Porous concrete is the best choice for external walls, finds Dr. Ahmed Hafez, but costs and conservatism are holding back its use in the building practise.
Nearly a hundred years after its discovery autoclaved aerated concrete (AAC) has been (re)discovered as the most suitable building material in Egypt as well as the Netherlands. “I was surprised as well,” said PhD candidate Ahmed Hisham Hafez.
The material, also known as porous concrete, aircrete or by its brand name Ytong, was invented in Sweden in the early 1920’s. It is a highly thermally insulating concrete-based material used for both internal and external construction. Besides its insulating capability, one of its advantages in construction is its quick and easy installation, because the material can be routed, sanded, or cut to size on site using standard carbon steel power tools. It was a popular building material in the 1970’s in Europe. Since then the production in Europe has slowed down considerably, but the industry is growing rapidly in Asia due to strong demand for housing and commercial space. According to Wikipedia, China, Central Asia, India, and the Middle-East are the biggest in AAC manufacturing and consumption.
For his PhD research, Hafez screened nine different building materials by criteria like construction time, construction costs, the energy needed for the production, CO2-emission, construction techniques and operation energy. He allotted different weights to the criteria for Egypt and the Netherlands, and yet the same material came out as the winner: aerated concrete.
In Egypt, it was the insulation value and the low weight that made the difference. A 25 cm thick wall from aerated concrete means less air-conditioning is needed and thus, the operation energy goes down. Thanks to the light weight, there is also a reduction in building time and hence labour costs.
In the Netherlands, the prime advantages of AAC are its low embodied energy (energy needed to produce the material), the low CO2-emission, its recyclability and the relatively thin walls (32 cm).
Why then has the material fallen out of grace? Hafez blames cost reduction and conservatism. He says that builders tend to focus on the lowest construction costs, which leads them to choose calcium silicate blocks with a traditional layered insulation. And because calcium silicate has become the default choice, builders and engineers tend to stick to the safest and tried option.
Another unknown is the acceptance by the prospective house-owners. AAC walls will feel less hard and sturdy than say concrete. A drill or a nail enters easily, but longer and thinner screws will be needed when fitting cabinets and wall hangings.
Ahmed Hisham Hafez, Integrating Building Functions into Massive External Walls, PhD supervisor Prof. Ulrich Knaack (BK), June 6, 2016.
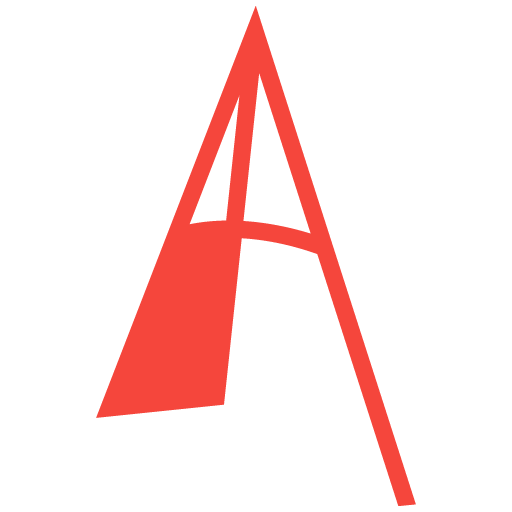
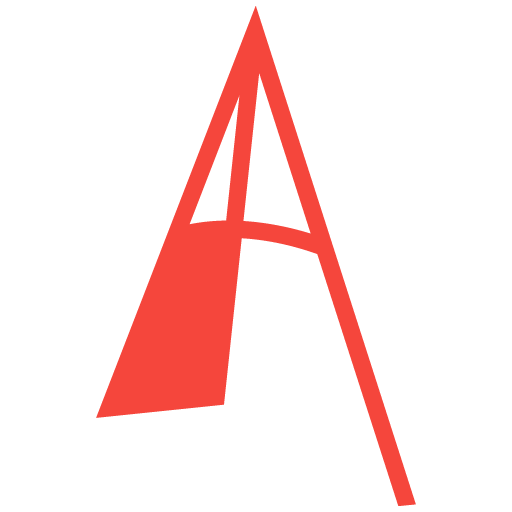
Comments are closed.