Pacemakers run out of batteries after around 7 years, so wearers undergo several open-heart operations during their lifetime to replace them. The solution? The heart itself.
Nima Tolou: "Developing the pacemaker is not only about economics, it is about people too." (Photo: Nina van Wijk)
Read what Delta wrote about Nima Tolou’s mechanical watch:
Made in Delft: the most accurate mechanical watch ever
or read this article about the Engineer of the Year award (Dutch only)
Delftse onderzoeker wint Prins Friso Ingenieursprijs
With every heartbeat, the powerful heart muscle contracts and relaxes, and this produces a lot of kinetic energy. Dr Nima Tolou, Assistant Professor at the Department of Precision and Microsystems Engineering (3mE Faculty), saw an opportunity in this power.
Tolou and his team work on motion-energy harvesters which capture motion and vibrations from their environment and convert these into electricity. Using this technique, Tolou and his team already revolutionised mechanical watches.
Now, they are working on revolutionising pacemakers. When pacemaker batteries run out, for safety reasons the entire pacemaker is replaced. This requires open-heart surgery, which is risky for the patient and has a price tag of around EUR 70,000. Tolou decided to harvest the power of the heart itself to power the pacemaker. With every beat, a built-in motion-energy harvester will convert kinetic energy to electric power for the pacemaker.
In March, Tolou received the Engineer of the Year award for his work on societally relevant challenges and using technology to solve them. Strong values are at the heart of his work, Delta editor Nina van Wijk discovered when interviewing Tolou.
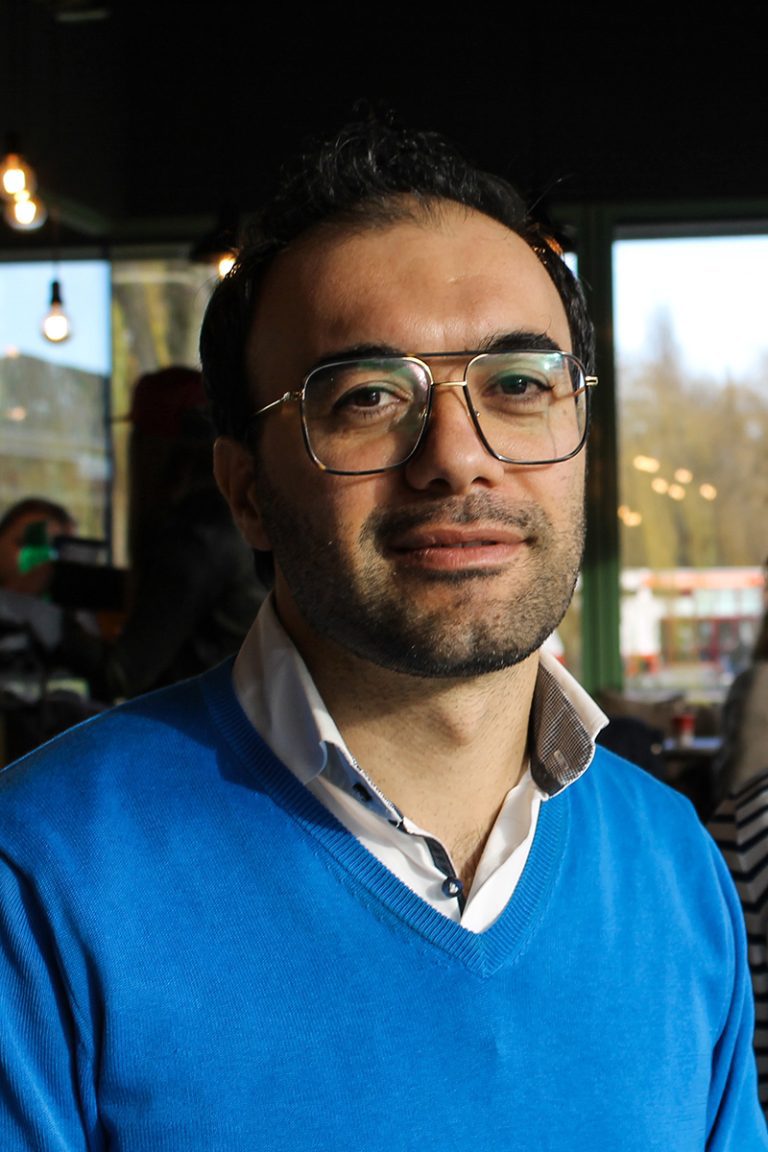
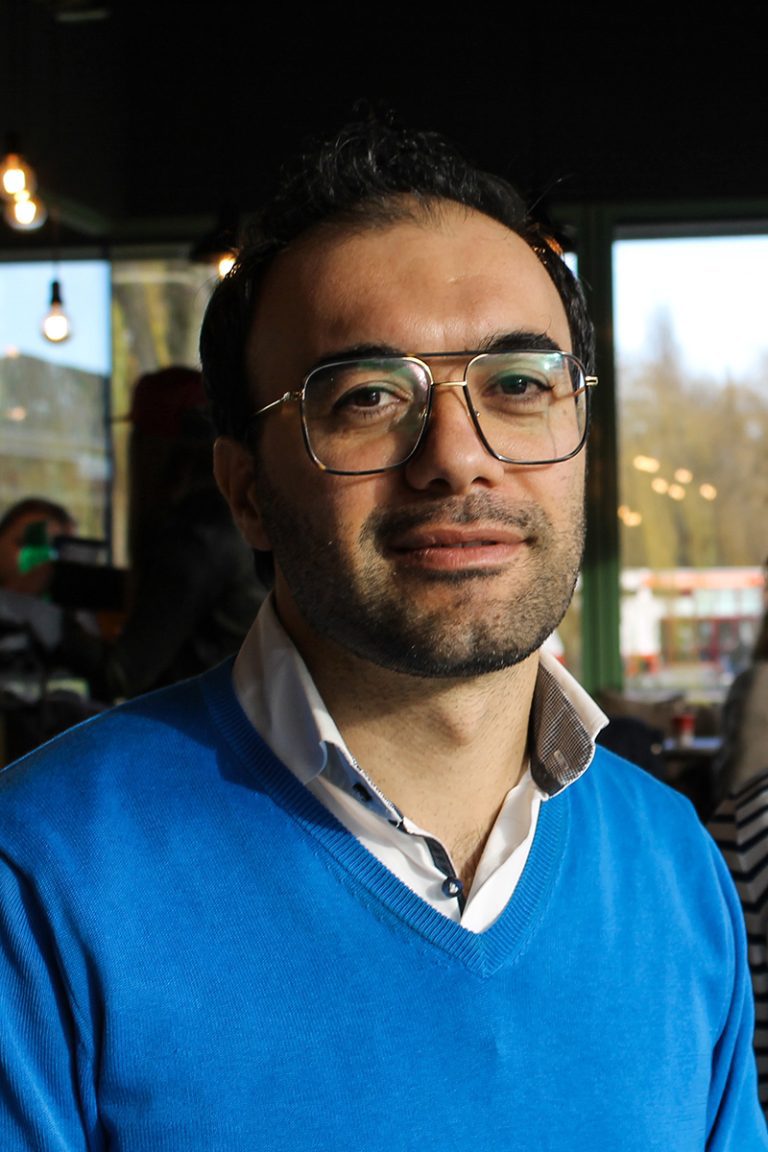
In March you received the Engineer of the Year award. How did this award influence your work?
“The award was a confirmation of the quality and impact of our work. Afterwards we received a lot of attention, sponsorships, offers of grants and interest from industry. However, what was more interesting was that we became more focused, especially on the societally relevant challenges and the values of our work.
One of our fundamental values is that we work for people. Some people do science for science, we do science for people. In 20 years, the science will just be for curiosity. There’s nothing wrong with that, but I realised what a joy it is to help people, reach them and improve their lives. The pacemaker is one way in which we can do that.”
Why is developing the pacemaker important for you?
“Pacemaker replacement is a really big problem for the patient. When I got the Engineer of the Year award, I received an email from a former colleague. He said that he was really excited that I was still working on the pacemaker because he has one and its battery ran out after six years. He had to undergo open-heart surgery to get a new pacemaker, but his body rejected it. So he had to have a second operation to get another pacemaker. This email was so rewarding. I saw it as an example of solving societal problems. Seeing a person, a colleague, suffering and being worried is not nice. Developing the pacemaker is not only about economics, it is about people too.”
What is the biggest challenge in producing the pacemaker?
“The main challenge is that the pacemaker must not fail. It is a medical device so it must be highly reliable. To give you an example, a small crack in the device can lead to significantly less power. It doesn’t matter that the pacemaker works really well, if you still have to replace it after one year because of a micro-crack.”
How do you ensure reliability?
“We test the pacemaker by giving it shocks, for example. We improve its shape, material or packaging. All of these things sound simple, but each could be a whole PhD in itself.”
How do you approach this task?
“We use the same approach as with our watch. It was a crazy concept, but it became a remarkable product. We make sure that we know the main issues that we have to address for people to use the product and for industry to manufacture it. These are really our main challenges. Production is an issue. You want to ensure that the idea can be introduced into real life and that people can ultimately use it. Otherwise it would just remain a concept. And if you cannot produce the product, there is no point in designing it.”
When will the pacemaker be in use?
“It could easily take 10 years. Medical devices take a very long time to produce because of all the safety regulations. In 2.5 years, we hope to have the first prototype ready to prove that the technology works. Then, we will test it in an appropriate environment, maybe in a lab. After that, we will do the first production where we will test the first generation of the product.”
You’ll need a lot of patience. How do you stay motivated?
“Working values are really important. What we do is not important, why we do it is important. The ‘why we do’ is really great in our team, and it guides all our research. That’s why we won the Engineer of the Year award. That was not my own achievement, it was a team effort. Our motivation comes from the heart, it’s why we work till we sweat. It’s our drive.”
Want to read more?
Made in Delft: the most accurate mechanical watch ever
Delftse onderzoeker wint Prins Friso Ingenieursprijs (Dutch only)
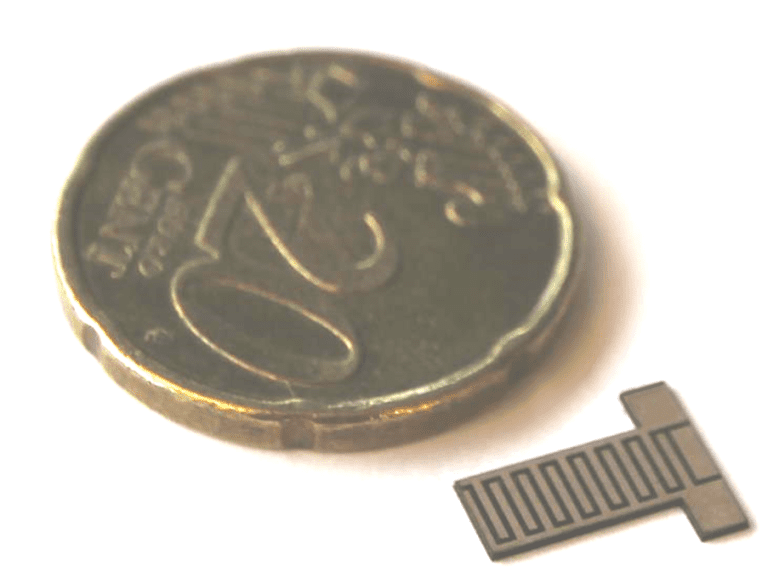
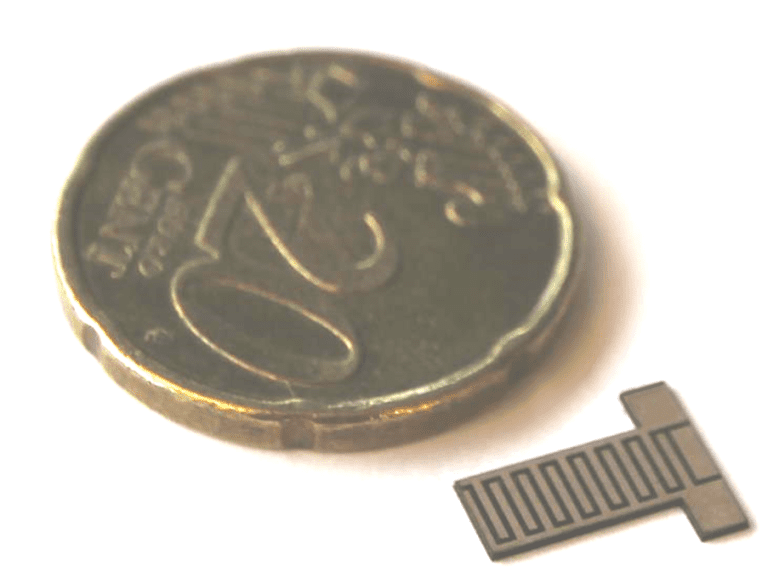
Nina van Wijk / science editor trainee
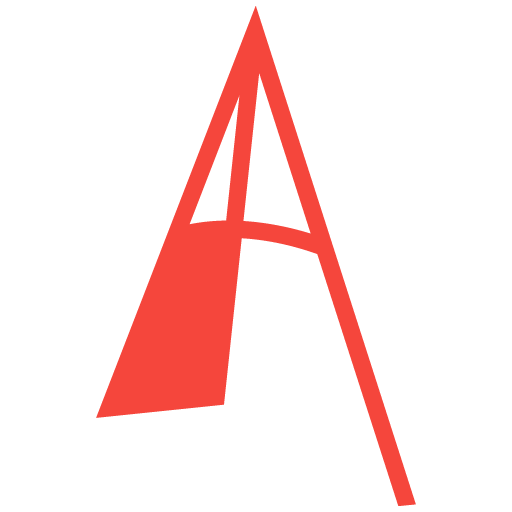
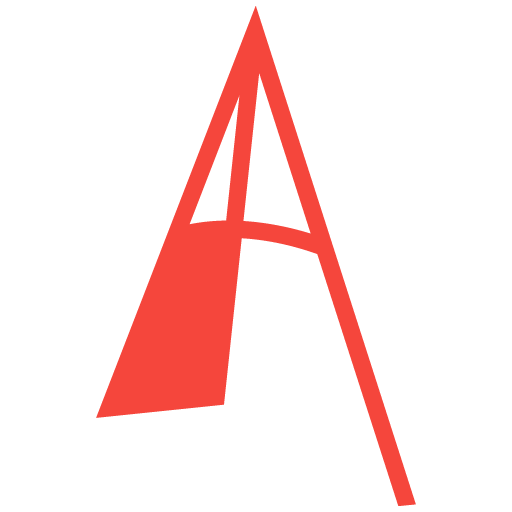
Comments are closed.