“I just scratched the surface. I now see that there are many more questions to be answered,” says Dr. Bénédicte Lebreton, from France, looking back on her two years of research at TU Delft.
She participated in a large project that’s looking for greener ways of producing semi-synthetic antibiotics.
The fungus Penicilium chrysogenum has been used to produce penicillin for about fifty years. Annually, more than 5000 tons are produced at DSM, which has a large plant in Delft. However, continuous improvements must be made to the production process to ensure it remains profitable and environmentally friendly.
Lebreton took part in a large project, partially financed by the Dutch Ministry of Economic Affairs, in which five research groups from four Dutch universities worked together with DSM researchers to improve the production process of semi-synthetic antibiotics. Two research groups from TU Delft’s Kluyver Biotechnology laboratory participated in this Chemferm project.
Pencilium chrysogenum fungus produces penicillin G, a raw material for producing semi-synthetic penicillin. By replacing phenylacetic acid (a side chain of penicillin G) with other molecules, different semi-synthetic penicillins can be produced with specific properties, such as increased effectiveness against bacteria that causes certain diseases.
In this process, DSM wants to replace the use of chemical process steps with ‘enzyme catalysed’ process steps (an enzyme is a protein capable of catalysing specific reactions), thus offering the possibility of improving material usage and reducing the number of process operations. However, changing one step in the process might have significant implications for subsequent operational steps, so DSM needed more fundamental knowledge of the various process steps, which in turn would help them to predict possible changes and make the necessary adjustments.
“Such a project is an exciting and challenging context to work in, because many people are involved at different levels of the production process. Research at the universities and DSM complemented each other quite well,” says Lebreton. “It’s important for universities to have research projects linked to companies, which must confront concrete industrial problems and bottlenecks. In this project, the university groups were given the freedom to determine how they conducted their own research.”
Lebreton, whose research focused on finding new ways to improve the crystallisation process of ampicillin, studied the effect impurities have on the crystallisation process, examining kinetics, like growth rate, and product quality. With other group members, she also worked on theoretical models describing crystallisation kinetics.
However, because her research was conducted for a private company, she cannot reveal her exact findings. “Crystallisation is a complex process, influenced by many parameters, from process parameters to the bulk solution’s composition. I just scratched the surface. I now see that there are many more questions to be answered,” says Lebreton, who hopes her project will result in more projects in this area at TU Delft.
Continuing her globetrotting ways, Lebreton, whose engineering degree in France was followed by a PhD project in England, is leaving Delft in May. Her next port of call is the United States and a post-doctoral position. “Going abroad contributes to having an open mind,” she believes. “You learn so much, not only about your host country but also about your own country.”
Lebreton is happy her upcoming post-doctorate is with a company: “I’ve never worked on the recovery process at a company. I’m looking forward to gaining more experience of industrial challenges and studying processes from a company point of view, which is important for applied research.”
“I just scratched the surface. I now see that there are many more questions to be answered,” says Dr. Bénédicte Lebreton, from France, looking back on her two years of research at TU Delft. She participated in a large project that’s looking for greener ways of producing semi-synthetic antibiotics.
The fungus Penicilium chrysogenum has been used to produce penicillin for about fifty years. Annually, more than 5000 tons are produced at DSM, which has a large plant in Delft. However, continuous improvements must be made to the production process to ensure it remains profitable and environmentally friendly.
Lebreton took part in a large project, partially financed by the Dutch Ministry of Economic Affairs, in which five research groups from four Dutch universities worked together with DSM researchers to improve the production process of semi-synthetic antibiotics. Two research groups from TU Delft’s Kluyver Biotechnology laboratory participated in this Chemferm project.
Pencilium chrysogenum fungus produces penicillin G, a raw material for producing semi-synthetic penicillin. By replacing phenylacetic acid (a side chain of penicillin G) with other molecules, different semi-synthetic penicillins can be produced with specific properties, such as increased effectiveness against bacteria that causes certain diseases.
In this process, DSM wants to replace the use of chemical process steps with ‘enzyme catalysed’ process steps (an enzyme is a protein capable of catalysing specific reactions), thus offering the possibility of improving material usage and reducing the number of process operations. However, changing one step in the process might have significant implications for subsequent operational steps, so DSM needed more fundamental knowledge of the various process steps, which in turn would help them to predict possible changes and make the necessary adjustments.
“Such a project is an exciting and challenging context to work in, because many people are involved at different levels of the production process. Research at the universities and DSM complemented each other quite well,” says Lebreton. “It’s important for universities to have research projects linked to companies, which must confront concrete industrial problems and bottlenecks. In this project, the university groups were given the freedom to determine how they conducted their own research.”
Lebreton, whose research focused on finding new ways to improve the crystallisation process of ampicillin, studied the effect impurities have on the crystallisation process, examining kinetics, like growth rate, and product quality. With other group members, she also worked on theoretical models describing crystallisation kinetics.
However, because her research was conducted for a private company, she cannot reveal her exact findings. “Crystallisation is a complex process, influenced by many parameters, from process parameters to the bulk solution’s composition. I just scratched the surface. I now see that there are many more questions to be answered,” says Lebreton, who hopes her project will result in more projects in this area at TU Delft.
Continuing her globetrotting ways, Lebreton, whose engineering degree in France was followed by a PhD project in England, is leaving Delft in May. Her next port of call is the United States and a post-doctoral position. “Going abroad contributes to having an open mind,” she believes. “You learn so much, not only about your host country but also about your own country.”
Lebreton is happy her upcoming post-doctorate is with a company: “I’ve never worked on the recovery process at a company. I’m looking forward to gaining more experience of industrial challenges and studying processes from a company point of view, which is important for applied research.”
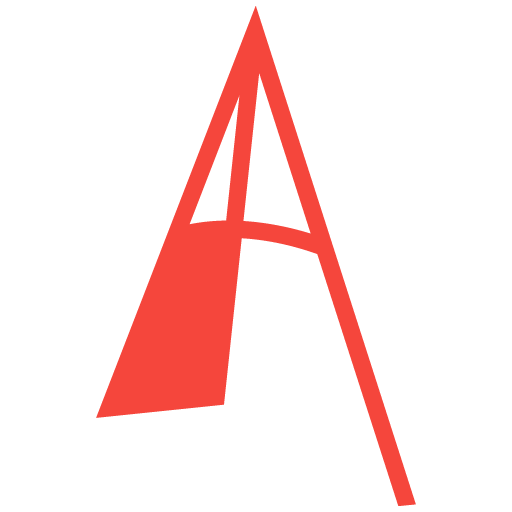
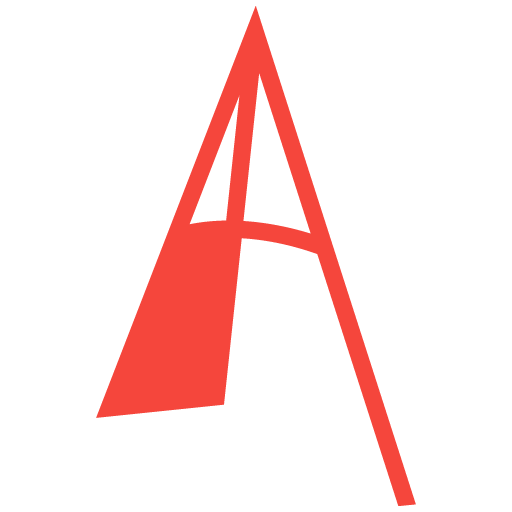
Comments are closed.