the windward side of the flanges. In a C1 Connections, the tension caused by the wind is perpendicular to the much thinner bolt. Consequently, wind gusts don’t load the bolts. Instead, the wind load is distributed evenly across the entire connection.”
Winkes is now in contact with the large wind turbine manufacturers and has a trump card up his sleeve. These OEMs (Original Equipment Manufacturers) with their ever-larger turbines are primarily looking for improved material fatigue resistance and a higher allowable load, Winkes says. They regard C1 Connection’s fast and safe installation a bonus.
Video by Topsector Energie about C1 Connection.
- More information and contact details on C1 Connections’ website.
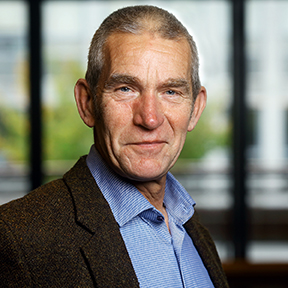
Do you have a question or comment about this article?
j.w.wassink@tudelft.nl
Comments are closed.