Europe is entirely dependent on imported metals for its electrical products. The group of TU Delft’s recycling expert Peter Rem is working to change this by developing new technologies as part of an EU programme.
Researchers Lin Wang and Max van Beek (on ladder) install the MDS machine that separates electronics components based on their density in a continuous process. (Photo: Thijs van Reeuwijk)
There are crates full of circuit boards waiting for processing in the Faculty of Civil Engineering and Geosciences’ recycling lab. They come from radios, televisions, amplifiers, telephones and computers. Doctoral candidate Max van Beek has become a real expert. He pulls a set of circuit boards full of transistors, capacitors, resistors and chips from a crate.
“Look at this, circuit boards used to be made of paper and are beige. Modern circuit boards are now green. They are made of fibreglass. Components like resistors, capacitors and transistors are becoming ever smaller over time. But chips are becoming ever more abundant and bigger.”
Circular Economy
Many of the components contain small amounts of rare and valuable metals such as gold, silver and palladium. Most of these raw materials are sourced outside of Europe. Innovation in recycling is needed to reduce that dependency on non-European countries. This is the rationale for the European PEACOC (Pre-commercial pilot for the efficient recovery of Precious Metals from European end of life resources with novel low-cost technologies) programme.
Innovative separation technology can increase the concentration of valuable metals in electronic waste, creating greater value and less waste. Innovative separation technology is the expertise of recycling expert Prof. Peter Rem (Faculty of Civil Engineering and Geosciences). He is the promotor of Max Van Beek who, along with post-doc Dr Lin Wang, carries out research in the recycling lab.
Rem’s group is one of 19 partners involved in the PEACOC research group as part of European Horizon2020 that is working on developing ‘unique, economical and environmentally friendly technologies for the efficient extraction of gold, silver and platinum from waste’, states the website. The research programme started in 2021 and will continue until April 2025. As part of the collaboration, TU Delft designed the magnetic density separator (MDS). More on this later.
Mountains of waste
How much electrical and electronic equipment at European scale are we actually talking about?
- The amount of equipment with plugs or batteries sold in Europe every year has increased from 7.6 million tonnes in 2012 to 12.4 million tonnes in 2020, reports Eurostat, the European statistics agency. This is almost 28 kilogrammes for each inhabitant.
- The amount of electrical and electronic equipment collected over this same period rose from three million tonnes to 4.7 million tonnes a year (10.5 kilograms per inhabitant of Europe) and thus remains somewhat lower than the amount purchased.
The European Union hopes to collect more electrical and electronic waste.
- In 2016 the target was to collect 45% of the weight of what had entered the market in the three previous years.
- From 2019, that target rose to 65%.
- In reality, in 2020 the collected average in Europe was 45% (the target of four years prior to that).
- In 2021 in the Netherlands, the amount of electrical and electronic waste collected amounted to 11.75 kilograms per resident. This is a little more than the European average of 11 kilograms per resident per year.
Extraction
What can the Netherlands do with 200 million kilograms of electronic waste per year? Extracting valuable metals only works if the value of the metals in the electrical/electronic waste is higher than the costs of recovery.
It is for this reason that Peter Rem and the recycling industry are working on new technologies to increase the concentration of valuable materials in electrical and electronic waste.
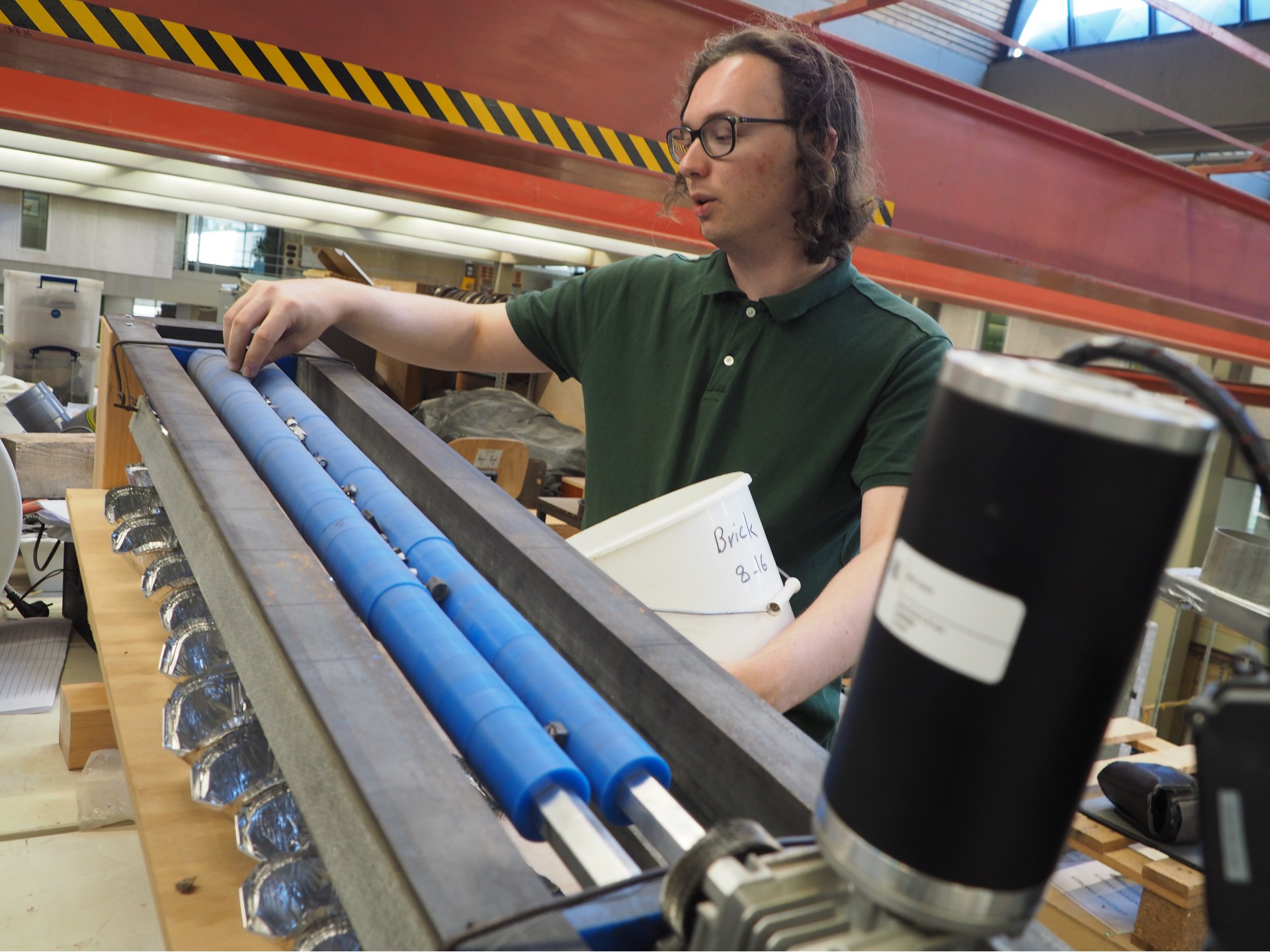
Enriching
Doctoral candidate Max van Beek gives a demonstration. He starts with a bucket containing one kilogram of capacitors, coils, resistors, and other electronic parts. They were taken from the circuit boards that he showed earlier.
About 10% of the material in the bucket consists of precious metals, says Van Beek. There then follows a series of various separation technologies to increase the concentration of valuable materials.
- Sifting.
- Roller sorting: the components drop between two turning cylinders according to their thickness.
- Magnetic separation: a slanted permanent plate magnet draws the components to a conveyor belt. The more magnetic the components, the further they go.
- Magnetic density separation.
At the end of the process, only 150 grams is left of one kilo of electric and electronic waste, of which 96 grams is precious metals. This is 64% of the total. Separation technologies have increased the concentration by 10% (in the bucket) to 64% (at the end of the process). “This is a factor of 6.4,” says Van Beek proudly.
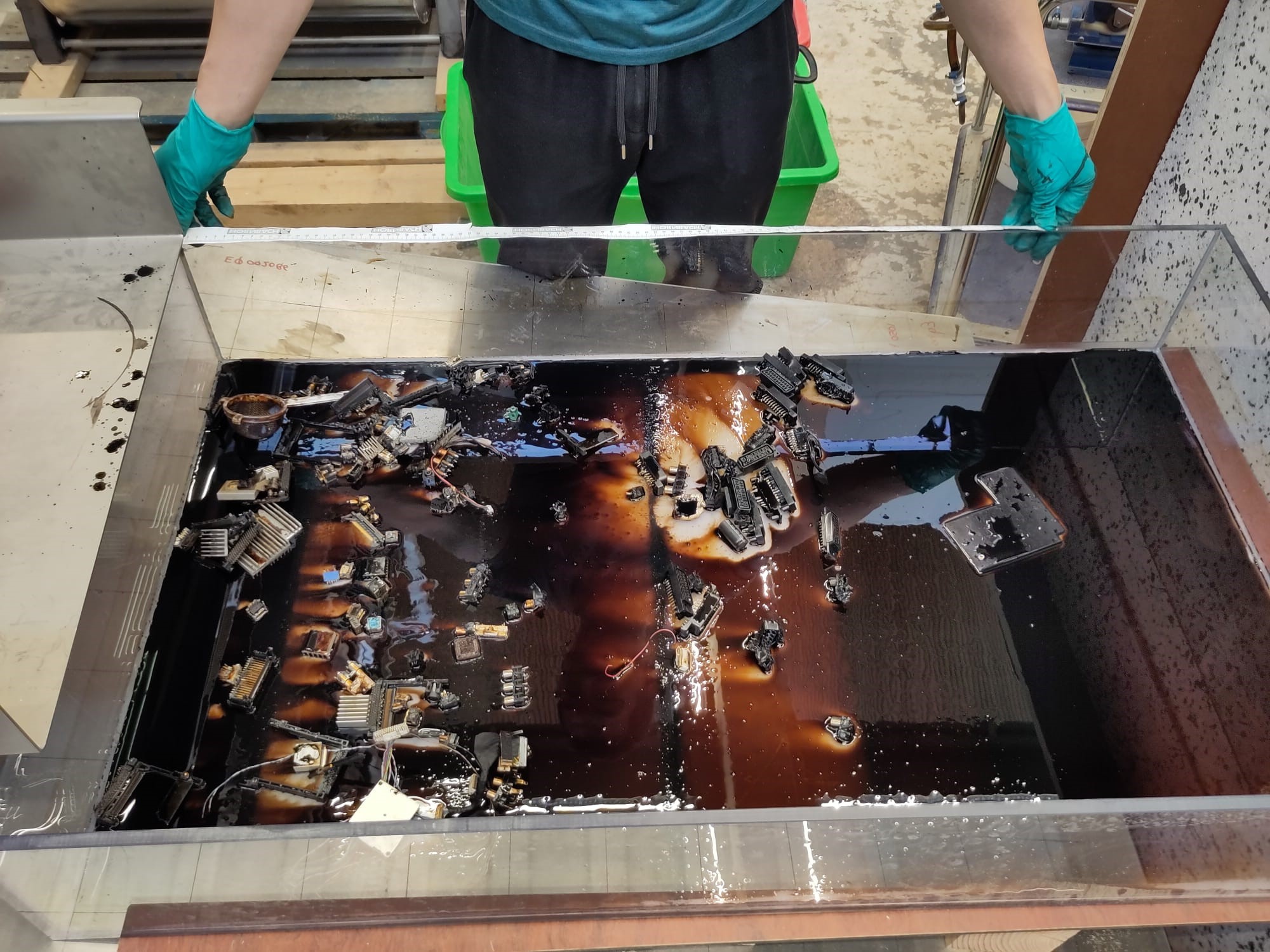
Magnetic nanoparticles
The latest and most advanced technology is the magnetic density separator (MDS). Rem had previously designed this technique to separate plastics according to minimal density differences Post-doc Dr Lin Wang is optimising the technology to separate electrical and electronic waste.
The container in which the separation occurs looks as though it contains oil, but this is not the case. The black liquid is water containing suspended magnetic nanoparticles. A strong permanent plate magnet beneath the container exerts a pull force on the liquid that increases the density. As the magnet is at an angle, the fluid density varies. The outcome is that the parts are separated according to their density.
‘They are economical separation techniques’
This becomes clear when Wang pumps away the black liquid. To the left are relatively heavy metals like aluminium cooling fins and computer chips, while in the middle are cinch cables and other plastic and metal connectors. To the right are mostly light plastic components. The area to the left is the most interesting for the extraction of metals.
“This is a cheap separation technology,” emphasises Rem. The magnets are permanent and the only parts that use energy are some running electric engines. The MDS technology is currently the cornerstone in the sorting and reprocessing process of electrical and electronic waste. At the end, the contents of the bucket containing the mixed electronic waste is separated into 30 or 40 small containers.
As big as a city bus
The lab got an industrial MDS machine prototype in mid-December. It is as big as a city bus. Before that Wang had to keep filling and emptying the basin. Now the conveyor belt continuously removes the separated components.
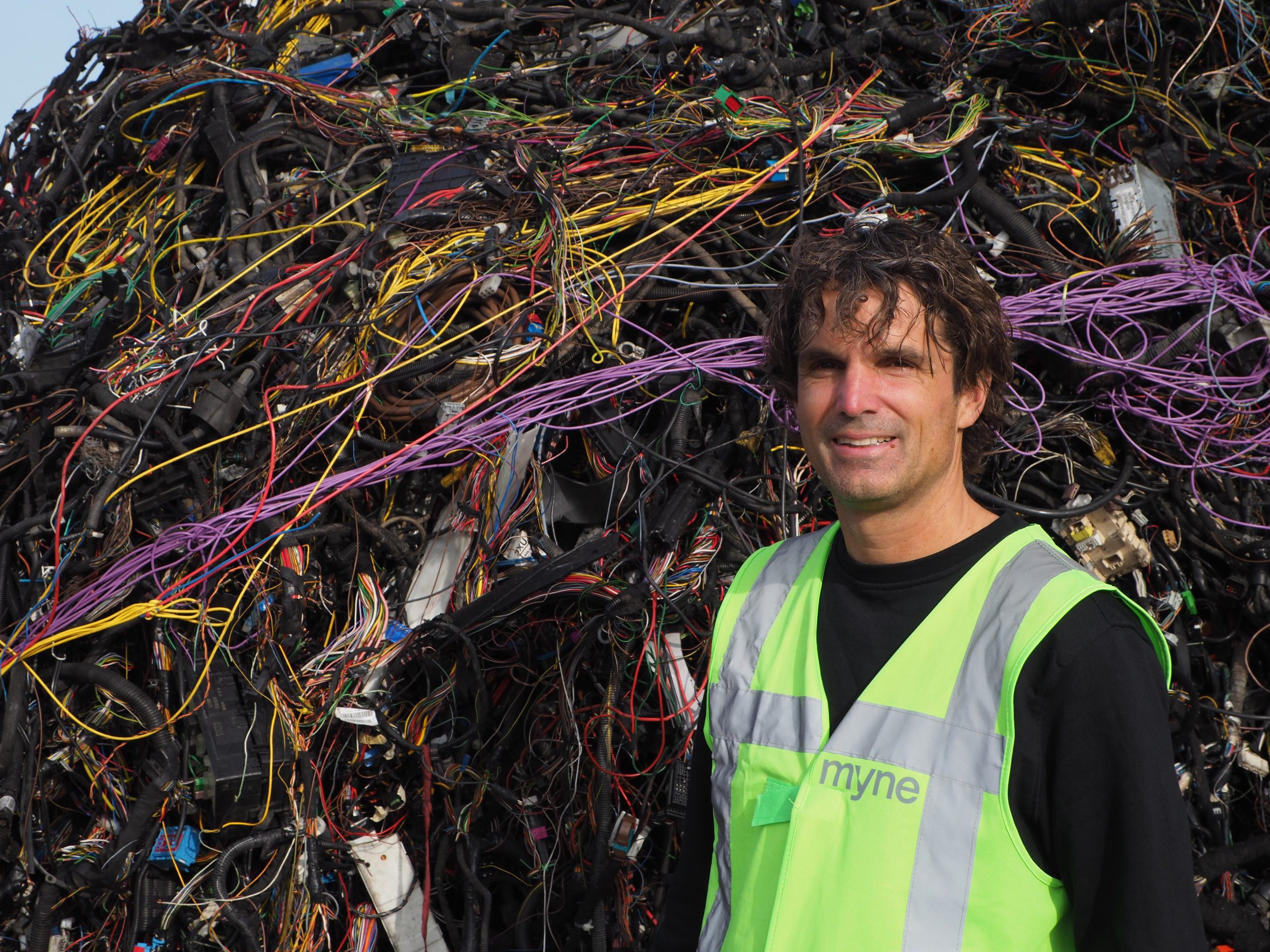
The prototype is sponsored by MYNE, formerly Reukema, a metal recycling company. This is no coincidence. Its Director and TU Delft alumnus Martijn van de Poll was at the inception of the TU Delft research with his question whether a separation technology could be designed that would be cheaper than sorting out by hand in Asia.
MYNE now buys e-waste and cable harnesses – bundles of dozens of cables of different thicknesses, often from cars – from the Netherlands, Belgium, Germany and France. This material no longer goes to Asia. Part of it now goes to the TU Delft separation lab. The testing unit is expected to process 1.5 tonnes an hour.
Van de Poll estimates that a factory with five to 10 MDS separators should be profitable. He has already invested in a separation system for aluminium alloys. The ‘Xorter’ that emerged from this is in operation in Harderwijk.
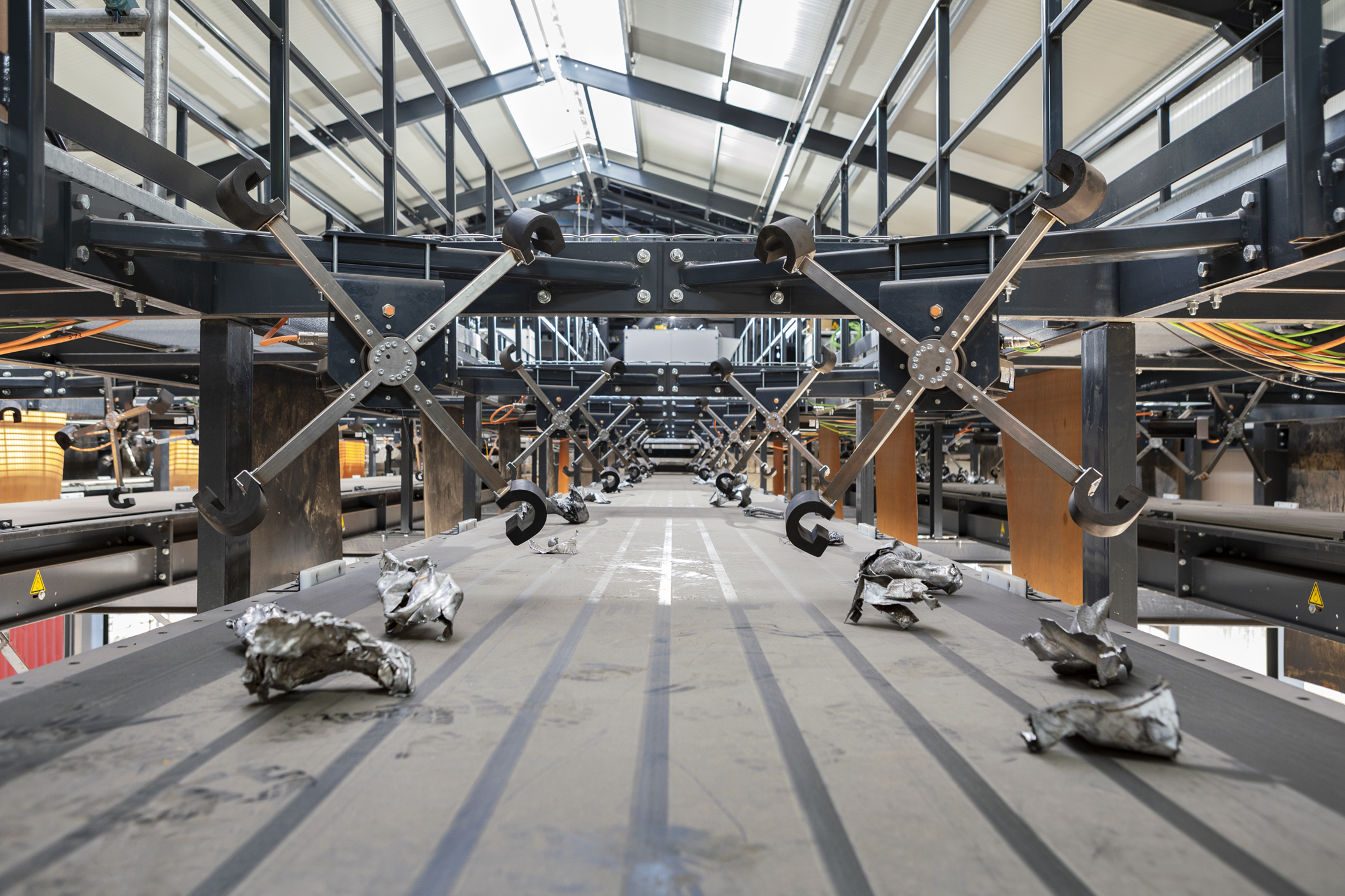
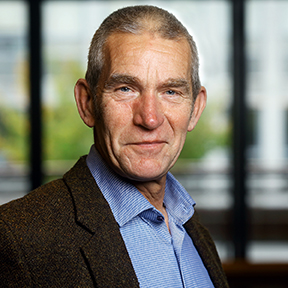
Do you have a question or comment about this article?
j.w.wassink@tudelft.nl
Comments are closed.