Het is dringen op de bottellijn, en bierflesjes komen daar niet ongeschonden uit. Uiteindelijk krijgen ze alle de bekende witgerande schaafwond. Het mechanisme achter deze scuffing is echter nooit goed beschreven, ontdekte dr.i
r. Jan do Livramento.
Bottleneck
Bier is een kwestie van marketing. Maar van het zorgvuldig geconstrueerde sentiment dat bier omringt, is aan de bottellijn weinig te merken. Niks geen eeuwenoude receptuur die van generatie op generatie wordt doorgegeven. Bierproductie gebeurt op industriële schaal, en daarbij horen grote getallen. Een beetje productielijn wast, vult en kroont ruim twintig flesjes per seconde. De uurproductie van tachtigduizend pijpjes is daarmee ongeveer gelijk aan de jaarconsumptie van een grote studentenvereniging.
Om deze hoge snelheden te kunnen handhaven worden tussen de diverse onderdelen van een bottellijn bufferzones aangebracht, waarin duizenden flesjes tussen het wassen en afvullen door massaal in de wacht worden gezet. De toepassing van deze flessenbuffers is zo oud als het hoge-snelheidsbottelen zelf, en werd al in de jaren dertig geïntroduceerd door Coca Cola. Zo’n flessenzee in het gareel houden is echter geen sinecure, en het voortdrijven van de wachtende massa maakt ook nog een hels kabaal.
Doordat de flessen in de buffer voortdurend langs elkaar schuren, raken ze bovendien bekrast. Op zich geen ramp, maar omdat geretourneerde pijpjes voor het afvullen worden gereinigd met een zwak etsend reinigingsmiddel, tekent de ring van krasjes zich naar verloop van tijd af als een schrale, witte rand. Geen gezicht in de schappen, en ook nog eens slecht voor de sterkte van de fles. Dit proces heet scuffing, en houdt de bottelaars al decennia bezig. De technische levensduur van een fles zou namelijk tien jaar moeten zijn, maar wordt mede door scuffing bekort tot een jaar of zes. Hierdoor raakt Heineken per jaar ongeveer vijf miljoen gulden extra kwijt aan vervanging van het flessenpark.
Mist
Tot nu is er geen afdoende oplossing voor dit oude probleem gevonden. ,,De eerste artikelen over het onderwerp verschenen al in 1934 bij Coca Cola”’, weet systeem- en regeltechnicus dr.ir. Jan do Livramento, momenteel werkzaam bij Philips. Begin april promoveerde hij op een onderzoek naar bottelen bij hoge snelheden, dat hij als toegevoegd researcher deels bij Heineken uitvoerde. ,,Er is sindsdien natuurlijk wel aan gewerkt, maar de maatregelen tegen scuffing hielden nooit gelijke tred met de almaar hogere snelheden van de productielijnen. Zonder een bijzondere aanpak is dat vechten tegen de bierkaai.”
Om de scuffing tegen te gaan gebruikten bottelaars onder meerflesjes met een beschermende coating, en zochten zij hun heil in mildere schoonmaakmiddelen. Tevergeefs. Do Livramento: ,,Van die speurtocht is men onverrichter zake teruggekeerd. De oplossingen die men vond waren of onaanvaardbaar wegens toevoegingen als zink, of gewoon onbetaalbaar. Enzymen blijken bijvoorbeeld zes keer zo duur uit te vallen als loog, en werken lang niet zo goed.”
Dat alle pogingen om scuffing te voorkomen steeds op niets uitliepen vindt hij niet verwonderlijk. Het verschijnsel is volgens hem namelijk altijd verkeerd begrepen. ,,Bestaande modellen gaan uit van een hydrostatische benadering van scuffing. Begrijpelijk als je die stroom flesjes door de fabriek ziet kronkelen, want de analogie met een vloeistof is dan snel gemaakt. Maar als je het onderlinge krachtenspel tussen de flesjes bekijkt, dan blijkt dat je met deze aanpak ongelooflijk de mist in kunt gaan. Het aantal flesjes is veel te laag om het geheel als een vloeibaar medium te kunnen beschouwen.”
Dat klinkt logisch, want het draait tenslotte om bierflesjes. ,,Ja”, erkent Do Livramento, ,,maar met dit besef moet je de gebruikelijke aanpak wel helemaal overboord gooien. Je krijgt nu te maken met theorieën die je gewoonlijk tegenkomt bij aardwetenschappen, en niet bij systeem- en regeltechniek. Je zou het de kwantummechanica van de koude grond kunnen noemen.”
Onvoldoende begrip van het probleem speelde hem zelf ook parten tijdens zijn onderzoek. ,,Ik dacht in het begin nog dat het een regeltechnisch probleem was, waarbij je honderdduizend flesjes je wil probeert op te leggen. Maar de structuur en de geometrie van de bottelarij spelen hierbij een zeer grote rol. Uiteindelijk bleek het daarom meer een ontwerptechnisch probleem te zijn.”
Sceptisch
Toen ze bij Heineken hoorden welk pad Do Livramento was ingeslagen, was men daar opeens niet meer zo enthousiast. ,,Ze hadden natuurlijk liever gezien dat er een mooi besturingssysteem zou komen, en nu waren ze weer terug bij af”, verklaart hij. ,,Reacties als ‘is dit niet wat ver gezocht’ waren toen niet van de lucht. Men was waarschijnlijk bang dat het onderzoek op een zijspoor terecht zou komen. Dan kom je in een moeilijke positie als onderzoeker, want er gaat vreselijk veel tijd zitten in het overtuigen van mensen.”
Zijn computersimulatie die steeds krachtiger rekentuig vereiste, maakte de zaak er niet beter op. Do Livramento’s ‘redding’ was een visualisatieprogramma waarmee hij kon laten zien wat hij nu eigenlijk bedoelde. ,,Ik organiseerde een bijeenkomst met een aantal managers, en die waren sceptic as hell”, grinnikt hij. ,,Toen ik liet zien hoe ik de plaats en draaiing van flessen in een getransporteerde bulk kon bepalen, vroeg de hoofdmanager: ‘Wat is hier zo bijzonder aan, dat zie toch ik elke dag?’ Ik heb hem toen gefeliciteerd, want hij had daarmee mooi mijn model geverifieerd.”
Met zijn discrete element model kan niet alleen het bulkflessengedrag beschreven worden, maar ook de mate van scuffing van elke individuele fles. Gewapend met deze kennis kan een ontwerper van een transportsysteem van te vorenbepalen hoe erg de flesjes op een bepaald traject moeten lijden. Om dit te valideren gebruikte Do Livramento een camerasysteem dat onder andere de positie, rotatie, en snelheid van de flesjes kon meten. Tussen de voorspelling volgens het model en de eigenlijke meting bleek uiteindelijk slechts tussen de een en vijf procent verschil te zitten.
Poot
Doordat nu kon worden aangegeven waar de bottlenecks bij het flessentransport zitten, nam de animo bij de bierbrouwer weer even toe. Maar daarna werd het moeilijker. Do Livramento: ,,Toen ik aan het onderzoek begon, stond innovatie huizenhoog in het vaandel bij Heineken. Maar in de jaren daarna begonnen ze zich terug te trekken naar hun kerntaken. Ze waren nu eenmaal gewend alleen machinespecificaties op te stellen. Zelf iets ontwerpen is geen core business. Eind ’92 heb ik daarom het grootste deel van het onderzoek afgerond, maar het proefschrift was toen nog lang niet af.”
Afgelopen zomer pikte Do Livramento zijn onderzoek na een lang reces weer op. Hoewel zijn onderzoekstraject niet geheel pijnloos was, heeft hij geen spijt van zijn keuzes. ,,In de industrie vind je nu eenmaal de leukste opdrachten, maar commerciële bedrijven willen uiteindelijk gewoon geld verdienen. Als dat je niet aanstaat, moet je daar niet zijn. Waardevrije wetenschap bestaat nu eenmaal niet, zeker niet in de industrie. Maar als ik het nog een keer zou moeten doen, dan zou ik op dezelfde manier mijn poot stijf houden. Als je in elke vezel voelt dat je op de goede weg zit, dan moet je, zeker als onderzoeker, in die richting doorgaan. Daarvan heb ik, achteraf gezien, nog de meeste voldoening gehad.”
Het is dringen op de bottellijn, en bierflesjes komen daar niet ongeschonden uit. Uiteindelijk krijgen ze alle de bekende witgerande schaafwond. Het mechanisme achter deze scuffing is echter nooit goed beschreven, ontdekte dr.ir. Jan do Livramento.
Bottleneck
Bier is een kwestie van marketing. Maar van het zorgvuldig geconstrueerde sentiment dat bier omringt, is aan de bottellijn weinig te merken. Niks geen eeuwenoude receptuur die van generatie op generatie wordt doorgegeven. Bierproductie gebeurt op industriële schaal, en daarbij horen grote getallen. Een beetje productielijn wast, vult en kroont ruim twintig flesjes per seconde. De uurproductie van tachtigduizend pijpjes is daarmee ongeveer gelijk aan de jaarconsumptie van een grote studentenvereniging.
Om deze hoge snelheden te kunnen handhaven worden tussen de diverse onderdelen van een bottellijn bufferzones aangebracht, waarin duizenden flesjes tussen het wassen en afvullen door massaal in de wacht worden gezet. De toepassing van deze flessenbuffers is zo oud als het hoge-snelheidsbottelen zelf, en werd al in de jaren dertig geïntroduceerd door Coca Cola. Zo’n flessenzee in het gareel houden is echter geen sinecure, en het voortdrijven van de wachtende massa maakt ook nog een hels kabaal.
Doordat de flessen in de buffer voortdurend langs elkaar schuren, raken ze bovendien bekrast. Op zich geen ramp, maar omdat geretourneerde pijpjes voor het afvullen worden gereinigd met een zwak etsend reinigingsmiddel, tekent de ring van krasjes zich naar verloop van tijd af als een schrale, witte rand. Geen gezicht in de schappen, en ook nog eens slecht voor de sterkte van de fles. Dit proces heet scuffing, en houdt de bottelaars al decennia bezig. De technische levensduur van een fles zou namelijk tien jaar moeten zijn, maar wordt mede door scuffing bekort tot een jaar of zes. Hierdoor raakt Heineken per jaar ongeveer vijf miljoen gulden extra kwijt aan vervanging van het flessenpark.
Mist
Tot nu is er geen afdoende oplossing voor dit oude probleem gevonden. ,,De eerste artikelen over het onderwerp verschenen al in 1934 bij Coca Cola”’, weet systeem- en regeltechnicus dr.ir. Jan do Livramento, momenteel werkzaam bij Philips. Begin april promoveerde hij op een onderzoek naar bottelen bij hoge snelheden, dat hij als toegevoegd researcher deels bij Heineken uitvoerde. ,,Er is sindsdien natuurlijk wel aan gewerkt, maar de maatregelen tegen scuffing hielden nooit gelijke tred met de almaar hogere snelheden van de productielijnen. Zonder een bijzondere aanpak is dat vechten tegen de bierkaai.”
Om de scuffing tegen te gaan gebruikten bottelaars onder meerflesjes met een beschermende coating, en zochten zij hun heil in mildere schoonmaakmiddelen. Tevergeefs. Do Livramento: ,,Van die speurtocht is men onverrichter zake teruggekeerd. De oplossingen die men vond waren of onaanvaardbaar wegens toevoegingen als zink, of gewoon onbetaalbaar. Enzymen blijken bijvoorbeeld zes keer zo duur uit te vallen als loog, en werken lang niet zo goed.”
Dat alle pogingen om scuffing te voorkomen steeds op niets uitliepen vindt hij niet verwonderlijk. Het verschijnsel is volgens hem namelijk altijd verkeerd begrepen. ,,Bestaande modellen gaan uit van een hydrostatische benadering van scuffing. Begrijpelijk als je die stroom flesjes door de fabriek ziet kronkelen, want de analogie met een vloeistof is dan snel gemaakt. Maar als je het onderlinge krachtenspel tussen de flesjes bekijkt, dan blijkt dat je met deze aanpak ongelooflijk de mist in kunt gaan. Het aantal flesjes is veel te laag om het geheel als een vloeibaar medium te kunnen beschouwen.”
Dat klinkt logisch, want het draait tenslotte om bierflesjes. ,,Ja”, erkent Do Livramento, ,,maar met dit besef moet je de gebruikelijke aanpak wel helemaal overboord gooien. Je krijgt nu te maken met theorieën die je gewoonlijk tegenkomt bij aardwetenschappen, en niet bij systeem- en regeltechniek. Je zou het de kwantummechanica van de koude grond kunnen noemen.”
Onvoldoende begrip van het probleem speelde hem zelf ook parten tijdens zijn onderzoek. ,,Ik dacht in het begin nog dat het een regeltechnisch probleem was, waarbij je honderdduizend flesjes je wil probeert op te leggen. Maar de structuur en de geometrie van de bottelarij spelen hierbij een zeer grote rol. Uiteindelijk bleek het daarom meer een ontwerptechnisch probleem te zijn.”
Sceptisch
Toen ze bij Heineken hoorden welk pad Do Livramento was ingeslagen, was men daar opeens niet meer zo enthousiast. ,,Ze hadden natuurlijk liever gezien dat er een mooi besturingssysteem zou komen, en nu waren ze weer terug bij af”, verklaart hij. ,,Reacties als ‘is dit niet wat ver gezocht’ waren toen niet van de lucht. Men was waarschijnlijk bang dat het onderzoek op een zijspoor terecht zou komen. Dan kom je in een moeilijke positie als onderzoeker, want er gaat vreselijk veel tijd zitten in het overtuigen van mensen.”
Zijn computersimulatie die steeds krachtiger rekentuig vereiste, maakte de zaak er niet beter op. Do Livramento’s ‘redding’ was een visualisatieprogramma waarmee hij kon laten zien wat hij nu eigenlijk bedoelde. ,,Ik organiseerde een bijeenkomst met een aantal managers, en die waren sceptic as hell”, grinnikt hij. ,,Toen ik liet zien hoe ik de plaats en draaiing van flessen in een getransporteerde bulk kon bepalen, vroeg de hoofdmanager: ‘Wat is hier zo bijzonder aan, dat zie toch ik elke dag?’ Ik heb hem toen gefeliciteerd, want hij had daarmee mooi mijn model geverifieerd.”
Met zijn discrete element model kan niet alleen het bulkflessengedrag beschreven worden, maar ook de mate van scuffing van elke individuele fles. Gewapend met deze kennis kan een ontwerper van een transportsysteem van te vorenbepalen hoe erg de flesjes op een bepaald traject moeten lijden. Om dit te valideren gebruikte Do Livramento een camerasysteem dat onder andere de positie, rotatie, en snelheid van de flesjes kon meten. Tussen de voorspelling volgens het model en de eigenlijke meting bleek uiteindelijk slechts tussen de een en vijf procent verschil te zitten.
Poot
Doordat nu kon worden aangegeven waar de bottlenecks bij het flessentransport zitten, nam de animo bij de bierbrouwer weer even toe. Maar daarna werd het moeilijker. Do Livramento: ,,Toen ik aan het onderzoek begon, stond innovatie huizenhoog in het vaandel bij Heineken. Maar in de jaren daarna begonnen ze zich terug te trekken naar hun kerntaken. Ze waren nu eenmaal gewend alleen machinespecificaties op te stellen. Zelf iets ontwerpen is geen core business. Eind ’92 heb ik daarom het grootste deel van het onderzoek afgerond, maar het proefschrift was toen nog lang niet af.”
Afgelopen zomer pikte Do Livramento zijn onderzoek na een lang reces weer op. Hoewel zijn onderzoekstraject niet geheel pijnloos was, heeft hij geen spijt van zijn keuzes. ,,In de industrie vind je nu eenmaal de leukste opdrachten, maar commerciële bedrijven willen uiteindelijk gewoon geld verdienen. Als dat je niet aanstaat, moet je daar niet zijn. Waardevrije wetenschap bestaat nu eenmaal niet, zeker niet in de industrie. Maar als ik het nog een keer zou moeten doen, dan zou ik op dezelfde manier mijn poot stijf houden. Als je in elke vezel voelt dat je op de goede weg zit, dan moet je, zeker als onderzoeker, in die richting doorgaan. Daarvan heb ik, achteraf gezien, nog de meeste voldoening gehad.”
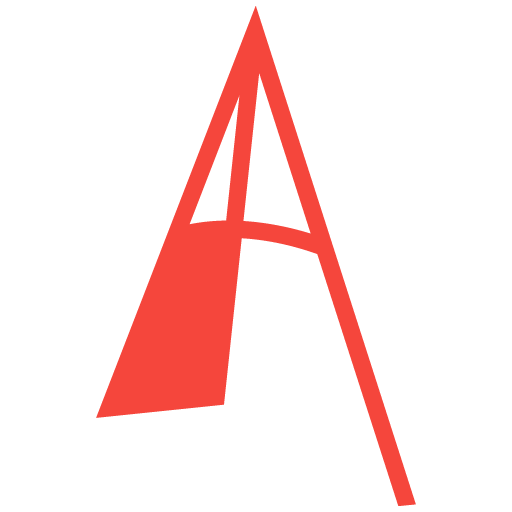
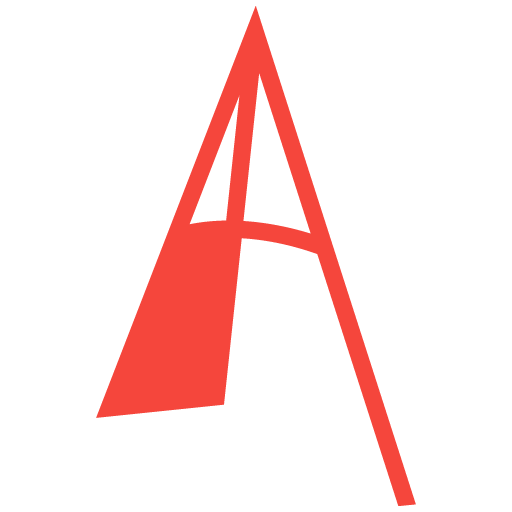
Comments are closed.