Een laagje zirkonia kan mechanische onderdelen behoeden voor al te snelle aftakeling. Het materiaal laat zich echter niet zomaar vastpinnen. Met wat nikkel ertussen lukt dat aardig, ontdekte materiaalkundige Erik Vegter.
Alles slijt. Hoe soepel de lagers van een machine ook rollen, eens zijn ze op. Nu is het altijd vervelend als apparaten door slijtage kapot gaan, maar in bepaalde situaties is stilstand wel erg ongewenst. Zoals in de chemische industrie, waar een stilstaande machine het hele productieproces kan lamleggen. Juist in die omgeving krijgt de apparatuur het zwaar voor de kiezen. Hoge temperaturen en agressieve vloeistoffen vergen het uiterste van de pompen, afsluiters en keerkleppen.
Een eenvoudige manier om de standtijd van machines te vergroten, is de zwaarbelaste onderdelen van harder materiaal te maken. Iets dat behalve slijtvast, bij voorkeur ook bestand is tegen hitte en corrosie. Voor deze toepassing gooit technische keramiek hoge ogen. Dit veelal uit metaaloxiden gebakken hi-techmateriaal, druppelt ook langzaam door in het huishouden. De duurdere mengkranen hebben steeds vaker keramische afsluiters. Nooit meer lekkende kranen, beloven de fabrikanten. Of in elk geval een stuk later.
Keramiek heeft helaas een nadeel: het materiaal is erg op zichzelf. Er zijn weinig manieren om het ergens anders aan vast te maken. ,,Je kunt het natuurlijk verlijmen, maar in chemisch agressieve stoffen lost zo’n lijmlaag vaak op. Dat is dus geen oplossing”, vat ir. Erik Vegter het probleem samen. Hij bekeek de afgelopen twee jaar bij Materiaalkunde een alternatieve verbindingsmethode, het diffusielassen. Aanstaande maandag promoveert hij op dit onderzoek.
De diffusiebinding is al een oude techniek, legt Vegter uit. ,,Als twee samengeperste stukken metaal voldoende wrijvingshitte ondervinden, hechten ze op een gegeven moment ook aan elkaar. Datzelfde principe heb ik gebruikt om zirkonia aan andere materialen vast te maken.”
Zirkonia, een oxide van het metaal zirkonium, heeft het uiterlijk van grijs pvc. Een mooi keramisch materiaal, meent de promovendus. ,,Het is één van de betere. Zeer sterk, terwijl het meeste technisch keramiek vrij broos is. Maar zirkonia is wel tot vijf keer zo duur als de gangbare constructiematerialen. Je moet het dus alleen gebruiken waar het echt nodig is. En daarvoor moet je zirkonia ook aan andere materialen kunnen verbinden.”
Gewoon lassen gaat helaas niet. Bij het gangbare booglassen smelten de te verbinden materialen plaatselijk, waardoor de materiaalstructuur verandert. Onacceptabel bij het zorgvuldig gebakken keramiek. Bovendien werpt het hoge smeltpunt van zirkonia, 2600 graden celsius, een praktische drempel op.
Berglandschap
De diffusiemethode die Vegter heeft onderzocht, laat het materiaalwel intact. Het keramiek wordt in een oven onder hoge druk en temperatuur op een ander materiaal geperst. Hierbij treedt geen smelting op, maar na enige tijd is de naadloze verbinding een feit.
Over wat er op het grensvlak van de twee materialen gebeurt, zijn de geleerden het niet eens. Dat is nog terra incognita. ,,Eerst zitten ze natuurlijk los van elkaar. Je hebt namelijk altijd te maken met oppervlakteruwheden, hoe mooi ze ook gepolijst zijn. Het blijft een soort berglandschap.” Onder toenemende druk vindt er plastische deformatie plaats. De microscopische pieken en dalen worden langzaam in elkaar gedrukt. ,,De atomen van het ene materiaal lopen dan over naar het andere, een proces dat diffunderen heet. Vandaar de term diffusielassen”, licht Vegter toe. ,,En als je maar lang genoeg wacht, worden alle gaten wel gedicht.”
Als de oppervlakken elkaar tot op drietiende nanometer zijn genaderd, doet er zich iets opmerkelijks voor. De overgang tussen het zirkonium en het andere materiaal lijkt te vervagen. Het grensvlak lost als het ware op in de materiaalstructuur.
,,Je zit dan al op het roosterniveau. De elektronenbanen van de materialen beginnen te overlappen, en ze zitten opeens aan elkaar vast. Maar hoe je dat nu moet zien? Een fysisch effect als de Vanderwaals-kracht is in elk geval niet voldoende om de sterkte van de verbinding te verklaren. Ik denk daarom toch dat de materialen hun elektronenbanen delen. Maar eigenlijk gaat deze vraag ook op voor gewone materialen. Daar zitten altijd imperfecties als korrelgrenzen in, maar ze blijven toch intact. Over de precieze aard van de verbinding heb ik in mijn onderzoek echter geen uitsluitsel kunnen geven. ”
Dat maakt ook niet zoveel uit, want Vegters onderzoeksvraag is vrij praktisch: hoe las je zirkonia vast aan iets anders? Een directe diffusieverbinding blijkt in elk geval onmogelijk. Zirkonia en bijvoorbeeld roestvast staal krimpen bij verhitting en afkoeling zeer verschillend. Hierdoor blijven hoge restspanningen in het keramiek achter, wat funest is voor de sterkte van het materiaal. Een eye-opener, bekent de materiaalkundige.
Bakproefjes
1 Doorsnede van een zirkonia-nikkel-siliciumnitride diffusieverbinding.
,,Ik had niet verwacht dat de restspanningen zo’n belangrijke rol zouden speelden. Die hebben eigenlijk meer invloed dan de fysisch-chemische kant van de zaak. Dat is ook een algemene conclusie die ik heb getrokken. Het verbinden lukt altijd, maar het zijn de restspanningen die de doorslag geven.”
Vegter had al snel door dat hij een tussenlaag nodig had. Hij koos voor nikkel. ,,Dat materiaal voldoet redelijk in de meeste toepassingen. Die nikkellaag fungeert als een soort kauwgom, en vangt een groot deel van de krimpspanningen op.”
Met het nikkellaagje plakte hij zirkonia aan roestvast staal, siliciumnitride en aan zirkonia zelf. Om een idee te krijgen van de optimale procescondities voerde Vegter ongeveer 400 bakproefjes uit bij verschillende druk, tijd en temperatuurprofielen. Daarnaast stelde hij een eenvoudig eindig-elementenmodel op om meer greep te krijgen op het krimpgedrag. ,,Met het model kun je de krimp bepalen als je het baksel van duizend graden in stappen afkoelt totkamertemperatuur. Dat heb ik natuurlijk vergeleken met mijn proefnemingen, en de uitkomsten zijn goed te relateren aan het optredende breukgedrag.”
De honderden gebakken blokjes werden op afschuiving belast om de sterkte te beproeven. Bijna lopendebandwerk, maar dat leidde wel tot een inzicht. Vegter: ,,Ik dacht dat de dikte van de tussenlaag nog wat zou uitmaken. Hoe dikker, hoe beter had ik verwacht. Dan heb je tenslotte meer buffermateriaal. Maar dat blijkt eigenlijk niet zoveel invloed op de sterkte te hebben.”
Vegter sloot zijn onderzoek begin dit jaar af. Het afronden van zijn proefschrift heeft geen bloed, zweet en tranen gekost. ,,Ik had eerder een aantal artikelen over dit onderwerp geschreven, dus ik had de smaak al een beetje te pakken. En ik heb geen hekel aan schrijven, want het heeft een groot voordeel: dan weet je namelijk pas wat je allemaal hebt.”
Vegter ziet nog wel enige zaken die om een oplossing vragen. ,,Deze verbindingstechniek moet nog sneller verlopen. Het bakproces duurt nu vier tot vijf uur. Dat is echt te lang. Om de zaak te versnellen zou de verhittingsmethode nog verbeterd kunnen worden. Je kunt de tussenlaag bijvoorbeeld snel verwarmen door er sterke stroom doorheen te sturen.”
Maar daar zal Vegter zich niet meer mee bezighouden. ,,Ik ben nu op zoek naar een baan buiten de universiteit. Niet dat het onderzoekswerk me tegenstond, maar ik wil niet dat ik nu al weet wat ik volgend jaar ga doen.”
Alles slijt. Hoe soepel de lagers van een machine ook rollen, eens zijn ze op. Nu is het altijd vervelend als apparaten door slijtage kapot gaan, maar in bepaalde situaties is stilstand wel erg ongewenst. Zoals in de chemische industrie, waar een stilstaande machine het hele productieproces kan lamleggen. Juist in die omgeving krijgt de apparatuur het zwaar voor de kiezen. Hoge temperaturen en agressieve vloeistoffen vergen het uiterste van de pompen, afsluiters en keerkleppen.
Een eenvoudige manier om de standtijd van machines te vergroten, is de zwaarbelaste onderdelen van harder materiaal te maken. Iets dat behalve slijtvast, bij voorkeur ook bestand is tegen hitte en corrosie. Voor deze toepassing gooit technische keramiek hoge ogen. Dit veelal uit metaaloxiden gebakken hi-techmateriaal, druppelt ook langzaam door in het huishouden. De duurdere mengkranen hebben steeds vaker keramische afsluiters. Nooit meer lekkende kranen, beloven de fabrikanten. Of in elk geval een stuk later.
Keramiek heeft helaas een nadeel: het materiaal is erg op zichzelf. Er zijn weinig manieren om het ergens anders aan vast te maken. ,,Je kunt het natuurlijk verlijmen, maar in chemisch agressieve stoffen lost zo’n lijmlaag vaak op. Dat is dus geen oplossing”, vat ir. Erik Vegter het probleem samen. Hij bekeek de afgelopen twee jaar bij Materiaalkunde een alternatieve verbindingsmethode, het diffusielassen. Aanstaande maandag promoveert hij op dit onderzoek.
De diffusiebinding is al een oude techniek, legt Vegter uit. ,,Als twee samengeperste stukken metaal voldoende wrijvingshitte ondervinden, hechten ze op een gegeven moment ook aan elkaar. Datzelfde principe heb ik gebruikt om zirkonia aan andere materialen vast te maken.”
Zirkonia, een oxide van het metaal zirkonium, heeft het uiterlijk van grijs pvc. Een mooi keramisch materiaal, meent de promovendus. ,,Het is één van de betere. Zeer sterk, terwijl het meeste technisch keramiek vrij broos is. Maar zirkonia is wel tot vijf keer zo duur als de gangbare constructiematerialen. Je moet het dus alleen gebruiken waar het echt nodig is. En daarvoor moet je zirkonia ook aan andere materialen kunnen verbinden.”
Gewoon lassen gaat helaas niet. Bij het gangbare booglassen smelten de te verbinden materialen plaatselijk, waardoor de materiaalstructuur verandert. Onacceptabel bij het zorgvuldig gebakken keramiek. Bovendien werpt het hoge smeltpunt van zirkonia, 2600 graden celsius, een praktische drempel op.
Berglandschap
De diffusiemethode die Vegter heeft onderzocht, laat het materiaalwel intact. Het keramiek wordt in een oven onder hoge druk en temperatuur op een ander materiaal geperst. Hierbij treedt geen smelting op, maar na enige tijd is de naadloze verbinding een feit.
Over wat er op het grensvlak van de twee materialen gebeurt, zijn de geleerden het niet eens. Dat is nog terra incognita. ,,Eerst zitten ze natuurlijk los van elkaar. Je hebt namelijk altijd te maken met oppervlakteruwheden, hoe mooi ze ook gepolijst zijn. Het blijft een soort berglandschap.” Onder toenemende druk vindt er plastische deformatie plaats. De microscopische pieken en dalen worden langzaam in elkaar gedrukt. ,,De atomen van het ene materiaal lopen dan over naar het andere, een proces dat diffunderen heet. Vandaar de term diffusielassen”, licht Vegter toe. ,,En als je maar lang genoeg wacht, worden alle gaten wel gedicht.”
Als de oppervlakken elkaar tot op drietiende nanometer zijn genaderd, doet er zich iets opmerkelijks voor. De overgang tussen het zirkonium en het andere materiaal lijkt te vervagen. Het grensvlak lost als het ware op in de materiaalstructuur.
,,Je zit dan al op het roosterniveau. De elektronenbanen van de materialen beginnen te overlappen, en ze zitten opeens aan elkaar vast. Maar hoe je dat nu moet zien? Een fysisch effect als de Vanderwaals-kracht is in elk geval niet voldoende om de sterkte van de verbinding te verklaren. Ik denk daarom toch dat de materialen hun elektronenbanen delen. Maar eigenlijk gaat deze vraag ook op voor gewone materialen. Daar zitten altijd imperfecties als korrelgrenzen in, maar ze blijven toch intact. Over de precieze aard van de verbinding heb ik in mijn onderzoek echter geen uitsluitsel kunnen geven. ”
Dat maakt ook niet zoveel uit, want Vegters onderzoeksvraag is vrij praktisch: hoe las je zirkonia vast aan iets anders? Een directe diffusieverbinding blijkt in elk geval onmogelijk. Zirkonia en bijvoorbeeld roestvast staal krimpen bij verhitting en afkoeling zeer verschillend. Hierdoor blijven hoge restspanningen in het keramiek achter, wat funest is voor de sterkte van het materiaal. Een eye-opener, bekent de materiaalkundige.
Bakproefjes
1 Doorsnede van een zirkonia-nikkel-siliciumnitride diffusieverbinding.
,,Ik had niet verwacht dat de restspanningen zo’n belangrijke rol zouden speelden. Die hebben eigenlijk meer invloed dan de fysisch-chemische kant van de zaak. Dat is ook een algemene conclusie die ik heb getrokken. Het verbinden lukt altijd, maar het zijn de restspanningen die de doorslag geven.”
Vegter had al snel door dat hij een tussenlaag nodig had. Hij koos voor nikkel. ,,Dat materiaal voldoet redelijk in de meeste toepassingen. Die nikkellaag fungeert als een soort kauwgom, en vangt een groot deel van de krimpspanningen op.”
Met het nikkellaagje plakte hij zirkonia aan roestvast staal, siliciumnitride en aan zirkonia zelf. Om een idee te krijgen van de optimale procescondities voerde Vegter ongeveer 400 bakproefjes uit bij verschillende druk, tijd en temperatuurprofielen. Daarnaast stelde hij een eenvoudig eindig-elementenmodel op om meer greep te krijgen op het krimpgedrag. ,,Met het model kun je de krimp bepalen als je het baksel van duizend graden in stappen afkoelt totkamertemperatuur. Dat heb ik natuurlijk vergeleken met mijn proefnemingen, en de uitkomsten zijn goed te relateren aan het optredende breukgedrag.”
De honderden gebakken blokjes werden op afschuiving belast om de sterkte te beproeven. Bijna lopendebandwerk, maar dat leidde wel tot een inzicht. Vegter: ,,Ik dacht dat de dikte van de tussenlaag nog wat zou uitmaken. Hoe dikker, hoe beter had ik verwacht. Dan heb je tenslotte meer buffermateriaal. Maar dat blijkt eigenlijk niet zoveel invloed op de sterkte te hebben.”
Vegter sloot zijn onderzoek begin dit jaar af. Het afronden van zijn proefschrift heeft geen bloed, zweet en tranen gekost. ,,Ik had eerder een aantal artikelen over dit onderwerp geschreven, dus ik had de smaak al een beetje te pakken. En ik heb geen hekel aan schrijven, want het heeft een groot voordeel: dan weet je namelijk pas wat je allemaal hebt.”
Vegter ziet nog wel enige zaken die om een oplossing vragen. ,,Deze verbindingstechniek moet nog sneller verlopen. Het bakproces duurt nu vier tot vijf uur. Dat is echt te lang. Om de zaak te versnellen zou de verhittingsmethode nog verbeterd kunnen worden. Je kunt de tussenlaag bijvoorbeeld snel verwarmen door er sterke stroom doorheen te sturen.”
Maar daar zal Vegter zich niet meer mee bezighouden. ,,Ik ben nu op zoek naar een baan buiten de universiteit. Niet dat het onderzoekswerk me tegenstond, maar ik wil niet dat ik nu al weet wat ik volgend jaar ga doen.”
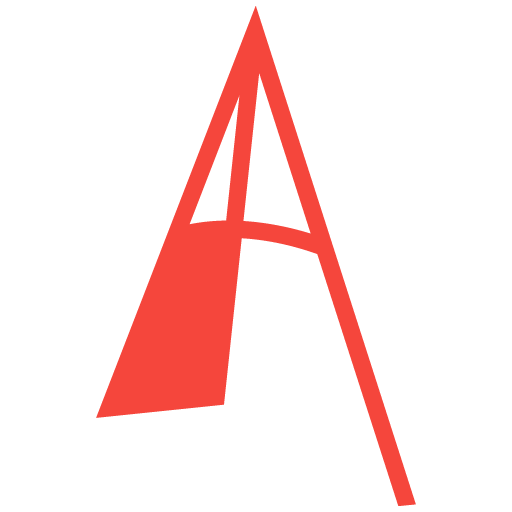
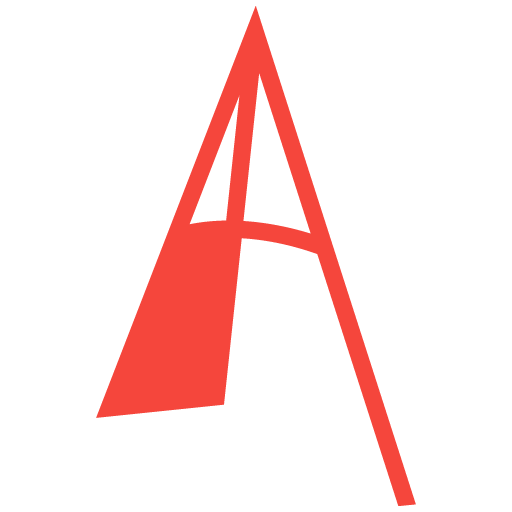
Comments are closed.