Imagine a city where the buildings are designed and built using computers and robots and that these spaces interact with and can be reconfigured by you. Squads of robots serve us to design, produce and assemble and customise our built spaces.
The Hyperbody chair at the Faculty of Architecture and the Built Environment is applying this vision to engage with the future of our built environments. The Robotic Building group, established in 2014 within Hyperbody, focuses on developing robotised systems for the built environment. They experiment with digitalized ways of building and robots to empower the user and improve the built environment, without compromising on quality.
“Responsive buildings and robotic systems are already around us in buildings,” said assistant professor Henriette Bier of the Robotic Building group. “We already have automatic doors and more sophisticated embedded systems such as adaptive shading installations and indoor climate controlling functions.” But Hyperbody envisages a more intense level of interaction, an enhanced dialogue between human and machine to achieve a complementary authorship of built space. By no means just completely automated push-of-a-button design and build, but an integrated active smart system with information feedback loops.
“We want to train the machines to learn and interact with us and at the same time, by producing and learning, bring about a shift in design and design education,” said PhD researcher Sina Mostafavi.
“In 2012 we started using cheap scrap robots from the car industry, and in 2014 continued with new ones. We customized them with 3D printed components and started to push these developments,” said Bier. “We’re developing robotised processes to exploit material properties and geometries not only at the spatial level but also to compose matter more efficiently. Design-to-robotic-production (D2RP) systems can deposit matter where needed, as needed, and make mass customisation of user oriented design feasible.”
Optimisation and efficiency
Robotics can also help to use space more efficiently. The Hyperbody Pop-up apartment project has explored maximising a minimal footprint of 50m2 using interactive moving components that adapt to the activity of the user. The prototype makes ingenious use of material and curved geometries to make the fold away elements morph into furniture and space partitions. This concept will be researched further to develop a spatially and sensorially reconfigurable apartment with embedded robotic devices.
Application in developing countries
Another development within the EU Horizon 2020 programme involves a deployable system of robots enabling ad-hoc building with local materials to be tested in Ethiopia. A mobile version of Hyperbody’s D2RP system will be powered by electricity generating kites developed in collaboration with the Airborne Wind Energy System Modelling, Control and Optimisation project (AWESCO) at TU Delft. The energy kites are a mobile, lightweight alternative to wind turbines that fly higher in stronger winds, efficiently producing energy with less material.
Network and exhibitions
Though their Protospace design studio, with sensors integrated in its wooden floor, and Protofab workshop take up less than 1% of BK floor area, their research is not marginal. They are networked with the Delft Robotics Institute and other research institutes all over the world such as MIT and ETH Zurich. In ten years the Hyperbody chair at BK has grown to attract around 100 students a year.
Hyperbody work has recently been exhibited in France at the Synthetic exhibition 2015 ESBA TALM (École Supérieure des Beaux Arts Tours Angers Le Mans). They regularly exhibit their pieces at V2 gallery in Rotterdam and they will participate at RoboArch 2016 in Sydney.
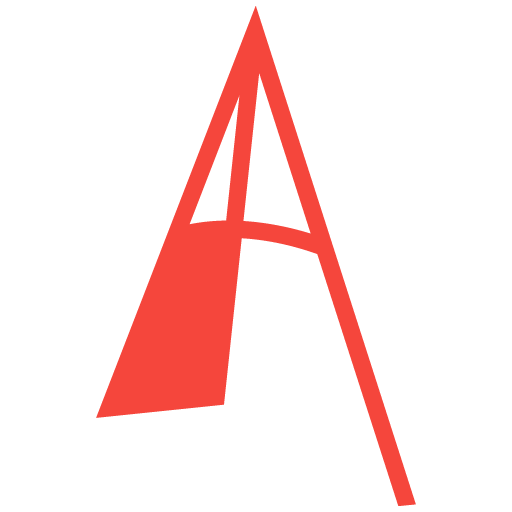
Comments are closed.