With the plastic soup in the ocean in mind, TU Delft engineer Jerry de Vos developed a scanner that should make plastic recycling easier. He won the James Dyson Award with it.
Jerry de Vos on waste island Thilafushi. Here he converted a sea container into a waste processing workstation. (Photo: Jerry de Vos)
An entire island that has been converted into a waste dump. It really exists, in the Republic of the Maldives. In the middle of the Thilafushi atoll there is a mountain of smouldering garbage that is so large and steep that the slightest breath of wind sends plastic rubbish into the ocean. ‘Waste management Thilafushi’ is the caption to a photo in which Jerry de Vos is positioned in front of this tropical mountain of smoking garbage.
It is one of the many places that De Vos visited in his quest for a more sustainable use of plastics. The photo is included in his graduation report ‘Plastic Identification Anywhere’, for which he received the international James Dyson Sustainability Award 2021 this week. De Vos described a portable scanner (smartphone size) in it, which reveals with a simple press of the button what kind of plastic you are looking at.
‘Sorting is often done by hand and by eye’
Only 14 percent of all plastic worldwide is currently recycled. This scanner should help improve that percentage. If people sorting plastic could separate the different types of plastic more accurately and faster, the entire recycling process would become economically more interesting, in De Vos’ opinion.
“Much of the plastic in the oceans comes from low-income and middle-income countries where the sorting is often done by hand and by eye,” he explained. “This takes a lot of time and is prone to error, because the identification triangles are often missing or no longer legible.” These triangles with information must be printed by manufacturers on their plastics to make the plastics identifiable.
In the past few years, De Vos travelled around the world to see how people in different countries deal with plastic waste. In Mauritius and in Algeria, he helped to set up small waste-processing companies. On Thilafushi he converted a shipping container into a waste-processing workplace. “I did that together with Precious Plastic, an organization that is devoted to plastic recycling. The equipment in such a container consists of a shredder that cuts the plastic up and an oven to melt the plastics, after which new products can be made on site. Bowls or protective covers for telephones, for example. Or sheet material for construction.”
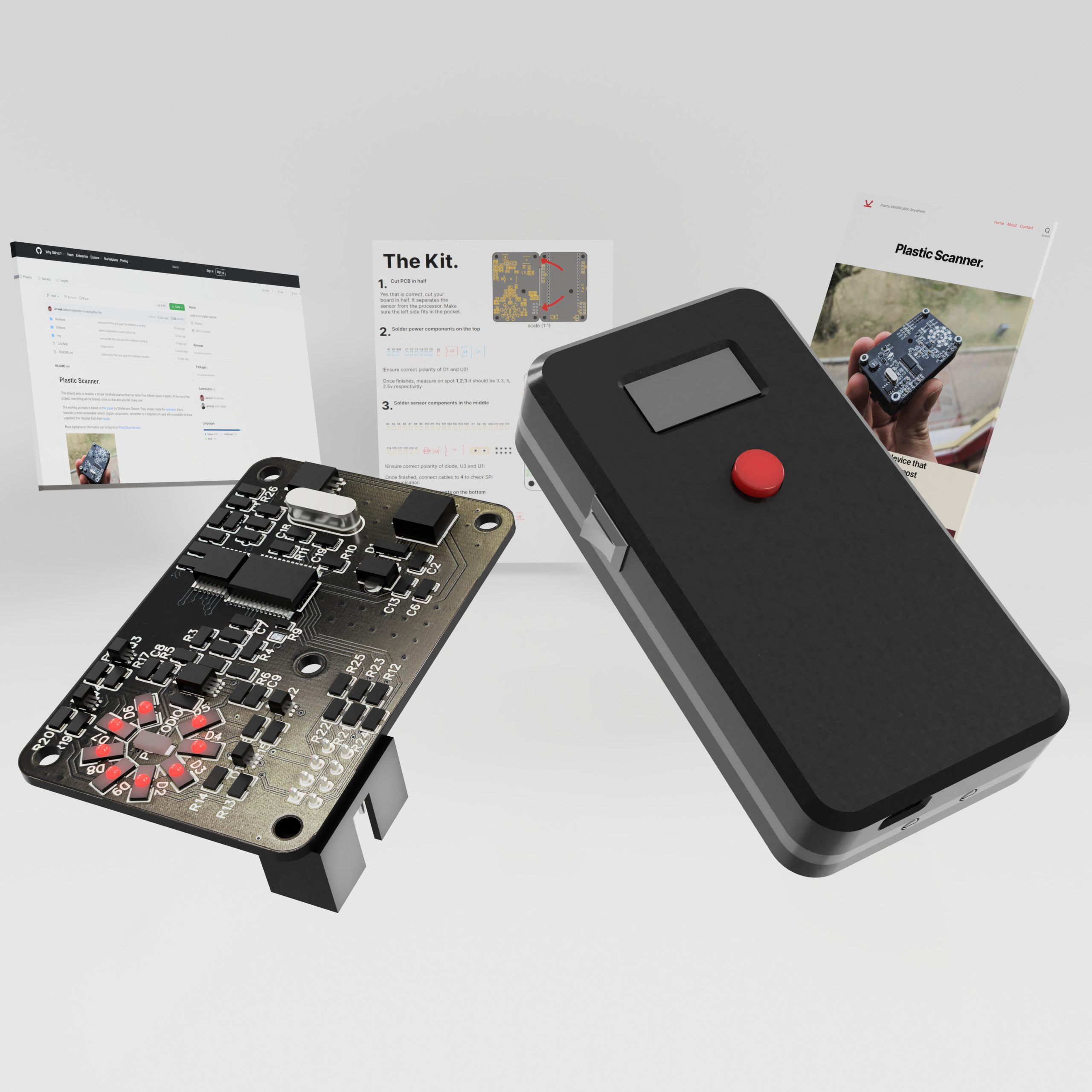
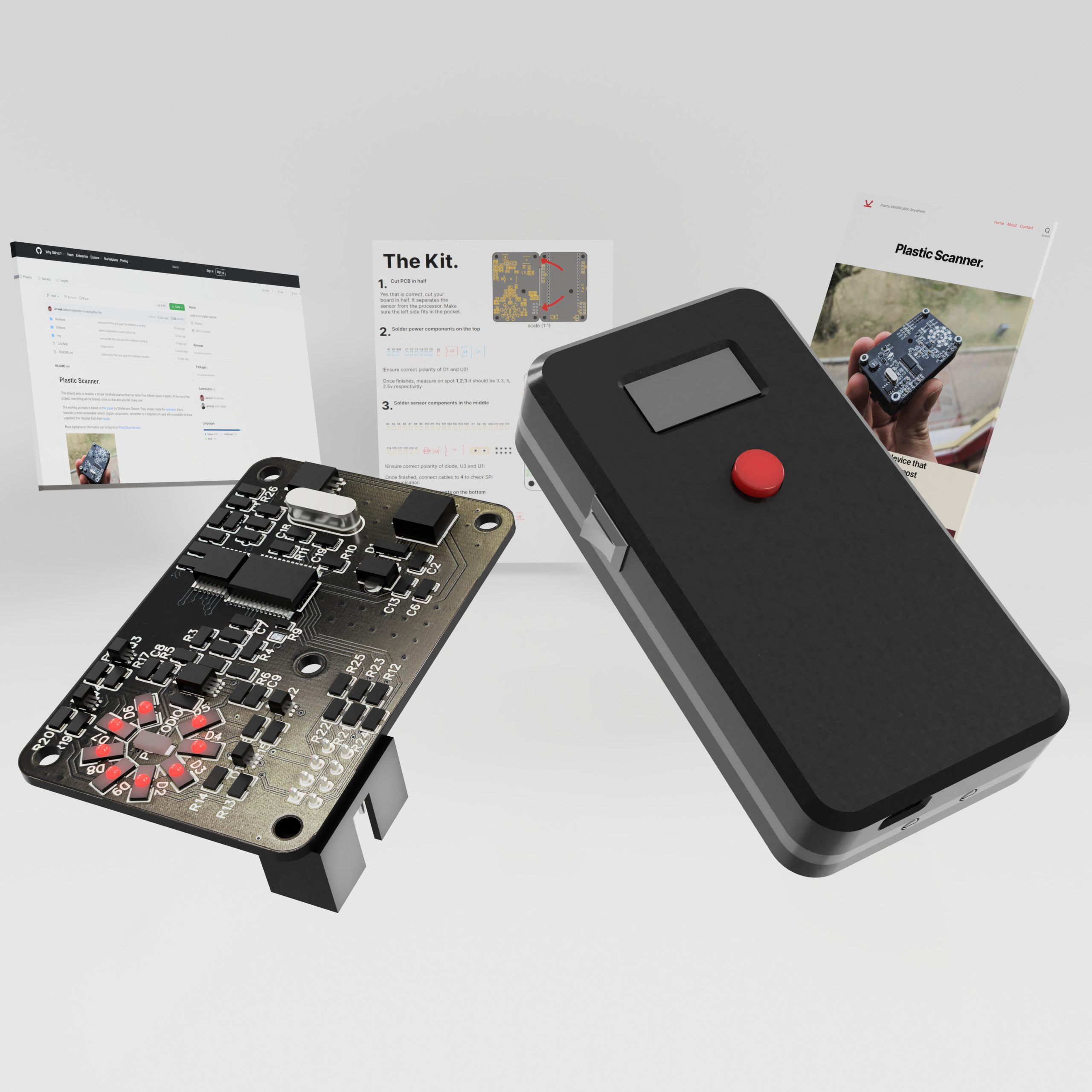
In the future, such small-scale processing workplaces may have another instrument in their toolbox: the scanner developed by the TU Delft alumnus. To be more specific, he took the first step towards it. He has created the scanning device and the case. These two parts still need to be integrated. With the James Dyson award money (€33,000), he intends to finish the product.
The device uses near-infrared spectroscopy. It emits infrared light and analyses the reflected photons. Different plastics reflect light in characteristic ways. With this method, around three-quarters of the plastics used in daily life can be categorised.
The use of infrared light in sorting waste is not new. Large waste-processing companies, like Suez in Rotterdam, use it as well. They employ devices costing tens of thousands of euros that emit a broad spectrum of light. But a much smaller number of light frequencies can be used to distinguish the majority of plastics. De Vos’s scanner uses eight LED lamps which each send out an individual wavelength. “The advantage is that this allows you to produce much smaller and cheaper devices. They are less accurate than the large industrial machines, but they are sufficient in many cases.”
The scan technique still has to be refined. Currently, it works best with light-coloured plastics because they reflect more light. The scanner still has difficulty with dark-coloured ones.
Open source
But that must not spoil the fun. Patent the invention is the next step you would think, before someone else steals it. Right? But De Vos looks at the situation differently. He is building on the work of other engineers, including that of the young German inventor Armin Straller, who had also been brooding on a type of scanner for plastics and published his findings openly on the digital coding platform Github. De Vos feels that his work should also be accessible to everyone.
‘I would be happy if I would come across the scanner on AliExpress’
He utilised an open source licence (GPL-v3 licence) for his project. This means that everyone may use the knowledge, if this right is given directly to others and the author(s) cited. “I would love it if other engineers would start working on the idea and I see the scanner offered for sale on AliExpress in five years’ time. I am not interested in the bother about IP-rights. I have seen the terrible conditions under which people work on waste dumps. That motivated me to make this project open source.”
The plastic scanner must become available for less than €100 in the near future, expects De Vos. “At the moment it would cost about €400 to make. But if you produce a hundred of them, then they will be four times cheaper, through the economy of scale.”
Affordable
That is still much too expensive for the ragpickers, the poor people who scramble over the waste dumps with large bags to collect a particular kind of plastic that can be sold to dealers. But small recycling companies can afford the device, which will raise the level of the entire waste-processing chain in developing countries.
“At a later stage, it may even be possible to develop an even smaller scanner that you could link to your smartphone,” said De Vos. “Your smartphone acts as the battery, computer and display. That would reduce the cost even further, making the scanner affordable for more people.”
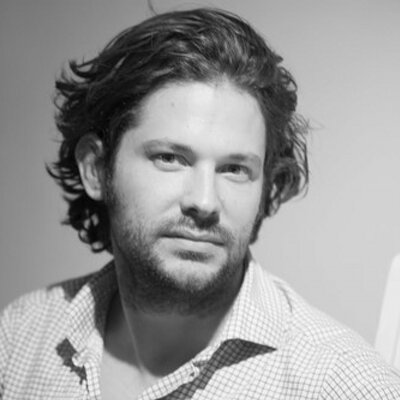
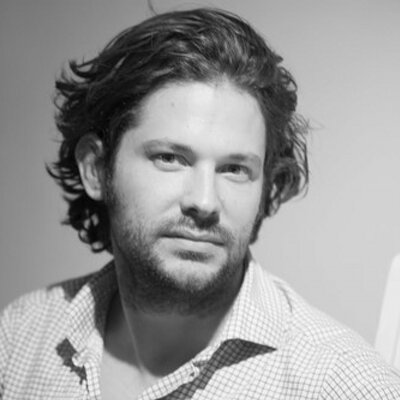
Do you have a question or comment about this article?
tomas.vandijk@tudelft.nl
Comments are closed.