Just by changing the light intensity Hiroshi Ohji can produce freestanding 3-D silicon structures, resulting in a cheap accelerometer for air bags and a novel DNA separating chip. Thanks to the Dutch coffee and lunch breaks.
Just by changing the light intensity Hiroshi Ohji can produce freestanding 3-D silicon structures, resulting in a cheap accelerometer for air bags and a novel DNA separating chip. Thanks to the Dutch coffee and lunch breaks.
,,We Japanese are hard working people. To be honest, my first impression of the Dutch was that they work few hours, because of their short working days with long coffee and lunch breaks,” says Dr. Hiroshi Ohji, an employee of Mitsubishi Electric Corporation. ,,My boss wanted to start with micromachining and therefore sent me to Delft in the middle of the nineties to find out more about this topic. He had heard good stories about the Delft researchers from a friend of him who was in Delft at the time.”
During his two-year stay with the Electronic Instrumentation group in Delft Ohji’s opinion about the Dutch research culture turned around. ,,I found out that people here aren’t lazy. They don’t exchange the latest gossip during their breaks, but discuss all kind of research questions. While in Japan a professor is very high up the hierarchical ladder and not someone you argue against, in Delft you can have frankly conversations with your professor about your research during these breaks, sometimes even resulting in innovations.”
Four years later Hiroshi Ohji is in Delft again, to defend his PhD-thesis on a promising new silicon etching technique. He explains that by changing the light intensity he can change the width of a pore while making it. A higher light intensity induces more tiny electric holes in the silicon layer and the more tiny holes surround the tip, the more silicon is eaten away or dissolved by the etchant and the wider the pore becomes.
What%s so special is that this makes it possible to etch all kind of three-dimensional structures, even freestanding structures in just one production step, where currently five separate steps need to be taken. In one step Ohji can make
the freestanding structure of a accelerometer, a small massive plate with an handle which moves into the direction of the acceleration.
Balls of DNA
Ohji also works on a novel DNA-separation chip. DNA-molecules of different lengths will be separated by a chip rather than by a sticky gel in the future, according to Ohji. Afterwards the separated DNA-molecules can be sequenced to unravel their DNA-code, for example, for human disease diagnosis.
Ohji believes his technique will result in a cheaper and better separating device, although he hasn%t done separating experiments yet. His chip is a kind of sieve consisting of silicon pillars that are standing less than several hundreds of nanometers apart from each other. He proved that DNA would go through the pores between the pillars if a voltage were applied on the chip.
His next step at Mitsubishi Electric Corporation, which not only focuses on electronics for car manufacturing, is to make chips with bigger and smaller pore sizes and applying different voltages so he can separate a mixture of DNA molecules by their length. Small ones, which form small balls will migrate through the pores quickly, while big DNA-molecules form bigger balls, therefore consuming a lot of time before reaching the other side of the chip if the pores are small.
Commercialising
Innitially, Ohji intended to stay in Delft for only a year. ,,In 1996 it took me about three months to get used to the Dutch culture. Therefore, after a year I had poor results and asked my boss if I could stay one more year. After my second year I asked my boss, please let me stay one more year. But then he said no.”
Ohji decided to ask his Delft professor, Paddy French, whether he had a chance of obtaining a PhD-degree when he continued his research project in Japan. He said yes. ,,Very few Japanese have a foreign PhD-degree, so therefore my boss also gave me permission to continue my research after I returned to Japan.” At Mitsubishi Ohji could dedicate half of his time to finish his PhD-thesis.
Currently he%s commercialising his own technique. ,,During my PhD-research, I developed a kind of prototype for small wafers. For mass production micromachining must be able to use bigger wafers. One of the biggest problems is the keep the light intensity homogeneous on a 6 inch wafer.”
His co-operation with the Delft people will continue. ,,My company pays Paddy French to come to Japan once a year. And I come to Europe once or twice a year for a conference.”
His children stay in Japan, however. ,,They used to be able to speak Dutch quite well after living in The Netherlands for two years. But at the moment they aren’t even able to count in Dutch anymore,” Ohji regrets.
,,We Japanese are hard working people. To be honest, my first impression of the Dutch was that they work few hours, because of their short working days with long coffee and lunch breaks,” says Dr. Hiroshi Ohji, an employee of Mitsubishi Electric Corporation. ,,My boss wanted to start with micromachining and therefore sent me to Delft in the middle of the nineties to find out more about this topic. He had heard good stories about the Delft researchers from a friend of him who was in Delft at the time.”
During his two-year stay with the Electronic Instrumentation group in Delft Ohji’s opinion about the Dutch research culture turned around. ,,I found out that people here aren’t lazy. They don’t exchange the latest gossip during their breaks, but discuss all kind of research questions. While in Japan a professor is very high up the hierarchical ladder and not someone you argue against, in Delft you can have frankly conversations with your professor about your research during these breaks, sometimes even resulting in innovations.”
Four years later Hiroshi Ohji is in Delft again, to defend his PhD-thesis on a promising new silicon etching technique. He explains that by changing the light intensity he can change the width of a pore while making it. A higher light intensity induces more tiny electric holes in the silicon layer and the more tiny holes surround the tip, the more silicon is eaten away or dissolved by the etchant and the wider the pore becomes.
What%s so special is that this makes it possible to etch all kind of three-dimensional structures, even freestanding structures in just one production step, where currently five separate steps need to be taken. In one step Ohji can make
the freestanding structure of a accelerometer, a small massive plate with an handle which moves into the direction of the acceleration.
Balls of DNA
Ohji also works on a novel DNA-separation chip. DNA-molecules of different lengths will be separated by a chip rather than by a sticky gel in the future, according to Ohji. Afterwards the separated DNA-molecules can be sequenced to unravel their DNA-code, for example, for human disease diagnosis.
Ohji believes his technique will result in a cheaper and better separating device, although he hasn%t done separating experiments yet. His chip is a kind of sieve consisting of silicon pillars that are standing less than several hundreds of nanometers apart from each other. He proved that DNA would go through the pores between the pillars if a voltage were applied on the chip.
His next step at Mitsubishi Electric Corporation, which not only focuses on electronics for car manufacturing, is to make chips with bigger and smaller pore sizes and applying different voltages so he can separate a mixture of DNA molecules by their length. Small ones, which form small balls will migrate through the pores quickly, while big DNA-molecules form bigger balls, therefore consuming a lot of time before reaching the other side of the chip if the pores are small.
Commercialising
Innitially, Ohji intended to stay in Delft for only a year. ,,In 1996 it took me about three months to get used to the Dutch culture. Therefore, after a year I had poor results and asked my boss if I could stay one more year. After my second year I asked my boss, please let me stay one more year. But then he said no.”
Ohji decided to ask his Delft professor, Paddy French, whether he had a chance of obtaining a PhD-degree when he continued his research project in Japan. He said yes. ,,Very few Japanese have a foreign PhD-degree, so therefore my boss also gave me permission to continue my research after I returned to Japan.” At Mitsubishi Ohji could dedicate half of his time to finish his PhD-thesis.
Currently he%s commercialising his own technique. ,,During my PhD-research, I developed a kind of prototype for small wafers. For mass production micromachining must be able to use bigger wafers. One of the biggest problems is the keep the light intensity homogeneous on a 6 inch wafer.”
His co-operation with the Delft people will continue. ,,My company pays Paddy French to come to Japan once a year. And I come to Europe once or twice a year for a conference.”
His children stay in Japan, however. ,,They used to be able to speak Dutch quite well after living in The Netherlands for two years. But at the moment they aren’t even able to count in Dutch anymore,” Ohji regrets.
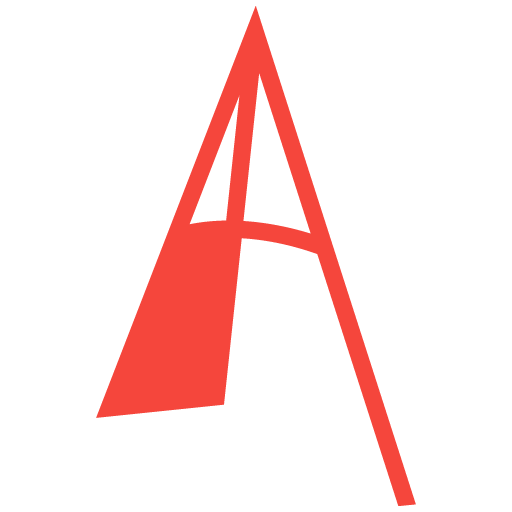
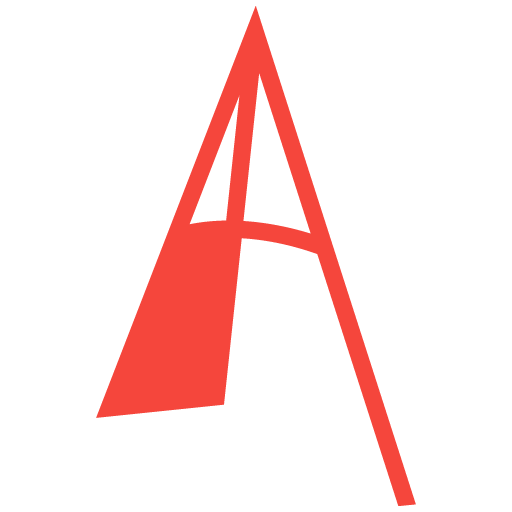
Comments are closed.