TU Delft alumnus Jan van der Tempel is nominated for the European Patent Office Inventor Award. Delta sailed with him and saw the first electrical footbridge.
Jan van der Tempel explains that “In metres high waves you normally cannot cross to a wind turbine. But you can do so with an Ampelmann.” (Photo: Jos Wassink)
The Horizon Star has two Ampelmanns on the aft deck. (Photo: Jos Wassink)
IJmuiden, 07:30. About 20 people are gathered opposite a dilapidated bar on the quay. A compact man with brown curls greets everyone with the now familiar elbow touch. Welcome, says Dr Jan van der Tempel (47), CEO of Ampelmann and the organiser of the offshore trip. Once everyone has been given safety shoes, helmet, and glasses, they board the Horizon Star – a 100 metre offshore supply ship. The front of the ship is a bridge and helicopter deck. The stern is a huge open deck. There are two hydraulic Ampelmann gangplanks between which men – and one woman – are walking in orange overalls. How the gangplanks work and the difference between them will be revealed today. “Typical Jan,” says one of the engineers in an orange overall. “We install a gangplank and at the end of the same week we have a day for our contacts and the press. Nobody else does this.” Just as nobody else owns a tower in the North Sea. More about that later.
“The mentality at the time was that we would sort out the transfer later.” (Photo: Jos Wassink)
Biergarten
The idea for the Ampelmann came to Van der Tempel on a terrace in Berlin in 2002 during a large offshore wind symposium. After a year of working for Boskalis at the Danish Horns Rev offshore wind park, he returned to TU Delft. He was doing his PhD research into the support structures of wind turbines under Prof. Jan Vugts (Faculty of Civil Engineering and Geosciences) and Prof. Gijs van Kuik (Aerospace Engineering). The growth prospects of offshore wind was already clear and people were thinking about 10,000 wind turbines in the North Sea. How these would all be built and maintained was an issue for later.
“The thinking at the time was that we would sort out the transfer at some point,” remembers Van der Tempel. By then he had already had to move from a moving ship to a static steel structure several times. Two Dutch engineers in the Biergarten believed that this had to be done differently. They were Jan van der Tempel and David Molenaar. It had to be done more safely, manageably and better. Transferring at sea needed to be just as safe as crossing the street.
With the iconic Berlin Ampelmann pedestrian crossing light everywhere in the German capital city, the company’s name was soon born. And the solution for the transfer was also dreamed up quickly – a hexapod that they were familiar with in flight simulators. In this case, every motion was driven by three pairs of hydraulic cylinders on three corners of a frame. The Ampelmann should do the reverse; the cylinders compensate the movements of the ship so that the frame with the extendable gangplank remains still while the ship below it rises and falls on the waves.
Van der Tempel developed the technology while working on his PhD research with the help of bachelor and master students that he supervised in his role as PhD Candidate. “The machine was ready in 2005,” he says. In an amateur video, he shakes a small cupboard up and down while next to him a platform the size of a coffee table moves, with a little delay, in parallel. The prototype works. In the meantime, Van der Tempel took business lectures and wrote a business plan (in Dutch) that immediately won a prize.
Thanks to a subsidy application together with Shell, which he got aboard by “drinking a lot of coffee and talking enthusiastically”, Van der Tempel could have his first real-life Ampelmann built. It was large enough to fill a gymnasium. The unit was tested in 2007 at the North Sea wind park in which Shell was also involved. Then followed a demonstration with 25 guests on a vessel next to an oil platform at Scheveningen that had been removed by Smit, an engineering company. “There was a storm at sea and there were two and a half metre waves. They were unable to transfer safely and the work remained undone for a week. But with the Ampelmann you could have transferred safely.” He could not have wished for a better demonstration.
After the first demonstration, Ampelmann grew into a company with 350 employees. The company maintains a fleet of 65 hydraulic gangplanks which they lease out. Worldwide, they have transferred six million people and 17,000 tons of freight. You would think that Van der Tempel as the CEO would have his hands full, but he is apparently involved in a host of other activities. In Delft, he is co-founder of the De Oude Bibliotheek, the offshore academy. Located in the old UB (Raam 180, Delft) building, the DOB Academy runs courses on offshore energy, meetings and congresses, and produces educational videos in its own studio.
The Prinses Amalia wind park has 60 turbines of 2 MW. (Photo: Jos Wassink)
Seal
Back to now. After a two hour sail, the Horizon Star pulls up against the Prinses Amalia wind park, 23 kilometres off the coast at IJmuiden. It is a sunny day and the light offshore wind means that the sea is calm. With the bow sailing into the current, the ship enters the wind park sideways and heads to a still turbine. Eneco, the owner of the park, has given permission to demonstrate the gangplanks there. The journey through the wind park is extremely slow and finally ends a few metres from the tower. The dynamic positioning keeps the ship in position despite any wind and current. A seal swims around the turbine tower, rides the churning current, dives below the surface and comes up again upstream. It looks like a seal funfair.
A first for the A43e, the ‘e’ standing for electric. (Photo: Jos Wassink)
Green for three seconds
When the humming cylinders extend, the platform of the Ampelmann rises like a fairground ride. Once at the right height the platform stabilises and the people on the platform see the ship below them moving. The operator eases the gangplank towards the wind turbine and stretches the bridge out until it touches a wide rubber bumper. At the base of the gangplank, on the platform, the light flashes green for three seconds – someone may cross. An Ampelmann staff member crosses the bridge to the wind turbine and steps off completely safely. According to the specifications, this zebra crossing at sea works up to a significant wave height of 2.5 metres.
Ampelmann: crossing when it’s green. (Photo: Jos Wassink)
The Ampelmann A-type that we see today is the first electric version and the first of many. The hydraulic pressure is generated by two electrical pumps for each cylinder (everything is double on Ampelmanns to ensure safety and continuous operations). Furthermore, as electricity is generated when oil flows from high to low pressure, the energy consumption is 75% to 90% less compared to the standard machine (now 45 kilowatt). Its weight has also been reduced from 45 to 25 tons.
“From now on, all new A-type machines will be electric,” says Van der Tempel. “We will then convert the existing machines into electric powered, including the larger E type.”
Coffee cup principle
Van der Tempel has big plans for his test tower in the North Sea. (Photo: Jos Wassink)
The empty steel tower just outside the Amalia wind park is referred to as ‘The tower of Jan’. There are few people who have their own tower in the North Sea, but Van der Tempel had it erected for independent offshore experiments. The employees can test and adjust the Ampelmanns there. Van der Tempel wants to test a new system of offshore construction here in October. He knows just how challenging it is to get a tower in exactly the right place with a crane and then to have to attach bolts to it. Van der Tempel describes his version as the upside down coffee cup method: all the parts are conical – they are all somewhat narrower at one end – and fit on top of each other. If the demonstration in October goes well, the construction of thousands of new wind turbines in the North Sea may be significantly simplified.
After that is the big work. The E-type is the bigger and heavier Ampelmann that can be used up to a significant wave height of four metres. Before it starts operation, two diesel drive hydraulic pumps are started. The E-type is a big boy that needs up to 500 kW. Only now do we realise just how quiet the smaller electrical A-type was. The heavy crane stretches the gangplank up into the air and plays out a hook to which a small container is attached. With its steel gangplank, the E-type can be used as a crane to transfer parts without having the container, that weighs tons, swinging dangerously in the air.
Swinging containers are a nightmare in the offshore. (Photo: Jos Wassink)
After that is the big work. The E-type is the bigger and heavier Ampelmann that can be used up to a significant wave height of four metres. Before it starts operation, two diesel drive hydraulic pumps are started. The E-type is a big boy that needs up to 500 kW. Only now do we realise just how quiet the smaller electrical A-type was. The heavy crane stretches the gangplank up into the air and plays out a hook to which a small container is attached. With its steel gangplank, the E-type can be used as a crane to transfer parts without having the container, that weighs tons, swinging dangerously in the air.
The Ampelmann engineers exude pride and camaraderie. (Photo: Jos Wassink)
High pressure
Van der Tempel manages the company and also spends a lot of time with other innovations for the offshore sector. If you chat with him for a while, apart from the Ampelmann, you will hear him talk about De Oude Bibliotheek, about vibratory driving instead of pile driving, and the Delft Offshore Turbine. The Delft Offshore Turbine (DOT BV) is a project in conjunction with TU Delft which uses a hydraulic pump that brings seawater under high pressure (hundreds of bars) instead of a generator in a wind turbine. The seawater under pressure drives a turbine elsewhere. In the DOT concept, several windmills jointly drive a large turbine. The advantages of this patented idea are the simpler construction of the windmills; less weight at the top of the turbine tower; and fewer components and hence fewer defects and less maintenance.
Photo session on the helipad. (Photo: Jos Wassink)
After the successful demonstration, there is a relaxed atmosphere among the Ampelmann engineers on the return trip. Without exception they all come from TU Delft and many have a background in offshore and mechanical engineering. The 12 of them have worked all week on the new electrical Ampelmann and now, on the return trip, they will be immortalised on the gangplank and on the helipad. They are clearly proud and feel like comrades in arms.
“At any other company of this size there is a representative that talks to the client, a design department that works on the computer, a construction department, testers and so on,” says one of the engineers when I ask him what it’s like to work here. “But here we do all that ourselves. Right through to the delivery and hearing what could be done differently or better.”
Van der Tempel’s mind is bursting with ideas. “Do you know the best thing about seawater under pressure?,” he asks. “Yes, you can generate electricity but you can also produce freshwater through reverse osmosis. And from freshwater you make electrical powered hydrogen.” Van der Tempel sees it clearly – unmanned factories at sea that supply green hydrogen through pipes.
The Horizon Star is once again moored along the Loggerkade quay in IJmuiden. Contacts, press and Ampelmann fans hang over the railing and talk to each other in the evening sun. After a trip of 10 hours, everyone wants to disembark, but for some reason they have to wait. Then the crew starts up the crane that lifts the gangplank and places it on the quayside. That takes ages. “Why don’t we just use the Ampelmann?” someone cheerfully asks.
PATENT OFFICE
The European Patent Office’s (EPO) database contains a series of patents under the name of Jan van der Tempel, often in combination with other people.
- Ship with platform on top deck that regulates its position, TU Delft, 2006
- Extendable gangplank, TU Delft, 2008
- Extendable gangplank, TU Delft, 2008
- Hydraulic windmills, TU Delft, 2009
- Hooking mechanism for gangplank, Ampelmann, 2015
- Hexapod system (follow up), Ampelmann, 2015
- Hexapod system (follow up), Ampelmann, 2019
- Coffee cup system for offshore, DOT BV, 2020
- Hydraulic windmills, DOT BV, 2020
- Offshore transport system, DOT BV, 2021
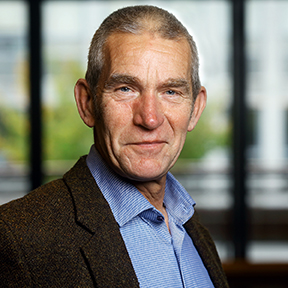
Do you have a question or comment about this article?
j.w.wassink@tudelft.nl
Comments are closed.