30,000 Colombians are missing a leg and, to make matters worse, it’s very difficult for amputees to get a prosthesis.
This fact was the starting point for six students from three departments at Industrial Design and Engineering who are collaborating on a Joint Masters Project (JMP).
The aim of the project is to design a product-service system that will provide a better fitting prosthetic, more quickly and at a lower price.
Using €3,000 raised through a crowdfunding project and extra financial support from the ProPortion Foundation, the TU Delft team flew to Colombia. There they talked to many amputees as well as hospital technicians and university medics. “We learnt that diabetes is the main reason that so many people lose their legs, followed by traffic- and work-related accidents, and of course land mines”, said Lyla Kok, who is studying Integral Product Design.
Currently a prosthetic leg costs around €1,400 in a country where the average salary is about €250 per month. In addition, the process of getting one made is extremely time-consuming. “Amputees often have to travel hours by bus to get to the city and then need to stay there for two weeks while their prosthetic is made”, said Jennifer Brown, who is studying Strategic Product Design. “In a country with many single mothers of large families living in remote areas, a trip to the city is often impossible”, added Kok.
With the goal of improving accessibility, affordability and even the fit of each prosthetic, the TU Delft team has come up with a new product-service design. Essentially the socket of the new leg is manufactured directly on the leg stump meaning a much better and faster manufacturing process: one day instead of two weeks.
First the team developed new materials to replace the traditional plaster; for example, Protoplast, which has a liquid/Vaseline structure when warmed but which hardens within minutes. Once the clinical technician has applied this material, the patient steps into a closed water system with an adjustable level. The leg then sinks in to the required height in the middle of the knee. This means that the patient can stand with his whole weight on the leg, mimicking happens when a person walks.
The water naturally distributes itself around the end of the stump, in the way that soft tissue i.e. muscle would do, leading to a much better fit and a more comfortable socket. “This is different from the current system of prosthetic manufacturing because it also allows the patient’s weight – and therefore the pressure points – to be taken into account’, said Kok.
Another great advantage of this system is that it is portable and can therefore be much more accessible to people in remote areas. This coming summer this new product-service design will be tested as a social business concept within the Colombian healthcare system.
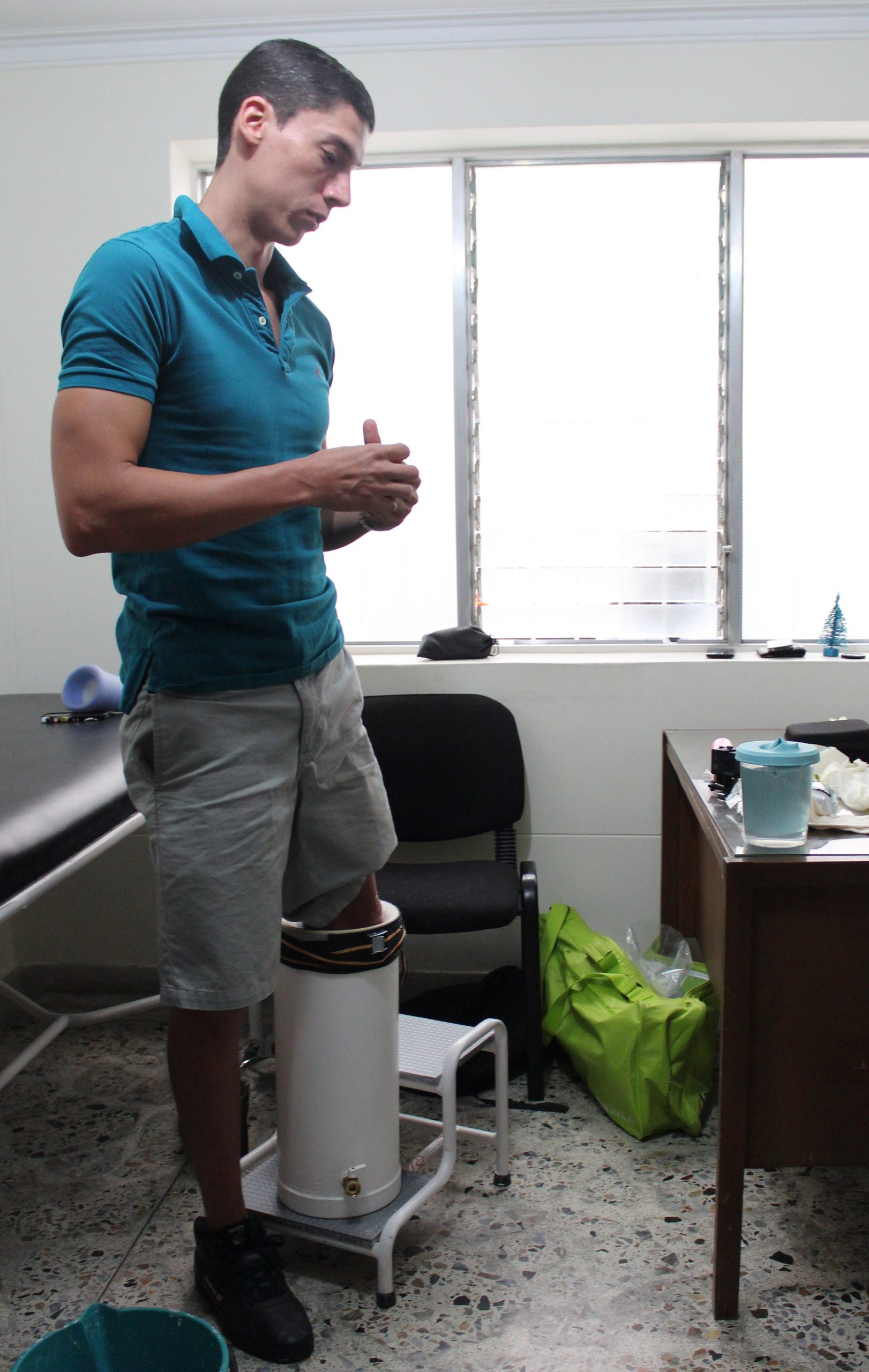
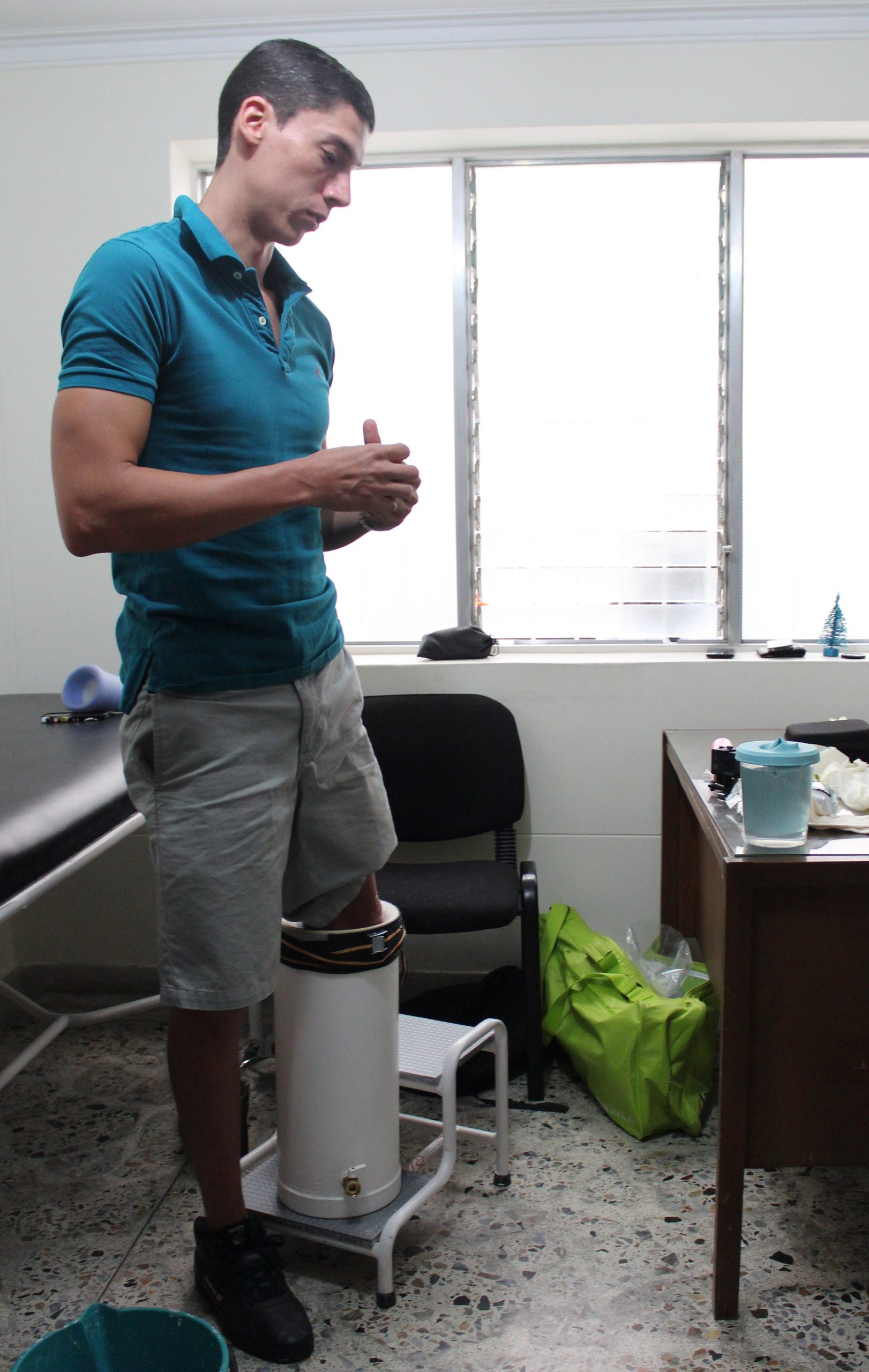
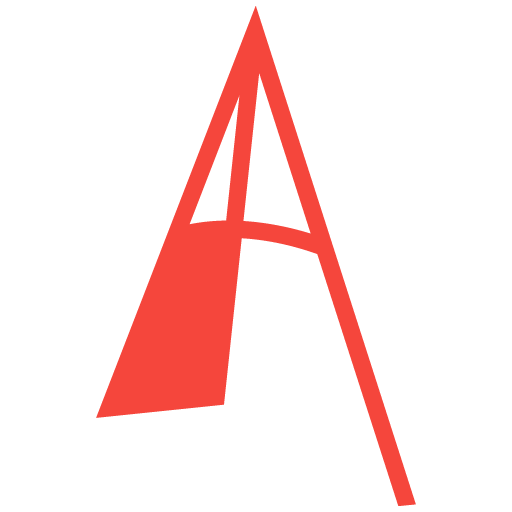
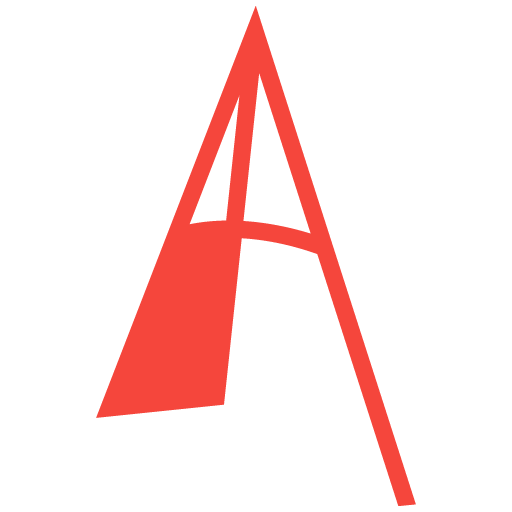
Comments are closed.