Electrolysis research at 3mE took second place in ‘KIJK’ magazine’s best tech ideas. The research is important in producing green hydrogen.
Araz Sheibani Aghdam and Willem Haverkort discuss a test set-up in the process & energy lab. (Photo: Jos Wassink)
Research into electrolysis – using electricity to separate water in hydrogen and oxygen – is on the cards again. Six years ago Physicist Dr Willem Haverkort started as a tenure tracker at the Process & Energy Department at the Faculty of Mechanical, Maritime and Materials Engineering (3mE). He saw that interest in electrolysis rose as the term ‘green hydrogen’ became more frequently used.
‘Green hydrogen’ is hydrogen that is generated using sustainably generated power. At present, this does not even account for even 1% (in Dutch) of the total market.
Nevertheless, green hydrogen is key in many sustainable energy scenarios. The Dutch Government views hydrogen as a universal raw material for industry, and a future fuel for households and cars. The Climate Agreement calls hydrogen a suitable medium for storing excess solar and wind energy in salt caverns or empty gas fields for winter storage.
Giving green hydrogen a meaningful role requires technical improvements and an unknown expansion of the electrolysis capacity. From the current 1-10 megawatts, the Climate Agreement wants to go to 500 megawatts in 2025 and to 3-4 gigawatts in 2030. TNO writes about ‘a factor of a thousand’ in seven years’ time.
Small-scale materials research for electrolysis in the process & energy lab. (Photo: Jos Wassink)
Banished
Michael Faraday discovered electrolysis about 200 years ago, and little has changed in industrial applications (mining metals and producing chlorine) over the last century. Haverkort notes that it is only in the last year or so that publications have appeared about new methods and materials to convert power into hydrogen more efficiently. ‘After years in scientific banishment, it is suddenly undergoing research again in chemical laboratories’, observed the ‘NRC’ newspaper (in Dutch) recently.
‘KIJK’, the popular scientific weekly, also observed this. ‘The reason that we put this idea (Haverkort’s research, Eds.) on the longlist is that hydrogen should play a role in the energy transition. So we have written a few articles about this promising gas.’
The jury members who selected the best ideas from the longlist and ranked them wrote: ‘Good work and very relevant’ (Jim Heirbaut, Editor at ‘De Ingenieur’) and ‘If it works out, the impact will be gigantic given the high energy costs/efficiency loss of current production methods. There is also a very big market for this type of solution.’ (Jacqueline van den Ende, co-founder of Carbon Equity).
The principle of electrolysis has been known for nearly two centuries. (Animation: Jos Wassink)
School test
The principle behind electrolysis is simple and easy to see in a popular test in secondary school classes. The teacher makes water conductive by adding some baking powder or potassium hydroxide and inserting two electrodes connected with a DC voltage source into it. A cloud of hydrogen gas (2H2O + 2e -> H2 + 2OH–) will emerge in the negative pole and oxygen (O2) will bubble upwards in the positive pool. If you remove your finger from a hydrogen-filled test tube next to a flame, the tube will briefly emit a whistling sound. But the mixture of hydrogen and oxygen forms oxyhydrogen which can explode easily. This must be avoided.
A separation between the electrodes will prevent the hydrogen and oxygen from mixing. However, a membrane or separator has a high electrical resistance, explains Haverkort, and this leads to losses in the conversion of electricity to hydrogen gas.
Researcher Willem Haverkort develops electrolysis without a separation membrane. (Photo: Jos Wassink)
Can it also be done differently?
Haverkort’s equally radical and simple idea is to use flowing water to remove the gas bubbles that are made by the electrodes. This makes a membrane redundant. The porous electrodes allow the water containing the gas bubbles to flow from the inside outwards.
Draining the gas bubbles and removing the membrane helps reduce the electrical resistance. What also helps is reducing the distance between the electrodes. “This is especially important if you want to use waste water to generate green hydrogen,” says Haverkort. His research group is part of a European consortium that will spend the next four years designing the technology to generate green hydrogen from sustainably generated power and waste water.
Haverkort believes that a microfluidic system (a type of chip with a fine network of liquid channels) can help minimise the distance between the electrodes. Apart from this, he has another trump card: by placing the electrolysis under high pressure (at around 10 bar) the gas remains in the solution. Only when the pressure is reduced is it released, just like when you open a soft drink bottle.
Gas factory
Large scale, micro structures, and high pressure. What will a modern electrolyser look like? Haverkort thinks about a lot of identical setups where water flows through thousands of microfluidic systems under high pressure. He envisions that a future modern hydrogen factory could closely resemble a data centre because of the endless repetition of this high tech setup. “The goal is within four years.”
‘How will we upscale cheaply and safely?’
The European Pathfinder project is an attempt to catch up with China. At the beginning of this year, Baofeng Energy surprised the energy world with a unit that converts 150 megawatts of solar energy into green hydrogen. Six months later, Sinopec, the Chinese oil concern, announced a unit twice the size due in mid-2023.
According to TNO, the Netherlands is looking to scale up by a factor of a thousand by 2030. In his Hydrogen Europe plan, TU Delft Energy Professor Ad van Wijk (who also works at the Faculty of 3mE) analyses the European situation. He estimates an electrolysis need of 40,000 megawatts in Europe and another 40 gigawatts outside Europe by 2030. This is more than 500 times China’s biggest factory to date. In only seven years.
The secondary school test is thus under pressure to quickly grow into an efficient mass technology. The contour lines are starting to show: microfluidic reactors, large scale, cheap materials, flowing water and waste water, and high pressure. And who knows what more will be discovered. “The core question is how will we upscale this cheaply and safely?” says Haverkort.
Read more:
- Haverkort continuously reports on his research in a weblog.
- Green hydrogen brings electricity and gas together (Delft Outlook, December 2020)
- Optimising hydrogen production using electrolysis (TNO)
- Hydrogen Europe plan (download) (Prof. Dr. Ad van Wijk, Jorgo Chatzimarkakis, 2020)
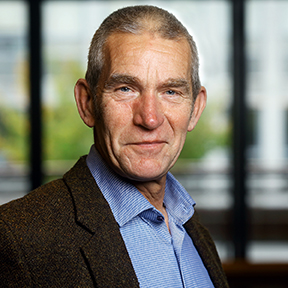
Do you have a question or comment about this article?
j.w.wassink@tudelft.nl
Comments are closed.