Non-cemented stacked blocks of stone and concrete bridge the waterway to The Green Village. The prototype reusable arch bridge is being field tested here for five years.
A new modualr arched bridge made from reused materials offers acces from the campus to The Green Village. (Photo: Robèrt Kroonen)
What is the similarity between housing development, water storage and obsolete bridges? All three are reasons that planners are expecting a growth in the demand for bridges in the coming years – an estimated 100,000 over the next few decades.
For bridge designers Ate Snijder and Rob Nijsse (Faculties of Architecture and the Built Environment and Civil Engineering and Geosciences respectively), the expected growth was a reason to look at whether the production of fixed bank connections could be done differently and more sustainably. At the moment, a cycle of construction and demolition of one-off projects is still standard practice. Nijsse and Snijder aim to make bridge construction more sustainable (with less CO2 emissions), circular (from recycled materials) and modular (reusable blocks). Snijder presented the prototype of their circular and modular arch bridge to the press and public on Tuesday 19 March.
For the building blocks, Snijder and Nijsse used three different materials. The outer and thickest blocks are made of leftover geopolymer concrete; a mixture of alkaline, blast furnace slag; and, coal fly ash as a binding agent. Geopolymer concrete production releases much less CO2 than ordinary concrete production, plus it converts waste materials into construction material.
The next few metres are made from recycled concrete. Circuton, as it is called, is composed of gravel, sand and cement derived from concrete pulverised on site. Circuton avoids CO2 emissions from cement production (one tonne of CO2 per tonne of cement) and transport.
The colourful bricks in the middle of the bridge consist of crushed brick, sinks and toilet bowls, which is reflected in the different shades.






Like the Romans
“We built the bridge much like the Romans did,” says BAM project leader Bas de Jong. First, BAM built a wooden arch on which the 206 stones were stacked dry – i.e. without cement. Their S-shaped profile make the blocks interlock. Once the bridge was under pressure – the two ends were pressed together – the 27 tonne unit could be jacked up and lifted into place. This the Romans could not do.
The bridge was placed between two end pieces or ‘menhirs’ made with a 3D concrete printer. The menhirs also guide the steel cables that act as railings.
The bridge is fitted with measuring stickers and will be regularly checked for settlement in the coming period. The makers expect the bridge to still sag slightly. The bridge will remain in place for five years, just like the glass bridge that preceded it. The Green Village acts as a field lab – a test site to find out how a conceived idea holds up in real life.
“If the circular arch bridge proves stable, it could offer a sustainable alternative to the one-off bridges that are currently the standard,” Snijder told the audience at the presentation. The arch bridge’s construction material is circular and can be reused in other places with other spans and widths. The developers estimate the maximum span at 25 to 30 metres and the construction time at about three weeks. They do not yet dare comment on comparative costs.
However, Snijder and his colleagues are working on creating a calculator that they can make available to municipalities. Civil servants can use it both to put together their own circular arch bridge, and to immediately see the CO2 emissions associated with the construction and costs.
Watch the construction in 4 minutes
- Also read: The Green Village on Circular Arch Bridge (in Dutch)
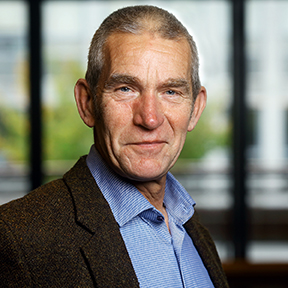
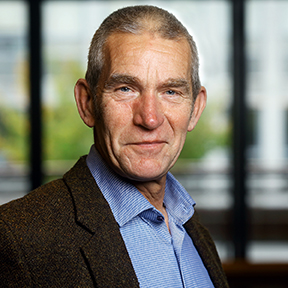
Do you have a question or comment about this article?
j.w.wassink@tudelft.nl
Comments are closed.