De university colleges willen hun tarief voor nieuwe studenten flink gaan opschroeven. Daarvoor moeten ze wel eerst toestemming krijgen van accreditatieorganisatie NVAO.
Het Utrechtse university college wil zijn eerstejaars vanaf september 2012 twee maal zoveel collegegeld laten betalen, meldt digitaal Universiteitsblad DUB. Nu betalen ze het wettelijke collegegeld van 1713 euro en nog eens 1100 euro voor een beurzenprogramma voor internationale studenten.
Ook andere university colleges willen hun collegegeld sterk verhogen, meldt DUB. De Roosevelt Academy in Middelburg zou als enige onder de drieduizend euro blijven.
Of de opleidingen hun collegegeld daadwerkelijk mogen verhogen hangt af van onderwijskeurmeester NVAO. Die zal de minister straks adviseren of een opleiding het “bijzondere kenmerk kleinschalig en intensief onderwijs” verdient.
De criteria waarmee de NVAO de aanvragen zal beoordelen moeten nog worden goedgekeurd door parlement en senaat.
“Haptic robots are used in cases where there is a separation between the actor and the object,” explains Pablo Estevez (MSc), a PhD student at the faculty of Mechanical, Maritime and Materials Engineering, in his fast, staccato English. “This can be in handling nuclear stuff, in working in a hot oven, under water or when the scale factor doesn’t match. Or if you want to move very large or very tiny things.” This last application – to move “very tiny things” – is what the team, under the supervision of Professor Rob Munnig Schmidt, is working on. Estevez and fellow PhD-students Patrice Lambert (MSc) and Ilhan Polat (MSc) are developing a ‘Teleoperated Microassembly Device’.
Lambert constructed a remote control (the master unit), Estevez the actuator (slave unit), and Polat ensures both units communicate. There a five wires communicating the master’s position to the slave a thousand times per second, and five wires communicating the forces from the slave back to the master unit. In addition, a video camera provides visual feedback. The operator will be able to manipulate microscopic objects with macroscopic ease. No more trembling tweezers under the microscope – a remote-operated micro assembly device will simply scale down the operator’s movements by a factor of 500 and scale up the feedback forces by the same amount. It would be the ideal tool for micro manufacturing, such as manual watch making.
The remote control consists of a platform supported by five, hinged limbs, each of which is coupled to an electromotor via a coupled encoder. The platform itself can be turned 45 degrees in either direction and can be squeezed. These motions, together with the platform’s three-dimensional position, are encoded in the positions of five electro-engines situated at the base of the master unit. Lambert underlines the importance of having the largest part of the unit’s mass concentrated in the device’s immobile base. The movable part should be as light and as stiff as possible. Lambert’s remote control has since been patented as PentaG, with the G standing for ‘grip’.
“Ah! Watch out for the box,” Estevez shouts to a colleague. The large, nearly empty plastic box contains a pivotal and sensitive part of the slave unit that Estevez has been constructing: the force sensors.
The movements of the engines in the master device will be converted into the currents through the actuator’s three sets of paired coils. Meanwhile, a clever contraption made of coils uses three tiny flat magnets to support an aluminium disk situated where the coils are positioned. The vertical coils lift the platform by Lorentz force, and the horizontal coils within the vertical coils rotate the platform over a small angle. “Just like an amplifier driving your speaker,” Estevez explains. In this way, the platform can be moved 0.2 millimetres in any direction and can be turned about one degree. For larger movements, a courser system should position the slave unit at more or less the correct position, after which the fine system can take over control.
A commercially available demo unit is already capable of making a virtual ball feel like rubber, steel or sand. Estevez hopes for the same result with his newly designed piezo force sensor. Physical contact with the probe will change the values of the built-in piezo resistors, translating into forces on the hand of the operator. Hence, a doctor injecting a living cell will actually feel what he is doing.
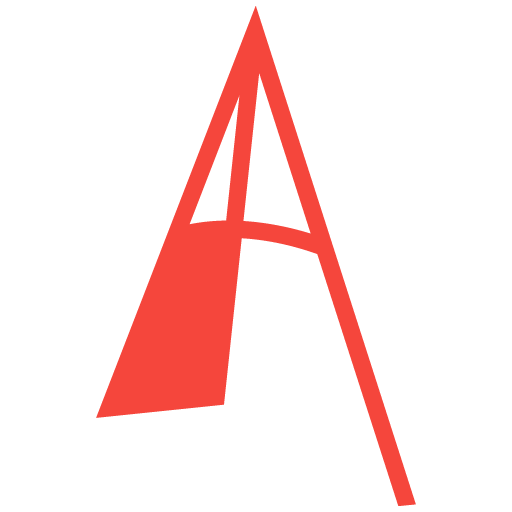
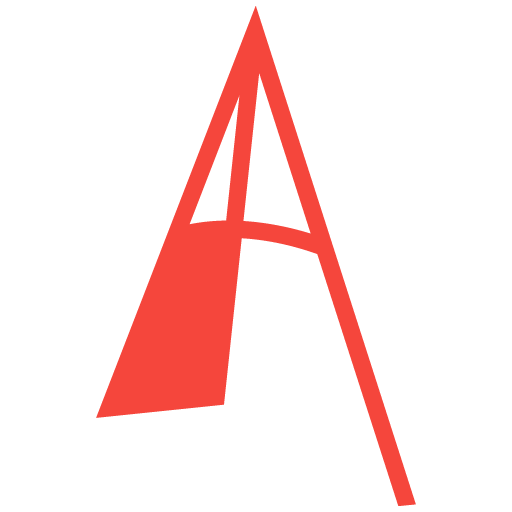
Comments are closed.