During his PhD research, Dr. Christiaan Boelsma came across two suitable materials for hydrogen sensing at the tip of an optical fibre and says: ‘There are still many new sensor possibilities available to explore.’
Hydrogen plays a crucial role in many sectors of the industry. The chemical industry cannot do without it. In the food industry hydrogen emission is one of the first signs of the onset of decay. Hydrogen cars have appeared on the roads, and they may be the frontrunners of the hydrogen economy. Hydrogen, after all, is the only energy carrier without CO2-emissions.
Notwithstanding all its uses, hydrogen is hard to detect as it’s a colourless, odourless and tasteless gas. But since hydrogen combines easy ignition with a large energy output, detection of hydrogen is essential for safety. The most common hydrogen detectors are solid-state and equipped with electronics. That implies the risk of sparks, which is not a good combination with the highly combustible hydrogen.
Presence of hydrogen
Thus, the development of new materials for optics-based hydrogen detection is good news. The materials that Dr. Christiaan Boelsma has patented may be deposited as a thin coating on the tip of a glass fibre. The presence of hydrogen at the end of the fibre results in a change in its optical reflection. The electronics required can be located at a considerable distance from the sensor, and presumably, the sensors will not be very expensive.
The change in optical reflection is a consequence of the absorption of hydrogen by certain metals. The absorption of hydrogen, or the formation of a metal-hydride, changes the electronic properties of the metal. If the metal layer is sufficiently thin, typically less than 0.1 micrometre, changes in the electronic properties also result in optical changes in reflection and transmission of the layer.
Mixtures
During his PhD research at the Materials of Energy Conversion and Storage (MECS) group of the Faculty of Applied Sciences (TNW) Boelsma has created and tested a range of various mixtures of transition metals in a magnetron sputtering device. Here, thin layers of metal are deposited on glass. One can create mixtures of metals or separate layers by switching between metal targets during the sputtering process. The most promising materials were multilayers from Zirconium-Magnesium (Zr-Mg) alloys and Hafnium. The thickness was 70 and 40 nanometres respectively, topped with a 10-nanometre capping layer of Palladium for protection.
Measurements showed that Zr-Mg can be used to measure hydrogen pressure from one to 10,000 pascal (120 degrees Celsius). Hafnium has an even larger range of 0.01 to 10,000 pascal and possibly even starting as low as 0.00001 pascal. That translates into an incredible sensitivity of one part in a trillion for measuring hydrogen.
So far, the two mentioned materials have been patented. Dr. Bernard Dam, Boelsma’s PhD supervisor, is looking for industrial partners to develop the optical hydrogen sensor into a prototype.
Improving response time
One of the first things to be done is improving the response time, which depends on, amongst others, the pressure (slower at lower pressure), working temperature and capping material. The response time may be extremely long (as much as several hours at room temperature), but can be improved by adding a proper topping layer, as Boelsma has shown. Adding a Teflon layer to the Hafnium-Palladium material reduced the response time from five hours to 30 minutes.
Boelsma has discovered a promising principle for measuring hydrogen, which fits in well with the transition to sustainable technologies. He is convinced that there is a lot of room for improvement and a host of other materials with comparable properties to be unveiled. We especially look forward to the first working prototype.
Christiaan Boelsma, ‘Tailoring the Hydrogen Detection Properties of Metal Hydrides’, PhD supervisor Prof. Bernard Dam (TNW), March 10, 2017.
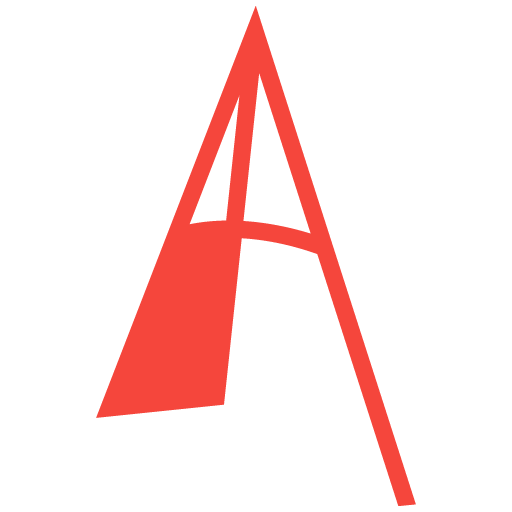
Comments are closed.