The Bioprocess Pilot Facility (BPF) at the Biotech Campus Delft added another two halls last week. One hall is for the pre-treatment of biomass, the other for the production of food grade materials like enzymes or sweeteners.
The two halls are complementary to the existing two facilities for fermentation and downstream processing (drying, filtering or distilling to obtain the fermentation product), said BPF’s director Hans van Leeuwen. These halls opened in May 2012.
Last week, Van Leeuwen pushed a button that kick started the new pre-treatment installation for wood chips and opened the remaining facilities for an audience of 250 people. BPF is now an open access facility for scaling up bio-production processes. Clients can test and optimise processes that convert biobased residues into chemicals, fuels and ingredients for food and pharma.
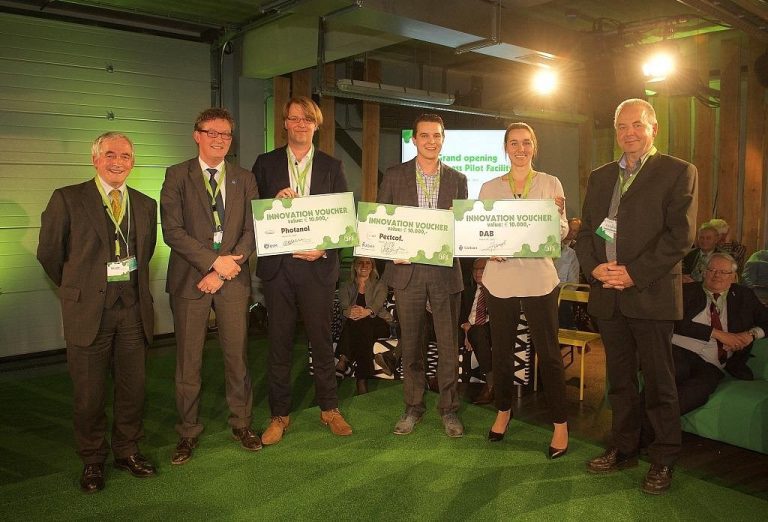
Three start-up companies (Photanol, DAB and Pectcof) presented their pitches in the competition for a 10,000 euro voucher that they could spend in the pilot facility. The jury thought all the ideas were equally outstanding and decided to grant all three contestants a 10,000 euro innovation voucher.
The facility is the intermediate step in between lab and industry, said Van Leeuwen. Upscaling a process from the lab to the industrial level typically takes half a year, with three or four sub-processes that require three to four weeks each.
The BPF on the former DSM grounds may also be used to optimise existing industrial processes by downscaling it to the BPF scale, tweaking the process for optimal results, and adapting the full-scale process accordingly.
The pre-treatment and food-grade halls are the last large components in the plan for a green pilot factory. Professor Luuk van der Wielen (director of BE-Basic and professor of biobased economy at the TU) presented the plan in 2010.
BPF’s shareholders are the TU, DSM and Corbion (a biobased firm that produces lactic acid). Ministries, local and regional development funds have supported the plant with ten of millions of euros in subsidies.
See also:
TU maakt begin met groene proeffabriek (31 May 2010)
BPF opened (23 May 2012)
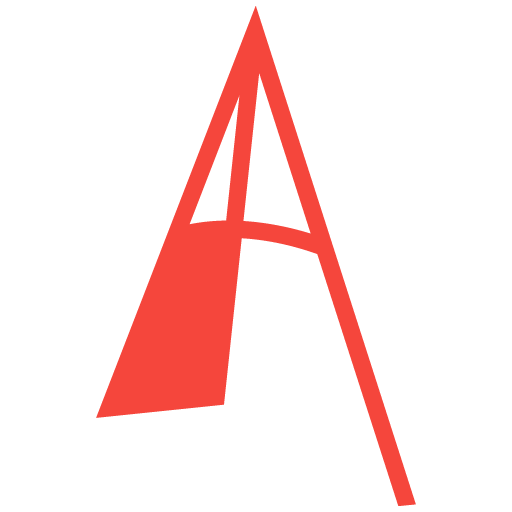
Comments are closed.