Artificial intelligence is this year’s theme at TU Delft. Delta highlights six AI studies. Part 2: how to optimise composite structures with AI.
Illustration generated by AI. (Image: New Media Center with Adobe Firefly)
Using AI to ensure that you can calculate the strength of a composite material much faster. The Delft-based SLIMM lab is using artificial intelligence to develop models to achieve this. With this, wind turbine builders want to optimise design and production of wind turbine blades that get bigger every year.
The SLIMM lab models composite materials, such as fibre-reinforced epoxy, that are used for airplane wings and wind turbine blades. These materials need to be both extremely lightweight and very strong. But their internal structures also make these materials complex. A video of blade manufacturer LM Wind Power shows how half a blade is made: an immensely long mould is sprayed with a gel coating, and is then covered with multiple layers of glass fibre, carbon, balsa wood and foam before being saturated with resin. After the composite material has hardened, two halves are combined into one blade. Because of these complexities, manufacturers tend to play it safe and make their products reliable but perhaps not as light as they could be.
“There are two ways to study the strength of composite materials. And neither works in practice,” says Dr Iuri Rocha with a smile. “Experimental testing doesn’t really work because of the number of different fibre orientations and layering of fibre mats. These endless variations basically make it impossible to test every possible composite material combination experimentally.” The other way would be by applying computer simulations on a microscopic scale, the so-called finite element modelling (FEM). But to scale up from micrometre scale to the size of a bridge or an airplane wing implies using many millions of elements. “Then you very quickly get to a point where your model takes several weeks to run. And that is for a single model. So to get answers to real research questions, you need to run several of these models. And to design a new material, you need to run thousands of these models. So, then it becomes impossible.”
That’s where AI comes to the rescue. SLIMM lab develops surrogate AI models, which are substitute models for the actual finite element models, and need a hundred thousand times less computer runtimes. “We train the machine learning model with the data from the original expensive FEM model. Once it’s sufficiently trained, we can use it to predict scenarios very quickly,” Rocha explains.
Variants are a hybrid model that combines physical modelling and machine learning to reduce training, and probabilistic machine learning (Bayesian, as it’s called) that produces a probability distribution rather than a definite outcome.
Both variants (Bayesian and hybrid) were developed to make the AI models more transparent and reliable. “People who build surrogate models tend to trust them blindly,” says Rocha. “But I think that you need some measure of uncertainty as well.”
Of course the project comes with its challenges, Rocha says. He mentions the work-intensive training of the models: the selection of the data and the time it takes to train the model. Besides, he fears that the introduction of generative AI applications such as ChatGPT will make AI models more opaque. No one knows how the outcome was produced in these models and how reliable it is. The opaqueness of AI models will even increase as Google and Microsoft develop their own generative AI variants, all shrouded in corporate secrecy. “It’s important that engineers have a good idea of how the design came about,” Rocha emphasizes. If opaque models dominate the market, there is a risk that the industry will mistrust all AI models and throw out the baby with the bath water.
Ever the optimist, Rocha strives for a different result. “The ideal outcome for me is that we come up with a set of techniques that makes high-fidelity simulations of materials seamless, user-friendly, and extremely fast. And in a way that can be easily shipped to industry.” This would enable the industry to optimise the production of wind turbine blades which, as we know, grow taller every year.
- SLIMM stands for ‘AI for Smart Materials Modelling’. Dr Iuri Rocha is the Artificial Intelligence Programme Director at the Faculty of Civil Engineering and Geosciences and his counterpart at the Faculty of Electric Engineering Mathematics and Computer Science is Dr Hanne Kekkonen. They work with four PhD candidates and two members of the faculties.
- There is more information on the SLIMM lab website.
- Also read part 1 of this series: Robots that navigate like humans
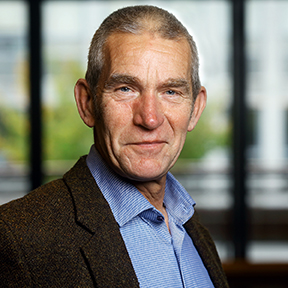
Do you have a question or comment about this article?
j.w.wassink@tudelft.nl
Comments are closed.